Sidérurgie
Notre offre pour l’industrie sidérurgique
Bien que les matériaux réfractaires ne représentent qu'une faible part du coût total de la production de fer et d'acier, leur fiabilité est essentielle pour l’efficacité des processus.
Un soutien approprié en matière de technologie réfractaire peut prolonger les intervalles entre les arrêts de production, réduire les coûts de maintenance et améliorer l'efficacité énergétique du processus, contribuant ainsi à atteindre les objectifs de durabilité. Notre mission est de soutenir nos partenaires précisément là où leurs installations en ont besoin – depuis les études d'ingénierie, en passant par la sélection conjointe des solutions les plus efficaces en matière de matériaux et de technologies d'installation, la logistique vers n’importe quelle destination, jusqu’au montage ou sa supervision, ainsi que l’assistance post-installation. Nous croyons que la fiabilité de nos produits et de nos services, associée à notre accompagnement complet, contribuera à réduire les temps d’arrêt et à rendre nos partenaires plus compétitifs et durables grâce à notre technologie réfractaire ! Découvrez notre offre complète pour l'industrie sidérurgique, qui comprend une large gamme de services et de produits : briques et bétons chamottés, à base d’andalousite, de mullite et d’alumine, ainsi que matériaux isolants.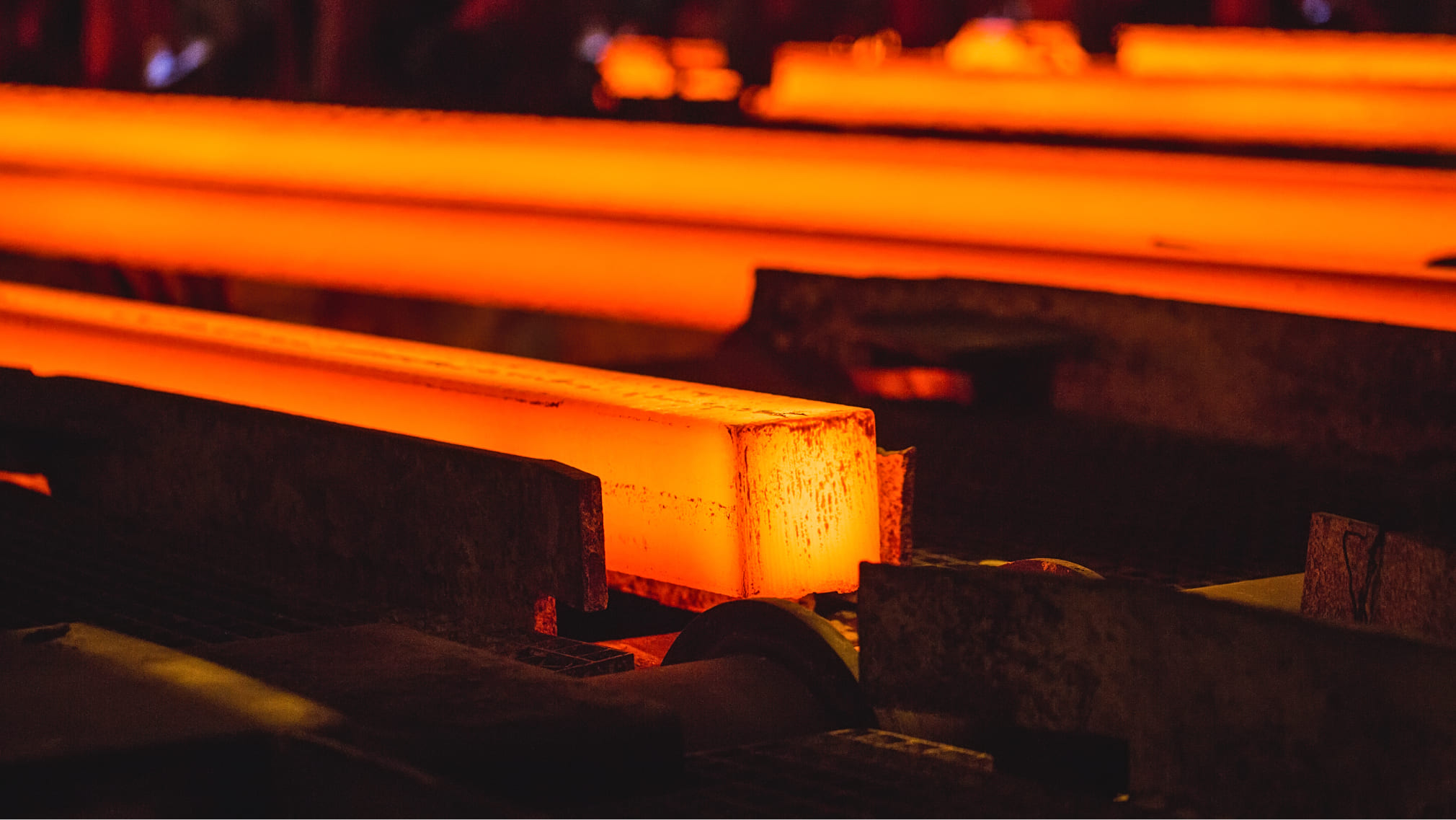
Comment pouvons-nous vous aider?
Nous concevons
- Calculs thermiques des zones sélectionnées de fours et de poches à l’aide de Simu-Therm.
- Conception de revêtements réfractaires pour poches torpilles, poches à fonte, cowpers de hauts fourneaux, fours à sole mobile et fours à sole amovible (plans de composants, fiches techniques des matériaux, nomenclatures, instructions de montage, courbes de séchage, consignes de mise en service, instructions de maintenance).
- Projets de composants préfabriqués tels que : voûtes de fours électriques, blocs brûleurs, blocs de coulée, blocs pour électrodes, modules muraux, modules de voûte, sole de fours de laminoirs.
Nous produisons et livrons
- Ancres céramiques à haute résistance thermique et mécanique, en andalousite et bauxite (60–85 % d’Al₂O₃).
- Éléments coulés préfabriqués de grandes dimensions : voûtes, cloisons, pièces de passage, ainsi que blocs de sole.
- Ensembles de goulottes pour la coulée par siphon, produits par pressage semi-sec.
- Briques isolantes et matelas de fibres céramiques pour les couches isolantes des fours et des poches.
- Blocs grillagés chamottés et à haute teneur en alumine pour le remplissage des cowpers de hauts fourneaux.
- Bétons réfractaires (de type conventionnel à ultra-bas en ciment) et isolants, ainsi que des masses de réparation à chaud.
Nous réalisons l'installation
- Planification et gestion des chantiers, y compris l’achat de tous les matériaux auxiliaires nécessaires (coffrages, pièces métalliques, consoles, isolants fibreux).
- Démontage et montage de revêtements céramiques dans les poches torpilles, les poches à fonte, les cowpers de hauts fourneaux et les fours de laminoirs.
- Assistance technique et supervision par des professionnels expérimentés en maçonnerie et en coulage de revêtements réfractaires.
Fours et autres applications à haute température
Le four de grillage pour boulettes de minerai de fer
Le four de grillage permet de frittar les boulettes préformées à partir de concentré de minerai de fer. Le four rotatif, qui constitue le cœur de l’installation, comporte trois zones principales : préchauffage, cuisson et refroidissement. Pour garantir un fonctionnement continu et fiable du four, les matériaux réfractaires utilisés dans le revêtement doivent présenter une excellente résistance aux chocs thermiques, une grande résistance à l’abrasion ainsi qu’à la flexion et à la compression (en raison des contraintes dues à la rotation du four et à la pression du matériau en charge). PCO propose une large gamme de matériaux chamottés et à haute teneur en alumine, disponibles aux formats standards (ISO, VDZ) ou sur mesure. Les plus grands fours de grillage pour lesquels PCO fournit les réfractaires atteignent un diamètre de 8 mètres. En aval du four rotatif se trouve le refroidisseur à boulettes, qui peut être revêtu de bétons, de masses à damer ou d’éléments préfabriqués prêts à être installés. Les matériaux utilisés dans cette zone sont choisis pour leur bonne résistance aux chocs thermiques et à l’abrasion.
Portée: Conception du garnissage Fourniture des matériaux réfractaires Services de montage du garnissage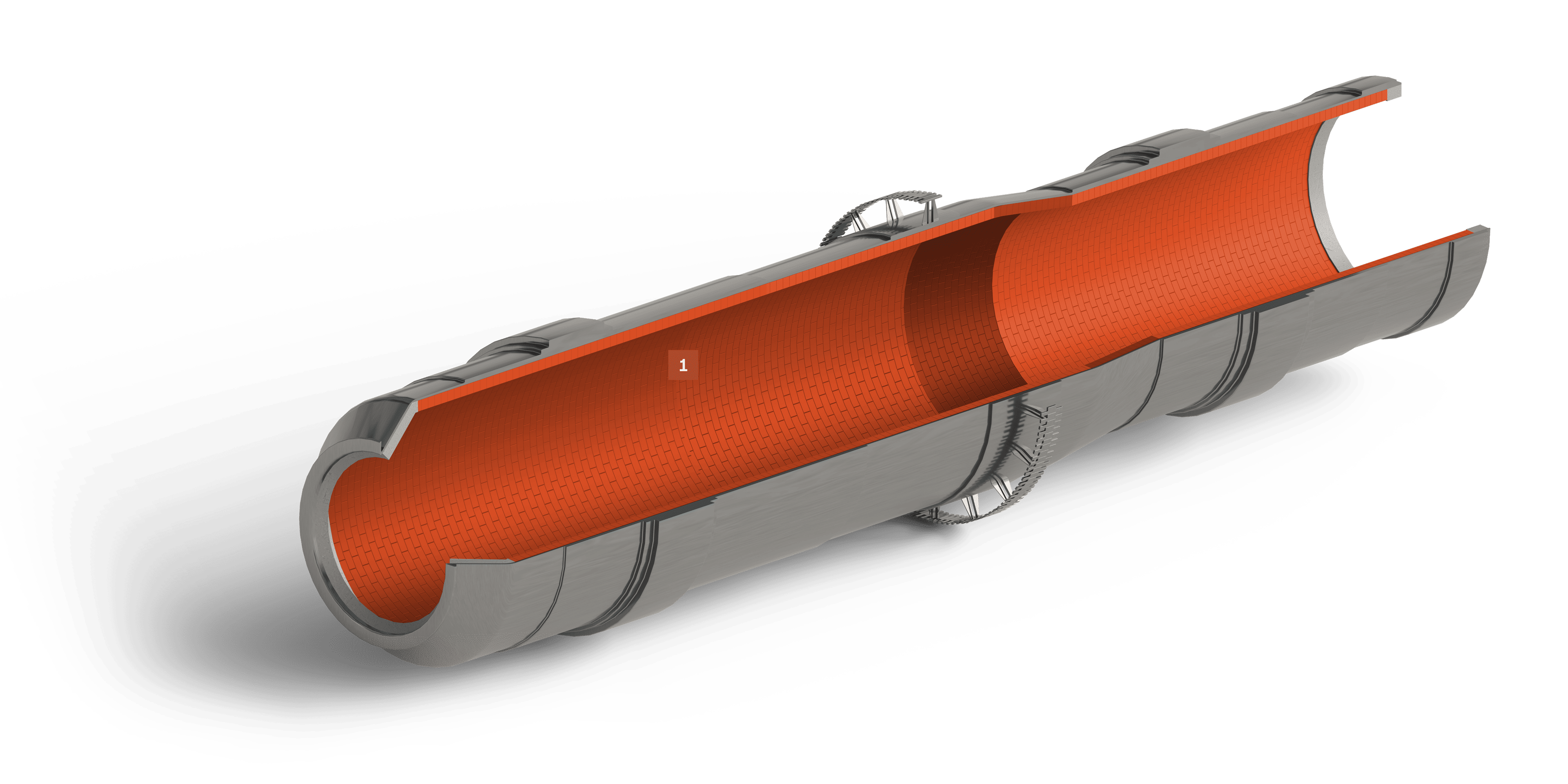
La majorité des fours rotatifs utilisés pour la fabrication de boulettes de minerai emploient des briques à haute teneur en alumine, souvent composées de 60 à 80 % d’Al₂O₃. Cette composition est sélectionnée pour sa capacité à maintenir une résistance élevée à des températures pouvant atteindre 1400 °C dans la zone de cuisson, ainsi que pour sa très bonne résistance aux chocs thermiques et à l’abrasion. Pour maîtriser ces contraintes, on recourt généralement à des briques soigneusement conçues avec un système d’emboîtement, à une installation de qualité réalisée à l’aide d’un mortier adapté et de joints de dilatation correctement positionnés, et, lorsque cela est possible, à un système composite comprenant une couche isolante destinée à réduire les contraintes thermiques.
Comment pouvons-nous vous aider ?
Vous souhaitez recevoir un conseil gratuit ou poser une question sur le choix d’un revêtement réfractaire? Laissez-nous vos coordonnées – nous vous rappellerons!
Contactez-nousQuel matériau utiliser pour réduire les dépôts de poussière ou de cendres et minimiser l’écaillage du revêtement ?
Quel produit assurera la résistance mécanique suffisante pour un four de très grand diamètre ?
Comment protéger le revêtement contre les forts gradients thermiques dus au chauffage irrégulier et aux phases de refroidissement du four ?
Le cowper du haut fourneau
Le cowper joue un rôle essentiel dans la sidérurgie : il chauffe l’air injecté dans le haut fourneau jusqu’à des températures avoisinant les 1000 °C. Ce processus continu exige une maîtrise précise du flux gazeux et une distribution homogène de la chaleur. Le revêtement réfractaire est soumis à des variations thermiques brutales, à la corrosion chimique des gaz de combustion et à l’abrasion causée par les particules solides, ce qui impose l’usage de matériaux hautement résistants. Dans les couches supérieures, on utilise des grilles en silice, réputées pour leur stabilité chimique et leur résistance aux déformations thermiques. Dans les zones inférieures, les produits chamottés sont employés pour leur résistance aux hautes températures et aux sollicitations mécaniques. Les éléments en andalousite, placés dans les zones hautes, assurent une bonne stabilité dimensionnelle et une excellente tenue chimique. Les couches isolantes produites par PCO – notamment les briques isolantes – permettent de limiter les pertes thermiques, d’augmenter l’efficacité énergétique du système et de garantir la fiabilité ainsi que la longévité de l’installation, même dans des conditions industrielles extrêmes.
Portée: Conception du garnissage Fourniture des matériaux réfractaires Services de montage du garnissage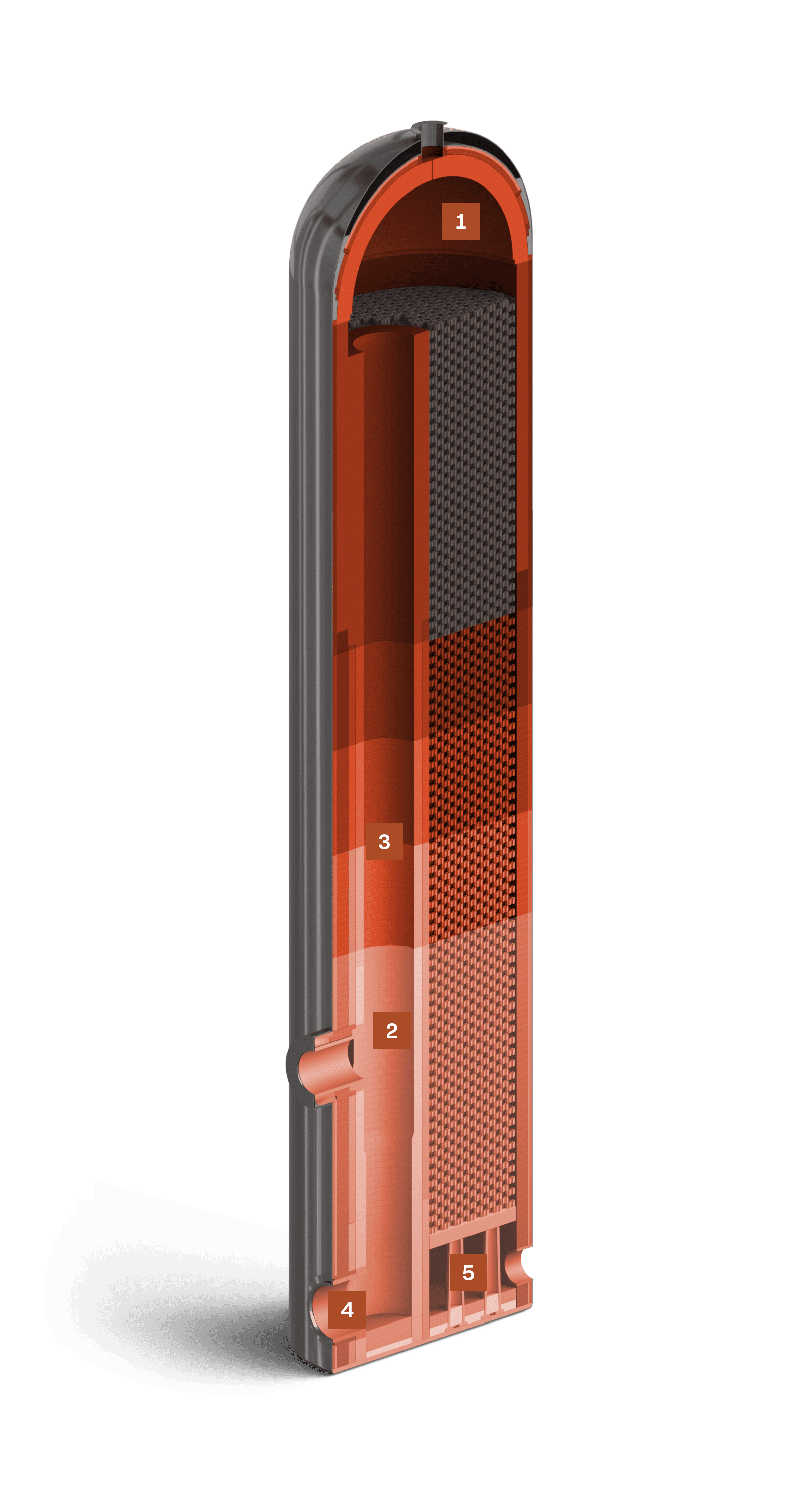
Dans le dôme du cowper, où les températures atteignent 1300 à 1400 °C, les matériaux réfractaires doivent résister à une exposition intense à des atmosphères oxydantes et réductrices, à des charges mécaniques importantes et à des variations thermiques brutales entraînant des chocs thermiques et une dégradation structurelle. Pour assurer la durabilité du revêtement, il est essentiel d’utiliser des matériaux présentant un fort degré de formation de mullite. Les produits ANDALUX, reconnus pour leur stabilité dimensionnelle, leur faible porosité et leur excellente résistance à la corrosion, s’avèrent particulièrement efficaces dans cette zone critique. Le choix précis des matériaux contribue directement à la fiabilité de l’installation et à l’efficacité du processus thermique.
Cette partie du cowper est soumise à des températures extrêmes, à une atmosphère chimique agressive et à des chocs thermiques sévères. L’utilisation de produits riches en mullite, comme les ANDALUX, permet de garantir une stabilité dimensionnelle même sous de fortes charges thermiques. Dans les zones légèrement moins sollicitées thermiquement, les matériaux SUPERTON sont privilégiés pour leur haute résistance mécanique, assurant la durabilité du revêtement. En complément, les matériaux isolants ISOLUX réduisent efficacement les pertes de chaleur, ce qui améliore l’efficacité énergétique de l’ensemble du système et prolonge la durée de vie de l’installation.
Les blocs grillagés du régénérateur jouent un rôle crucial dans l’échange thermique en permettant le préchauffage efficace de l’air dirigé vers le haut fourneau. Les matériaux utilisés dans cette partie doivent avoir : une résistance exceptionnelle aux hautes températures, une bonne tenue face aux gaz agressifs, et une robustesse mécanique. Selon la zone, des grilles chamottées ou à base d’andalousite sont utilisées pour garantir la stabilité de la structure sur le long terme.
Les brûleurs assurent l’apport d’énergie thermique au cowper et fonctionnent dans des conditions très exigeantes. Pour garantir leur longévité, leur efficacité énergétique et la sécurité de l’installation, les matériaux réfractaires utilisés doivent être soigneusement sélectionnés. Les produits à base de mullite sont couramment utilisés, car ils offrent une excellente résistance aux chocs thermiques tout en maintenant leur intégrité à haute température. Un choix judicieux de ces matériaux permet de minimiser les risques de dégradation, assurant ainsi la stabilité du processus thermique et la fiabilité du système.
Les conduits acheminent l’air chaud du cowper vers le haut fourneau. Exposés à des températures élevées, à de fortes fluctuations thermiques et à un environnement chimique agressif, ils nécessitent des matériaux très résistants. Dans les zones modérément sollicitées, le chamotte est privilégié pour son bon rapport coût-efficacité. En revanche, dans les zones soumises à des variations thermiques violentes, les matériaux à base de mullite sont utilisés pour garantir la stabilité et la fiabilité du système.
Comment pouvons-nous vous aider ?
Vous souhaitez recevoir un conseil gratuit ou poser une question sur le choix d’un revêtement réfractaire? Laissez-nous vos coordonnées – nous vous rappellerons!
Contactez-nousComment concevoir les blocs grillagés afin de limiter l’encrassement et l’enfournement de laitier dans le régénérateur ?
Quel matériau protège le brûleur contre l’écaillage et les chocs thermiques ?
Comment réaliser les joints de dilatation dans un revêtement en céramique pour qu’ils absorbent les variations dimensionnelles dues aux cycles thermiques ?
La poche torpille
La poche torpille, utilisée pour le transport de l’acier liquide entre le convertisseur et les postes de coulée, est soumise à des conditions thermiques extrêmes, avec des températures dépassant fréquemment 1600 °C. Ces poches, de très grande capacité – allant de 200 à 460 tonnes – fonctionnent dans un cycle rapide de remplissage, transport et vidage. Cela entraîne de fortes variations de température et des sollicitations mécaniques dynamiques. Le revêtement réfractaire est conçu pour minimiser les pertes de chaleur, résister aux chocs thermiques, ainsi qu’aux attaques chimiques des composants agressifs contenus dans l’acier liquide. Une attention particulière est accordée à la zone soumise à l’érosion provoquée par le contact direct avec le métal en fusion et le laitier. PCO Żarów propose une gamme complète de matériaux réfractaires adaptés à la construction des poches torpilles, tant pour les couches de travail que de protection. Nous fournissons des bétons réfractaires hautes performances et des éléments préfabriqués spécifiquement destinés aux zones les plus sollicitées, comme la gorge d’écoulement ou la zone d’impact.
Portée: Conception du garnissage Fourniture des matériaux réfractaires Services de montage du garnissage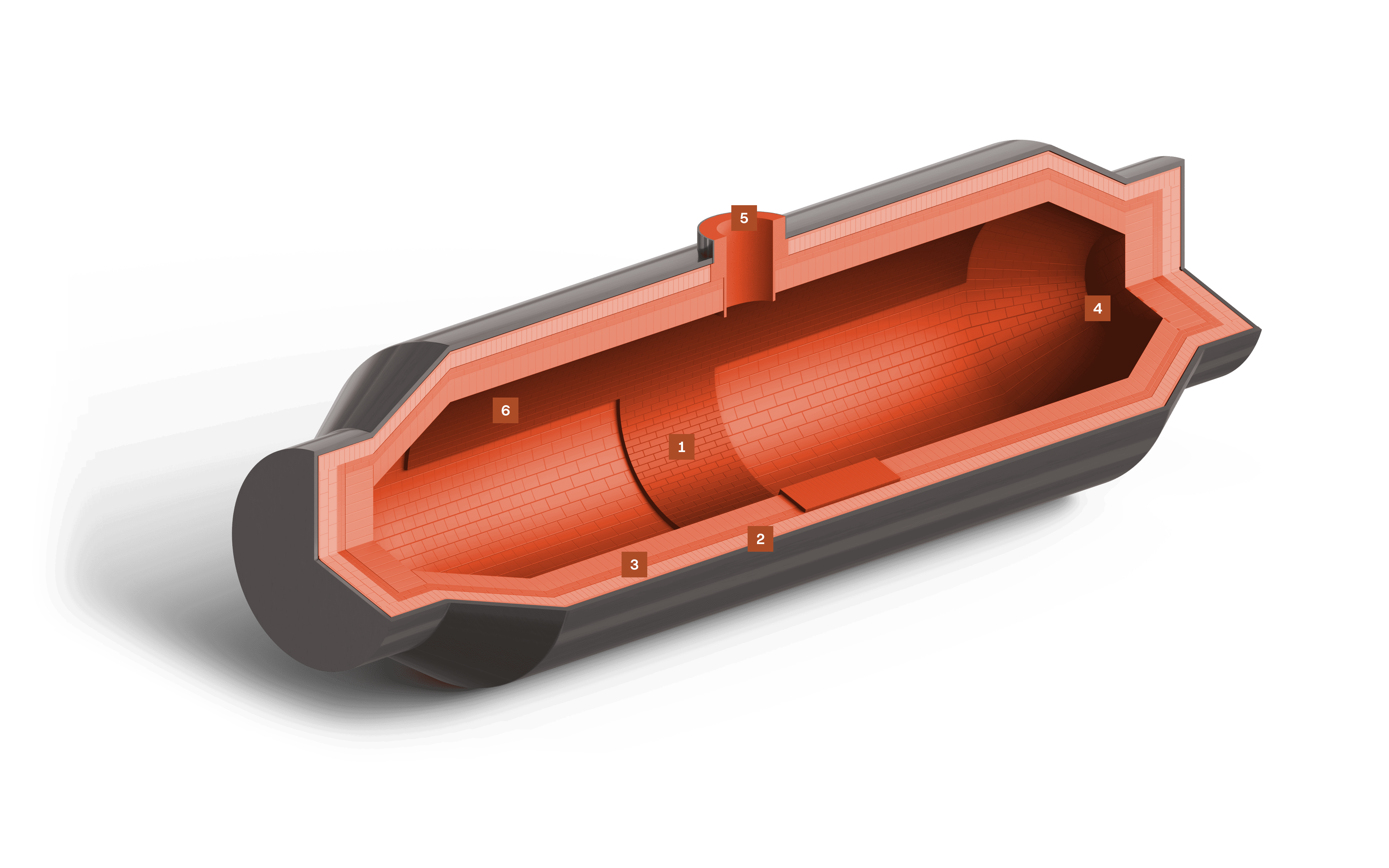
La zone d’impact est l’endroit où l’acier liquide pénètre violemment dans la poche, générant des chocs thermiques et mécaniques extrêmes. Les matériaux doivent présenter une résistance thermique exceptionnelle ainsi qu’une capacité à absorber les impulsions de chaleur sans subir de dommages structurels. La continuité du revêtement dans cette zone est primordiale pour garantir la stabilité à long terme de la structure et prévenir la dégradation prématurée de la poche.
La couche isolante protège la structure métallique contre les pertes thermiques et les déformations causées par le transport de grandes quantités de fonte. On utilise généralement un système multicouche combinant briques ou plaques isolantes réfractaires avec des matelas de fibres minérales. Ce système forme une barrière thermique et mécanique efficace, limitant les déformations tout en maintenant la performance énergétique. Les produits PERLITEX et ISOLUX proposés par PCO assurent une bonne isolation et une forte résistance à la compression.
La couche de protection joue un rôle tampon entre la couche de travail et la structure. Elle empêche les attaques directes de l’acier et du laitier en cas de défaillance de la couche de travail. Les matériaux utilisés doivent combiner isolation thermique, résistance à l’abrasion, résistance aux attaques chimiques, et bonne tenue à la compression. Les briques des gammes NORMATON, SUPERTON et ANDALUX sont souvent utilisées pour cette application.
Soumise au contact direct avec l’acier liquide, la couche de travail est confrontée à des conditions particulièrement agressives : chocs thermiques violents, corrosion chimique intense et érosion mécanique. De plus, les poches torpilles peuvent se déformer au fil du temps, d’où la nécessité d’utiliser des matériaux ayant une très grande précision dimensionnelle pour éviter les défauts comme le "martelage local". Dans certaines conceptions, une couche de transition est ajoutée entre la couche de travail et celle de protection, permettant une compatibilité thermique et mécanique optimale.
La gorge d’écoulement est la zone par laquelle l’acier est introduit ou évacué. Cette partie présente une géométrie complexe et subit des agressions thermiques et mécaniques très intenses. Elle exige des bétons réfractaires denses, capables de former une structure homogène et résistante. PCO Żarów propose des formulations spécifiques pour cette zone, notamment des bétons à séchage rapide ("fast dry") qui permettent une mise en service rapide à basse température.
Dans cette zone s’accumulent les résidus de laitier et de cendres. Bien que la température y soit plus basse que dans le reste de la poche, le frottement accru génère des charges mécaniques importantes susceptibles d’accélérer la dégradation. Les matériaux doivent donc offrir une excellente résistance à l’abrasion et au frottement afin d’assurer la longévité du revêtement.
Comment pouvons-nous vous aider ?
Vous souhaitez recevoir un conseil gratuit ou poser une question sur le choix d’un revêtement réfractaire? Laissez-nous vos coordonnées – nous vous rappellerons!
Contactez-nousQuelle solution permet de limiter la corrosion du revêtement dans la zone du laitier ?
Quel système multicouche protège efficacement contre les chocs thermiques pendant les cycles de remplissage ?
Quel matériau choisir pour réduire la dégradation de la maçonnerie dans la zone d’impact ?
La poche à fonte
La poche à fonte, utilisée dans les procédés de production de fonte, joue un rôle clé en servant de réservoir pour le transport et le stockage de la fonte brute à des températures comprises entre 1400 et 1500 °C. Ce processus peut être continu ou cyclique, et requiert un contrôle rigoureux des paramètres thermiques et mécaniques pour garantir la stabilité de la température et la qualité chimique de la fonte. Le revêtement réfractaire de la poche à fonte doit supporter des charges thermiques intenses, des chocs thermiques pendant les cycles de remplissage et de vidage, ainsi qu’un environnement agressif lié aux gaz chauds et aux résidus de laitier. Le choix de mélanges réfractaires hautement résistants à la corrosion et à l’abrasion est essentiel pour assurer une durée de vie prolongée de l’équipement. PCO Żarów fournit des revêtements complets pour les poches à fonte, comprenant à la fois les couches de protection et de travail. Les zones en contact direct avec le métal en fusion sont revêtues de briques réfractaires spécialisées, tandis que les bords de la poche sont protégés par des bétons réfractaires. Pour l’isolation thermique, des briques et des bétons isolants légers sont utilisés afin de limiter efficacement les pertes de chaleur.
Portée: Conception du garnissage Fourniture des matériaux réfractaires Services de montage du garnissage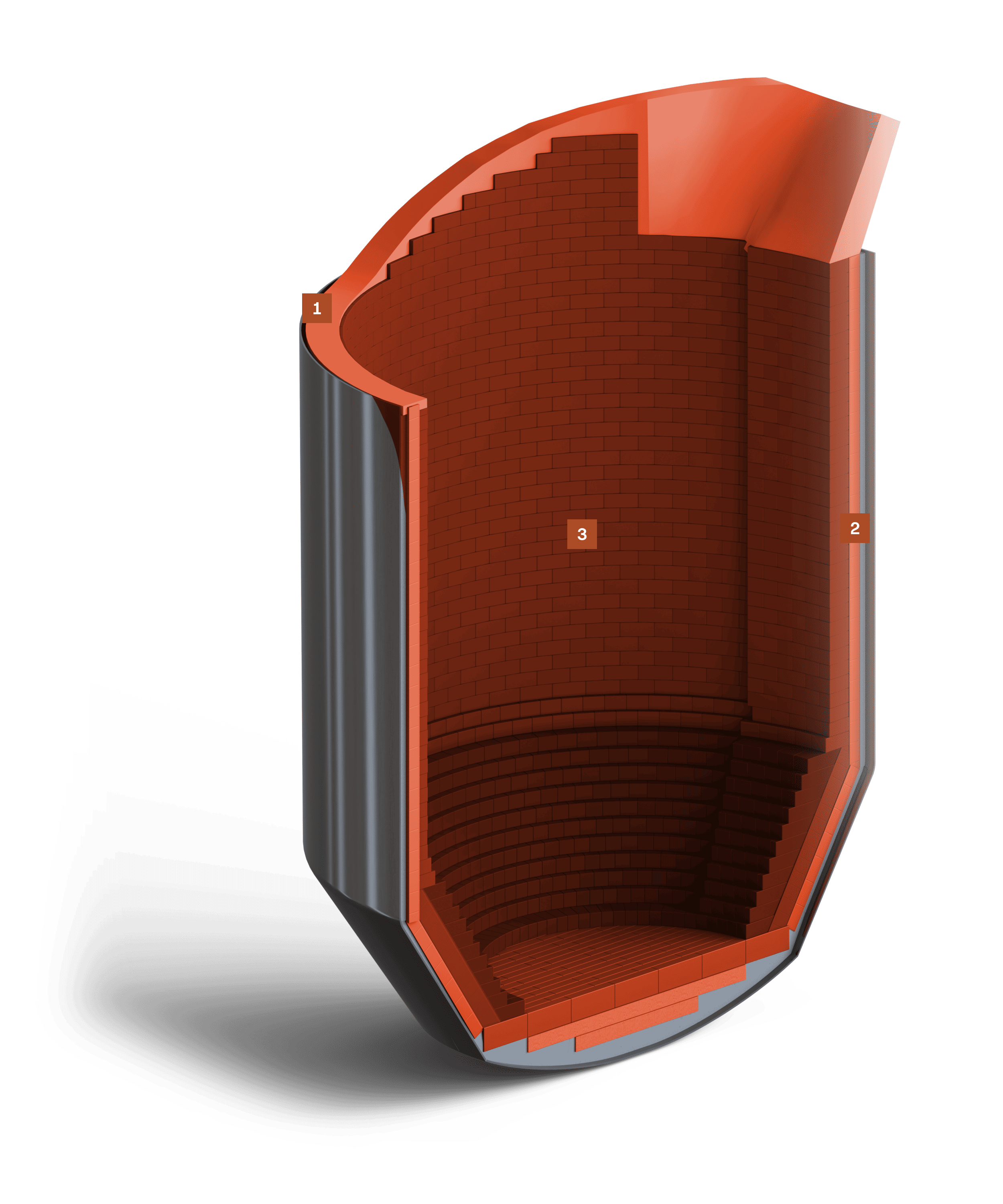
Cette zone exige des matériaux à la fois très résistants au feu et capables de résister à la corrosion et à l’érosion provoquées par le contact avec l’acier liquide et le laitier. L’intensité de fonctionnement et les chocs mécaniques dus au transport mettent la structure à rude épreuve. PCO Żarów recommande ici des bétons réfractaires à faible ou moyenne teneur en ciment, applicables par coulage ou par projection. Pour faciliter la construction, le même matériau est utilisé pour le bord supérieur et la buse de coulée.
Cette couche vise à réduire les pertes de chaleur, permettant de maintenir la fonte à température optimale plus longtemps. Elle est constituée de briques réfractaires denses et de bétons spécialisés, résistants aux températures extrêmes et aux conditions d’exploitation difficiles. Un choix approprié permet d’adapter parfaitement les paramètres aux exigences du procédé, tout en réduisant les pertes d’énergie et les coûts d’exploitation.
Soumise à de fortes contraintes, la couche de travail subit des déformations. C’est pourquoi les formes réfractaires utilisées doivent respecter des tolérances dimensionnelles très strictes. Il est également fondamental que leur coefficient de dilatation thermique soit bien adapté pour éviter le lessivage des joints sous l’effet des cycles thermiques. Les matériaux doivent résister aux températures élevées, aux chocs thermiques brusques, à l’action agressive de la fonte et du laitier. Un choix judicieux garantit non seulement la résistance à la corrosion et à l’érosion, mais aussi la stabilité structurelle du revêtement, ce qui est déterminant pour la qualité du processus et du produit final.
Comment pouvons-nous vous aider ?
Vous souhaitez recevoir un conseil gratuit ou poser une question sur le choix d’un revêtement réfractaire? Laissez-nous vos coordonnées – nous vous rappellerons!
Contactez-nousComment protéger une maçonnerie alumino-silicatée contre l’agression d’un laitier basique ?
Quel système multicouche permet de limiter les fissures thermo-mécaniques dans la couche de travail ?
Quel béton réfractaire offre la meilleure résistance à l’érosion par flux dans la zone du bord supérieur et de la buse ?
Le mélangeur de fonte
Le mélangeur de fonte est destiné au stockage tampon et à l’homogénéisation de la fonte issue du haut fourneau, tout en maintenant ses propriétés, principalement sa température, dans l’atelier d’acierie. Son revêtement réfractaire fonctionne à des températures très élevées, entre 1400 et 1500 °C, et doit résister aux variations thermiques, à la corrosion chimique ainsi qu’à l’érosion due à l’écoulement du métal liquide. Le choix des matériaux réfractaires dépend de chaque zone du mélangeur, car elles sont soumises à des contraintes différentes. Les produits PCO sont utilisés aussi bien dans la couche de travail de la zone supérieure que dans les couches isolantes situées sous le revêtement principal, assurant une protection optimale et une longue durée de vie de l’équipement. PCO Żarów fournit également les revêtements moulés pour le brûleur et la buse de vidange du mélangeur. Pour la partie cylindrique supérieure, non exposée directement au métal en fusion, nous proposons des briques à haute teneur en alumine à base d’andalousite.
Portée: Conception du garnissage Fourniture des matériaux réfractaires Services de montage du garnissage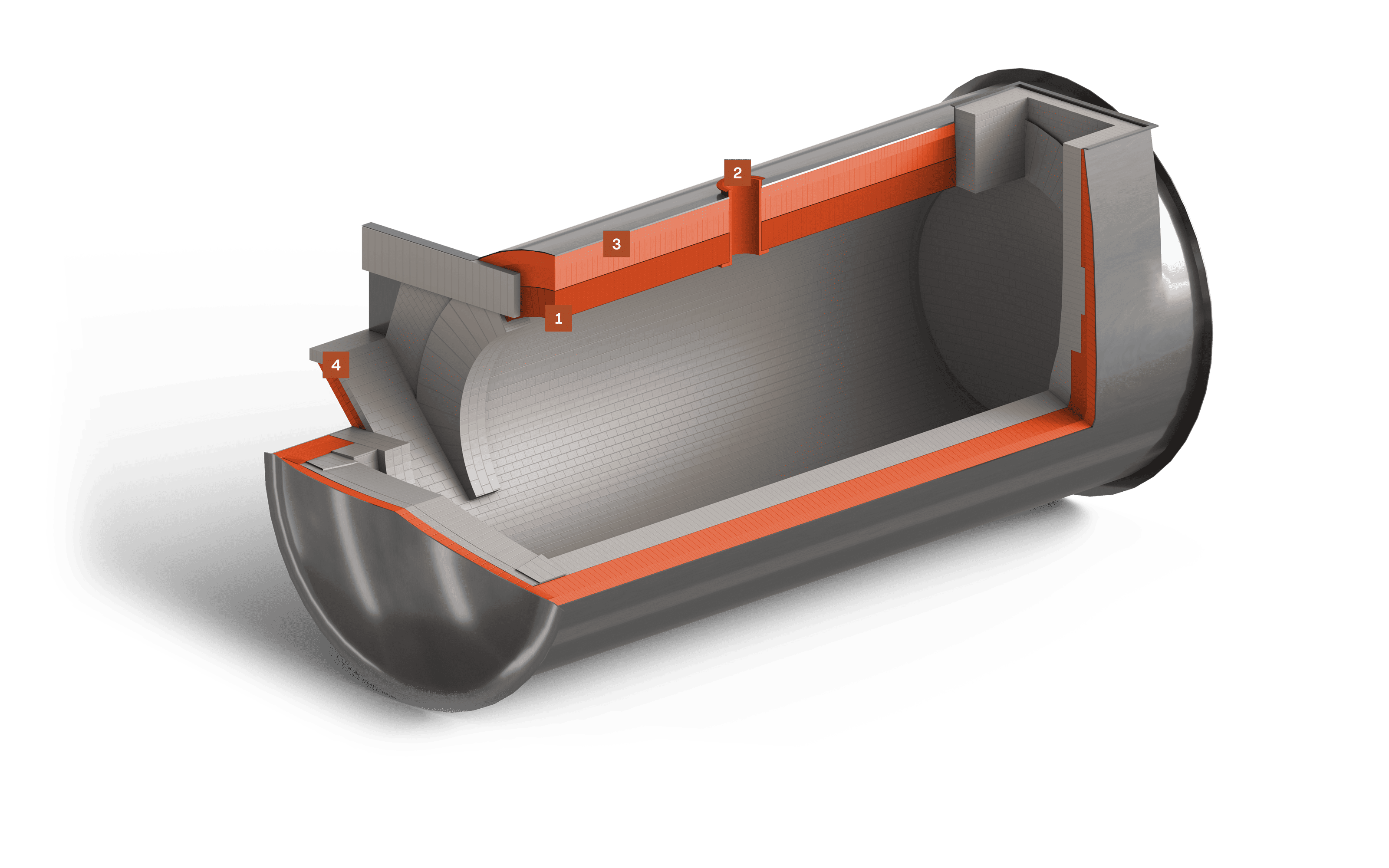
La zone métallique comprend les parties supérieures de la section cylindrique, les parois latérales et l’ouverture de remplissage. Cette zone est fortement exposée aux chocs thermiques et à l’érosion provoquée par le flux d’acier liquide. Les produits ANDALUX, alumino-silicatés à haute teneur en alumine, offrent une excellente résistance aux chocs thermiques et à l’érosion, garantissant la stabilité du revêtement dans des conditions d’usage intensives.
La zone du brûleur est soumise à une usure mécanique sévère et à des agressions chimiques intenses. Pour y répondre, PCO Żarów recommande l’utilisation du béton PCOCAST BN X222, un béton à faible teneur en ciment, qui conserve une résistance élevée à des températures allant jusqu’à 1600 °C.
La couche isolante vise à réduire les pertes de chaleur et à protéger la structure métallique du mélangeur contre la surchauffe. Elle combine des produits chamottés contenant 42–44 % d’Al₂O₃, comme SUPERTON, avec des briques isolantes légères de la série ISOLUX. Cette combinaison assure à la fois une excellente isolation thermique et une bonne résistance à la compression.
La buse de vidange, point final de l’équipement, est exposée à des températures très élevées, à des chocs thermiques rapides et à une forte usure mécanique et chimique, comme la zone du brûleur. Le béton PCOCAST BN X222 est recommandé pour cette application. Il conserve ses propriétés même à 1600 °C, garantissant durabilité et fiabilité.
Comment pouvons-nous vous aider ?
Vous souhaitez recevoir un conseil gratuit ou poser une question sur le choix d’un revêtement réfractaire? Laissez-nous vos coordonnées – nous vous rappellerons!
Contactez-nousQuel matériau utiliser pour les couches de protection afin de résister aux contraintes thermiques cycliques ?
Quels produits sont capables de supporter les déformations et le fluage dus aux charges mécaniques pendant la rotation du mélangeur ?
Comment combiner un revêtement alumino-silicaté avec une couche de travail basique dans la zone supérieure du métal ?
La voûte du four à arc électrique
La voûte du four à arc électrique constitue la partie interne en forme de dôme qui entoure directement la zone de l’arc, où les températures atteignent et dépassent les 1600 °C. Sa fonction principale est de protéger la structure du four, d’assurer une répartition homogène de la chaleur et de limiter les pertes thermiques pendant les cycles de fusion intensifs. La charge métallurgique placée dans le four est soumise à l’action directe de l’arc électrique, et le courant des électrodes traverse le matériau. Par conséquent, la vitesse d’usure du revêtement réfractaire est bien plus élevée que dans d’autres installations thermiques utilisées en sidérurgie.
Portée: Conception du garnissage Fourniture des matériaux réfractaires Services de montage du garnissage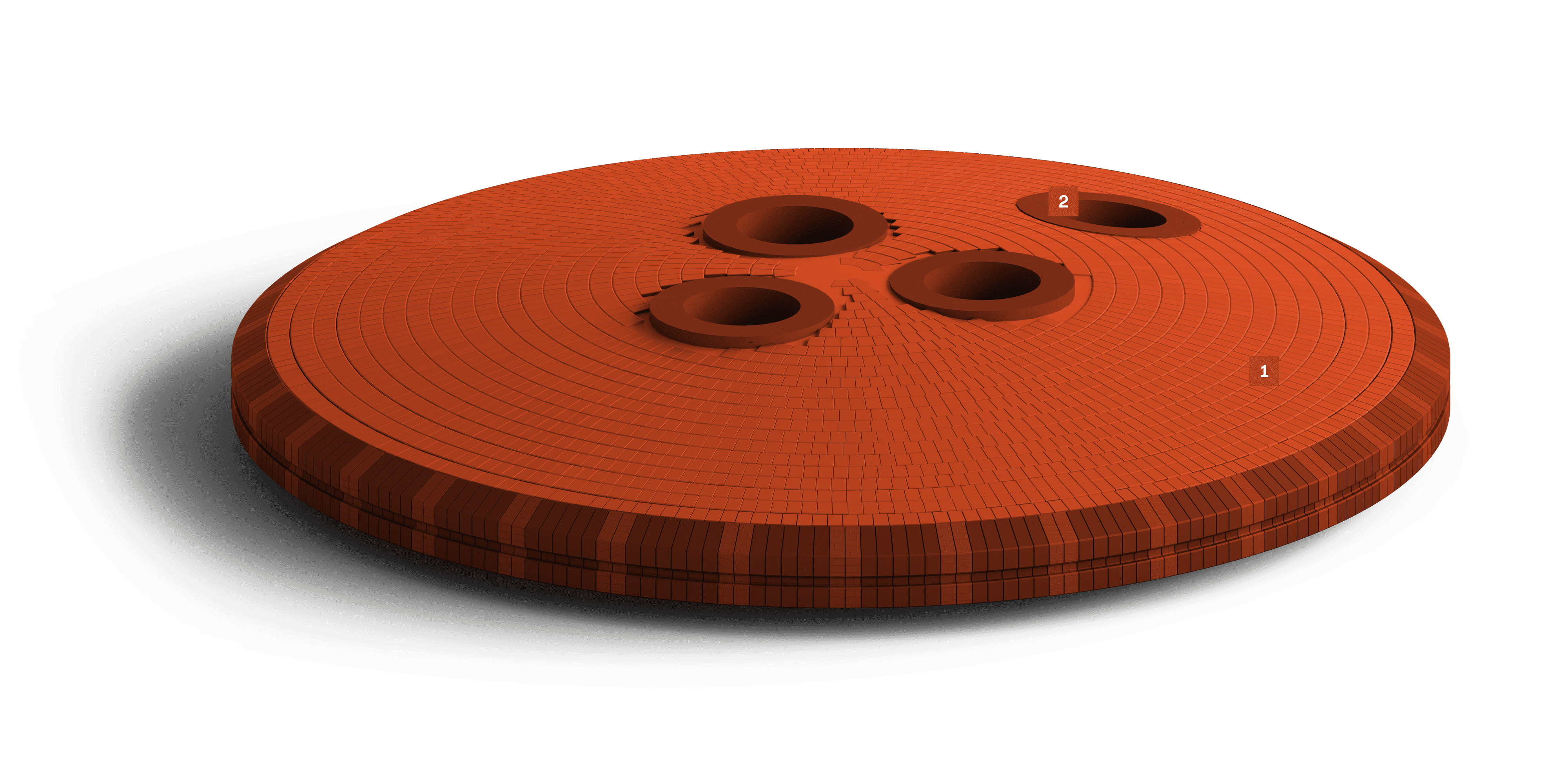
Pour prolonger la durée de vie de cet élément stratégique, PCO Żarów a développé des bétons réfractaires spéciaux de type PCOCAST, tels que 170KCR5 et BNX222. Grâce à une technologie avancée, ces bétons résistent aux variations fréquentes et rapides de température, assurant une excellente stabilité structurelle. De plus, leur temps de prise optimisé permet de réaliser le coulage et le séchage directement en aciérie, sur place, sans recourir à un four de préchauffage externe.
Les blocs d’entrée d’électrodes forment l’encadrement des ouvertures à travers lesquelles les électrodes en graphite sont introduites dans le four. Ils permettent le déplacement sécurisé des électrodes (montée et descente) durant le fonctionnement, tout en maintenant l’arc électrique en position optimale dans la chambre de fusion. Pour leur réalisation, PCO recommande des briques à haute teneur en alumine et des bétons à faible teneur en ciment, avec plus de 80 % d’Al₂O₃, afin de garantir la résistance aux fissurations provoquées par les vibrations et les mouvements répétés des électrodes.
Comment pouvons-nous vous aider ?
Vous souhaitez recevoir un conseil gratuit ou poser une question sur le choix d’un revêtement réfractaire? Laissez-nous vos coordonnées – nous vous rappellerons!
Contactez-nousComment concevoir la voûte pour qu’elle résiste aux hausses brutales de température et éviter l’écaillage du revêtement ?
Quel matériau choisir pour protéger contre la corrosion liée aux vapeurs condensables au niveau de la voûte ?
Comment dimensionner et maçonner les blocs d’entrée d’électrodes pour éviter les fissures dues aux vibrations et aux mouvements?
La poche de coulée principale
La poche de coulée principale, utilisée pour le transport de l’acier liquide lors de la fusion et des étapes de traitement ultérieur, fonctionne à des températures comprises entre 1550 et 1650 °C et subit des cycles thermiques intenses. Son rôle essentiel est de préserver la stabilité thermique du métal tout en minimisant les pertes de chaleur, un facteur clé pour maintenir les paramètres chimiques optimaux de l’acier. Le revêtement réfractaire doit résister à des variations de température brutales, à des contraintes mécaniques élevées et à la corrosion chimique provoquée par les composants métalliques fondus et les gaz de combustion. PCO Żarów fournit des produits réfractaires adaptés aux parois latérales et aux couches de protection, avec des matériaux magnésiens pour la couche de travail. Le fond de la poche, incluant la zone de travail et les formes de coulée, est réalisé à l’aide de produits alumino-silicatés non cuits, qui assurent une grande durabilité et une excellente stabilité dans des conditions extrêmes.
Portée: Conception du garnissage Fourniture des matériaux réfractaires Services de montage du garnissage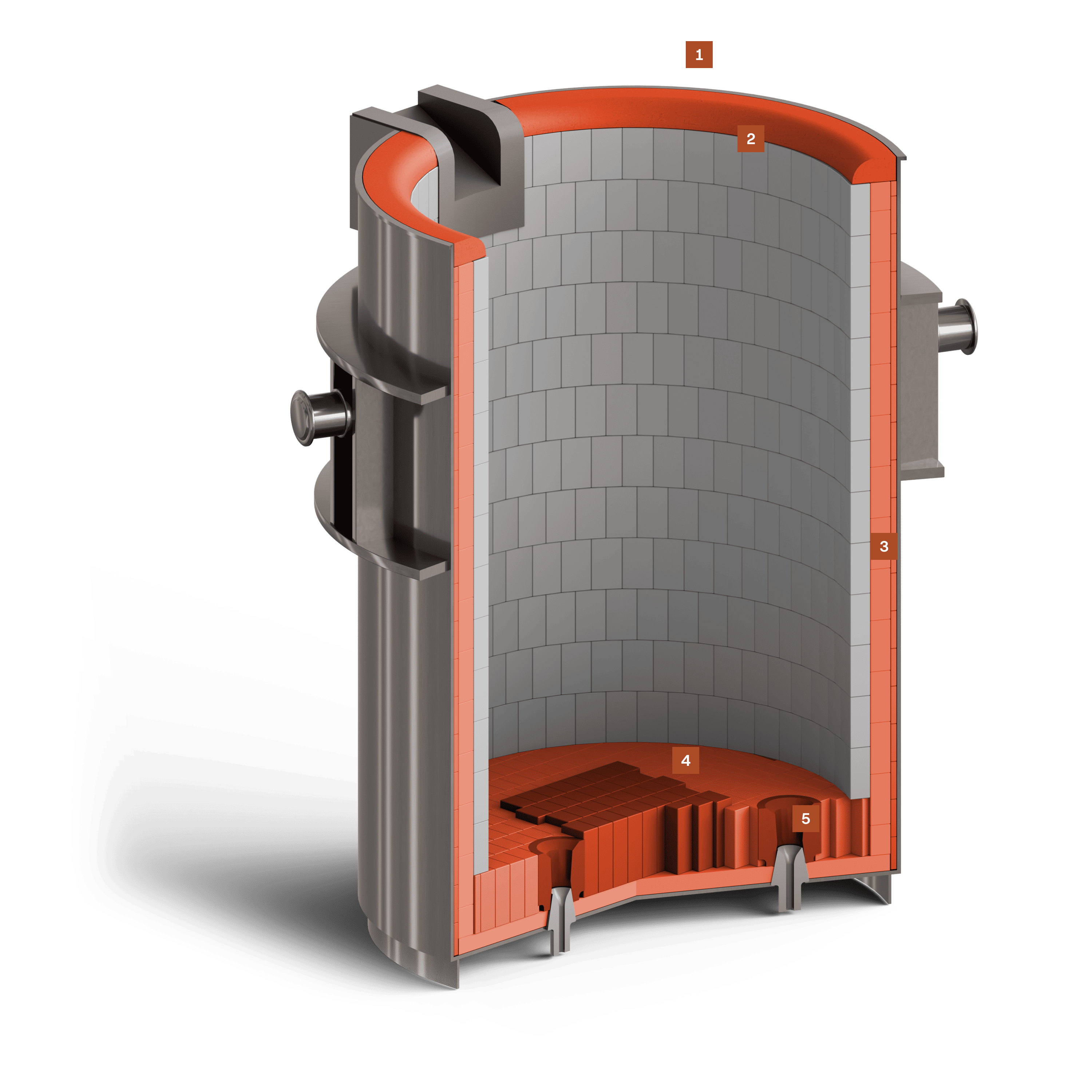
Le couvercle de la poche est destiné à maintenir une température élevée du métal pendant le transport. Il doit donc combiner une très bonne résistance aux températures extrêmes avec une performance isolante élevée. PCO Żarów a développé un béton spécial qui, tout en offrant une excellente tenue thermique, présente également une conductivité réduite. Ce matériau permet de conserver la température de l’acier tout en réduisant le poids du couvercle et la quantité de béton nécessaire, grâce à sa faible densité.
Le bord supérieur (ou couronne) est exposé à un contact direct avec l’acier liquide, le laitier et aux impacts mécaniques dus au transport. Les matériaux utilisés doivent donc offrir une résistance exceptionnelle aux hautes températures, à la corrosion chimique et aux charges dynamiques. PCO propose des bétons de différentes formulations – à faible, ultra-faible ou sans ciment – à base d’agrégats de haute qualité pour répondre à ces exigences.
Cette couche a pour objectif de réduire les pertes de chaleur afin de prolonger la conservation de la température de l’acier. Une isolation efficace de l’intérieur de la poche améliore l’efficacité de la coulée et permet des économies d’énergie. PCO Żarów propose des solutions sous forme de briques réfractaires denses ou de bétons, assurant à la fois de bonnes propriétés isolantes et une résistance aux contraintes mécaniques.
Le fond de la poche est une zone critique, directement exposée à l’acier fondu et au laitier. Il est essentiel de garantir une structure homogène et continue du revêtement. Pour cela, PCO Żarów a conçu un matériau chimiquement lié spécifiquement destiné à la zone d’impact (impact pad). Pour les parois latérales en contact avec le métal et le laitier, les produits des gammes ANDALUX et BAUXITEX sont recommandés. Ils offrent une excellente résistance aux agressions chimiques et mécaniques, contribuant à la stabilité à long terme du revêtement.
Les formes de coulée (ou buses de sortie) remplissent une fonction cruciale dans la poche : elles guident le flux d’acier liquide. Elles doivent donc être fabriquées à partir de matières premières extrêmement pures et stables sur les plans chimique et thermique. PCO Żarów a mis au point plusieurs qualités de bétons liés au spinelle, spécifiquement conçus pour ces applications. Ces matériaux se distinguent par une grande résistance à la corrosion et à l’érosion, garantissant la sécurité et la longévité du revêtement, même après une utilisation prolongée.
Comment pouvons-nous vous aider ?
Vous souhaitez recevoir un conseil gratuit ou poser une question sur le choix d’un revêtement réfractaire? Laissez-nous vos coordonnées – nous vous rappellerons!
Contactez-nousÉrosion du fond de la poche : comment concevoir un impact pad efficace et limiter l’usure des formes de coulée ?
Quels produits réfractaires protègent le mieux la couche de protection contre les fissures et l’écaillage liés aux chocs thermiques ?
Comment diagnostiquer la nécessité de réfection du revêtement à partir de l’usure observée dans la zone du laitier ?
La poche intermédiaire (tundish)
La poche intermédiaire occupe une place essentielle dans le processus de coulée continue de l’acier. Elle assure le rôle de tampon et de répartition du métal liquide, garantissant la continuité du processus lors du changement de poche principale. Sa conception interne favorise également l’homogénéisation de la température et de la composition chimique de l’acier. Le revêtement réfractaire de la tundish est soumis à de fortes contraintes : exposition à des températures élevées, variations thermiques locales, érosion provoquée par l’écoulement de l’acier liquide. Il doit donc présenter une excellente résistance aux chocs thermiques, à la corrosion chimique et à l’érosion mécanique. Une maîtrise précise des paramètres du procédé et un choix rigoureux des matériaux réfractaires sont indispensables pour assurer la stabilité du fonctionnement. PCO Żarów fournit l’ensemble des éléments de la couche de travail : revêtement du couvercle, cloisons préfabriquées, plaques de fond sous la coulée ainsi que les formes de guidage dans les zones de vidage.
Portée: Conception du garnissage Fourniture des matériaux réfractaires Services de montage du garnissage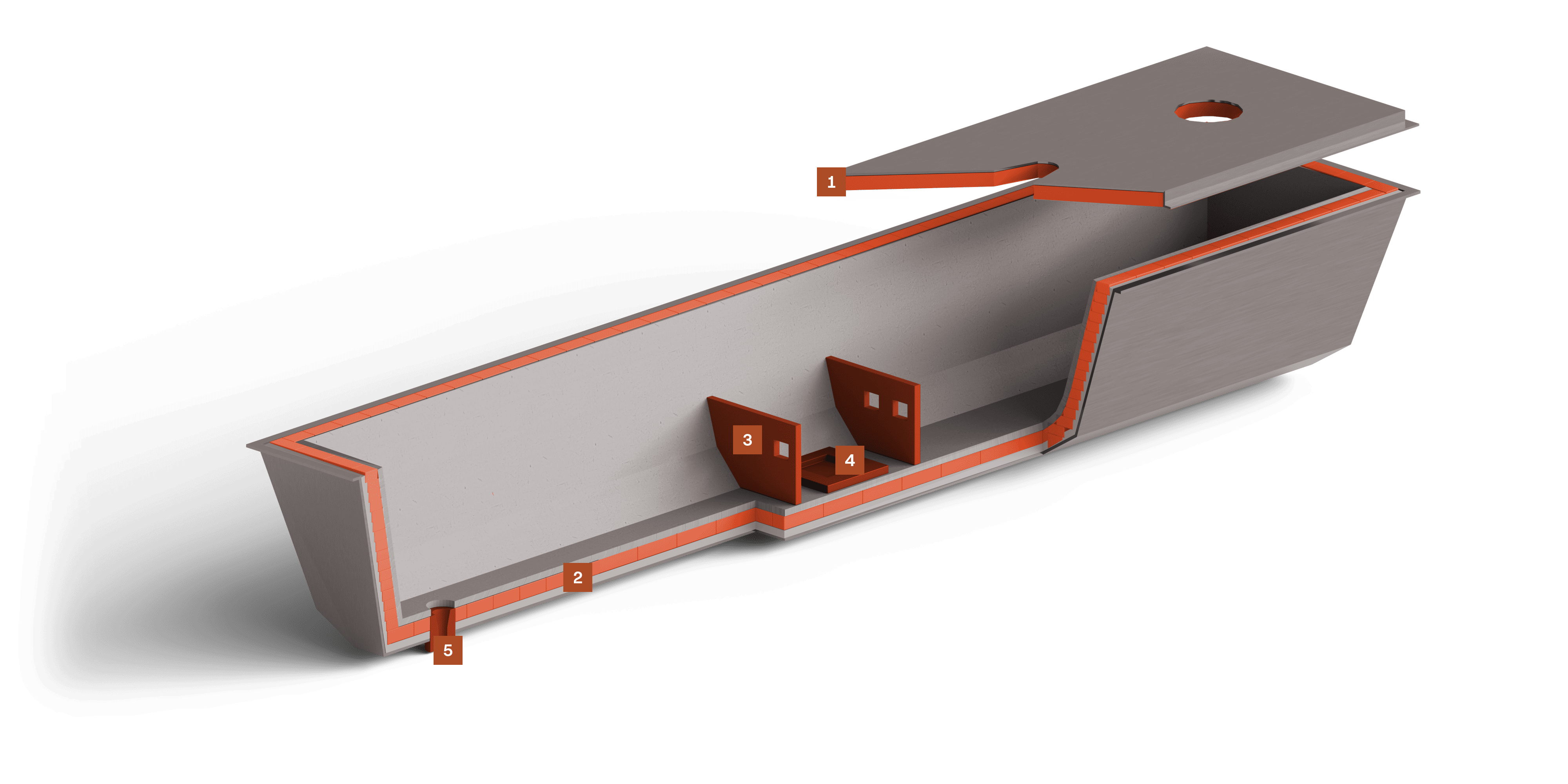
Le couvercle a pour fonction principale de limiter les pertes de chaleur afin de maintenir la température de l’acier liquide. Pour répondre à cette exigence, PCO Żarów propose des bétons à haute teneur en alumine combinant une excellente résistance thermique et une performance isolante accrue. Leur faible densité permet de réduire la masse du revêtement, améliorant ainsi l’efficacité thermique et réduisant les coûts d’exploitation.
La couche de protection vise avant tout à réduire les pertes thermiques. Les solutions proposées par PCO incluent des briques isolantes de type ISOLUX, reconnues pour leur très bonne capacité d’isolation thermique, ainsi que des briques denses comme ANDALUX ou BAUXITEX, qui assurent une résistance mécanique élevée et une protection contre l’agression de l’acier fondu ou du laitier en cas de pénétration à travers la couche de travail. Les bétons PCOCAST et MULCAST, grâce à leur grande fluidité, garantissent un remplissage homogène sans interstices, renforçant l’efficacité thermique.
Les cloisons à l’intérieur de la tundish servent à supprimer les turbulences pendant le remplissage, réduisant ainsi les inclusions et favorisant l’homogénéisation du métal. Ces éléments sont exposés à une corrosion et à une érosion sévères de la part de l’acier liquide et du laitier. Les matériaux PCO sont conçus pour résister durablement à ces agressions, assurant l’intégrité des cloisons pendant tout le cycle de coulée.
Les plaques de fond protègent la tundish contre les percements causés par le jet d’acier. Soumises à une exposition directe au métal liquide, elles doivent être fabriquées avec une précision extrême, garantissant une structure homogène et une haute résistance aux chocs thermiques et mécaniques. PCO Żarów propose des plaques produites par pressage à sec ou par coulage en béton réfractaire. Ces solutions éprouvées assurent une protection continue du revêtement et prolongent la durée de vie de la poche.
Les formes de coulée, en contact direct avec l’acier liquide, doivent offrir une excellente résistance thermique, une faible rétractation et une précision dimensionnelle parfaite pour garantir l’étanchéité au niveau de la buse. PCO Żarów propose une large gamme de produits pressés, y compris ceux des gammes ANDALUX et BAUXITEX, ainsi que des éléments préfabriqués comme PCOCAST et MULCAST, assurant une performance fiable dans les conditions les plus exigeantes.
Comment pouvons-nous vous aider ?
Vous souhaitez recevoir un conseil gratuit ou poser une question sur le choix d’un revêtement réfractaire? Laissez-nous vos coordonnées – nous vous rappellerons!
Contactez-nousQuel revêtement de travail résiste le mieux au choc thermique lors de la première coulée ?
Comment concevoir les cloisons pour qu’elles résistent à l’usure, à la corrosion et à l’érosion ?
Quel matériau choisir pour éviter la contamination de l’acier par des particules issues du revêtement céramique ?
Le système de coulée par siphon
Le système de coulée par siphon, élément clé de la ligne de coulée en lingotière, se compose de plusieurs pièces céramiques destinées à assurer une distribution précise du métal fondu vers les moules. Ces composants fonctionnent à des températures très élevées, souvent supérieures à 1600 °C, et sont soumis à des variations rapides de débit et de pression. Les matériaux réfractaires utilisés doivent résister à des charges thermiques intenses, à des cycles rapides de chauffage et de refroidissement, ainsi qu’à une corrosion chimique sévère liée à l’environnement agressif du métal liquide. La qualité de la surface de contact entre l’acier fondu et les éléments céramiques est cruciale : elle ne doit pas relâcher d’inclusions ni interagir chimiquement avec le métal, tout en permettant un détachement propre après la coulée. L’adaptation précise des matériaux aux conditions spécifiques du processus – notamment au type d’acier coulé – est essentielle pour garantir la stabilité des paramètres technologiques et assurer une qualité élevée des lingots.
Portée: Conception du garnissage Fourniture des matériaux réfractaires Services de montage du garnissage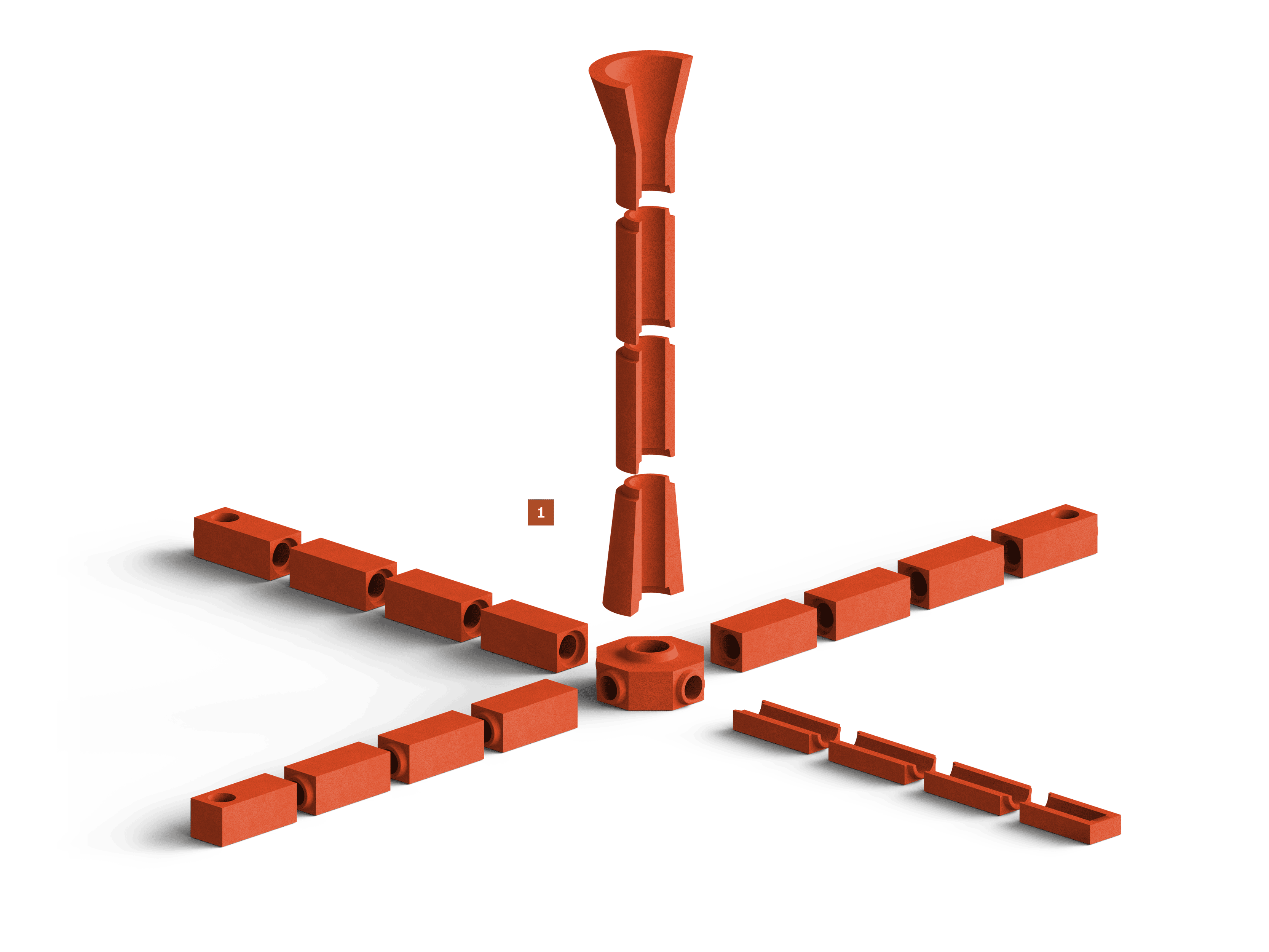
PCO Żarów fournit des ensembles complets de coulée par siphon, disponibles avec différents débits. Grâce à notre technologie de fabrication par pressage semi-sec, nous sommes en mesure de produire des parois aussi fines que 20 mm. Les pièces sont réalisées par pressage à sec, ce qui garantit une exécution très précise des détails (orifices d’entrée et de sortie, canaux, tubes, plaques de répartition) et une parfaite compatibilité entre tous les éléments du système.
Comment pouvons-nous vous aider ?
Vous souhaitez recevoir un conseil gratuit ou poser une question sur le choix d’un revêtement réfractaire? Laissez-nous vos coordonnées – nous vous rappellerons!
Contactez-nousQuel matériau offre la meilleure résistance au choc thermique lors de la coulée ?
Comment concevoir les dimensions des éléments pour limiter l’érosion et l’abrasion des canaux et des tuyaux ?
Quel matériau réduit les interactions avec l’acier et empêche l’apparition d’inclusions indésirables dans le métal ?
Le four à sole mobile (pusher furnace)
Le four à sole mobile est utilisé pour chauffer l’acier avant les opérations de mise en forme à chaud, telles que le laminage ou le forgeage. Il comporte plusieurs zones distinctes : préchauffage, chauffage principal et égalisation thermique. Pour garantir un fonctionnement efficace et durable, le revêtement réfractaire doit résister à l’érosion, à l’abrasion ainsi qu’aux chocs thermiques. Dans la zone de travail, exposée au contact direct avec le métal chauffé, on utilise des bétons ou des éléments préfabriqués offrant une forte résistance mécanique et une bonne tenue aux chocs thermiques. Dans les zones moins exposées, des bétons réfractaires, des masses à damer ou des éléments formés sont utilisés pour assurer une isolation thermique efficace tout en conservant une résistance mécanique adéquate. L’emploi de systèmes de revêtement multicouches, associant des couches de travail et des couches isolantes, permet d’atteindre des performances thermiques optimales. Cela améliore l’efficacité du chauffage et prolonge la durée de vie du four.
Portée: Conception du garnissage Fourniture des matériaux réfractaires Services de montage du garnissage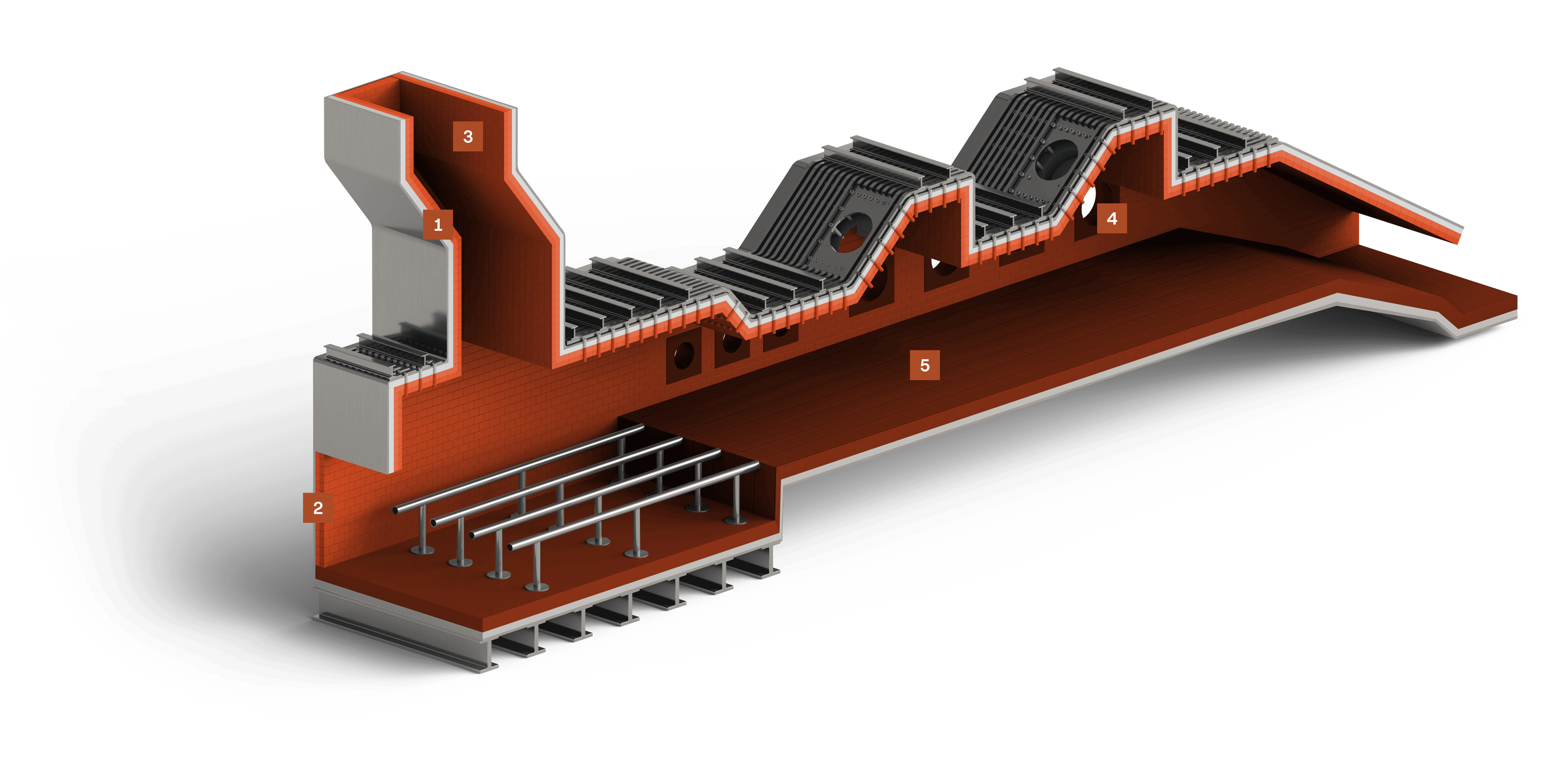
La couche de protection des parois est constituée de matériaux isolants ISOLUX, de chamottes SUPERTON et de produits à haute teneur en alumine ANDALUX. Leur combinaison assure une excellente isolation thermique, une stabilité des conditions de fonctionnement et une réduction des pertes de chaleur, ce qui se traduit par une meilleure efficacité du chauffage et une baisse des coûts d’exploitation.
Soumise à une forte usure, à l’oxydation et aux chocs thermiques, notamment dans les zones à forts gradients de température, la couche de travail des parois est réalisée à partir de briques andalousites ANDALUX. Pour les grandes surfaces, les éléments préfabriqués en béton MULCAST sont idéaux. Leur structure homogène leur confère une excellente résistance aux sollicitations thermiques et chimiques.
La voûte du four est directement exposée aux gaz de combustion chauds et aux variations thermiques importantes des cycles de chauffe. Dans cette zone, on utilise des briques alumino-silicatées contenant entre 60 et 80 % d’Al₂O₃. Pour les zones difficiles d’accès ou les épaisseurs importantes, des bétons réfractaires sont également employés avec succès.
Les brûleurs du four à sole mobile subissent des charges thermiques et chimiques extrêmes. Ils doivent être protégés par des matériaux capables de résister aux oxydes métalliques et aux laitiers agressifs. PCO Żarów fournit des blocs brûleurs fabriqués à partir de bétons à haute teneur en alumine. Leur stabilité thermique et leur robustesse assurent une performance fiable et durable des brûleurs.
La sole du four est la zone la plus sollicitée technologiquement. En contact direct avec le métal chaud, exposée aux gaz agressifs et à des températures extrêmes, elle requiert des matériaux présentant une très haute résistance thermique et chimique. Les bétons à haute teneur en alumine développés par PCO offrent de bonnes propriétés mécaniques sous des conditions d’utilisation intensives, garantissant la stabilité et la longévité de la structure.
Comment pouvons-nous vous aider ?
Vous souhaitez recevoir un conseil gratuit ou poser une question sur le choix d’un revêtement réfractaire? Laissez-nous vos coordonnées – nous vous rappellerons!
Contactez-nousQuel matériau protégera le mieux la sole (trzon) contre l’abrasion et la formation de calamine ?
Quel système multicouche permettra de limiter l’écaillage des briques intérieures (warstwa wewnętrzna)?
Comment concevoir le revêtement pour qu’il résiste aux impacts et pressions mécaniques pendant le déplacement du métal ?
Le four à pas marcheurs
Le four à pas marcheurs est conçu pour chauffer principalement des demi-produits sidérurgiques de grande taille et de forme régulière avant leur mise en forme plastique sur le laminoir. Le matériau est transporté à travers le four à l’aide d’un ensemble de poutres mobiles appelées walking beams (belki chodzące), ce qui permet un chauffage uniforme et contrôlé. Les températures de fonctionnement peuvent atteindre 1250 °C en continu. L’acier traverse trois zones principales : préchauffage, transfert et maintien thermique. Le revêtement réfractaire doit assurer une excellente étanchéité au gaz (szczelność gazowa), une résistance élevée aux chocs thermiques (szoki termiczne) et une bonne isolation (izolacyjność cieplna), afin de minimiser les pertes de chaleur et de garantir un chauffage homogène du métal avant le laminage ou le forgeage.
Portée: Conception du garnissage Fourniture des matériaux réfractaires Services de montage du garnissage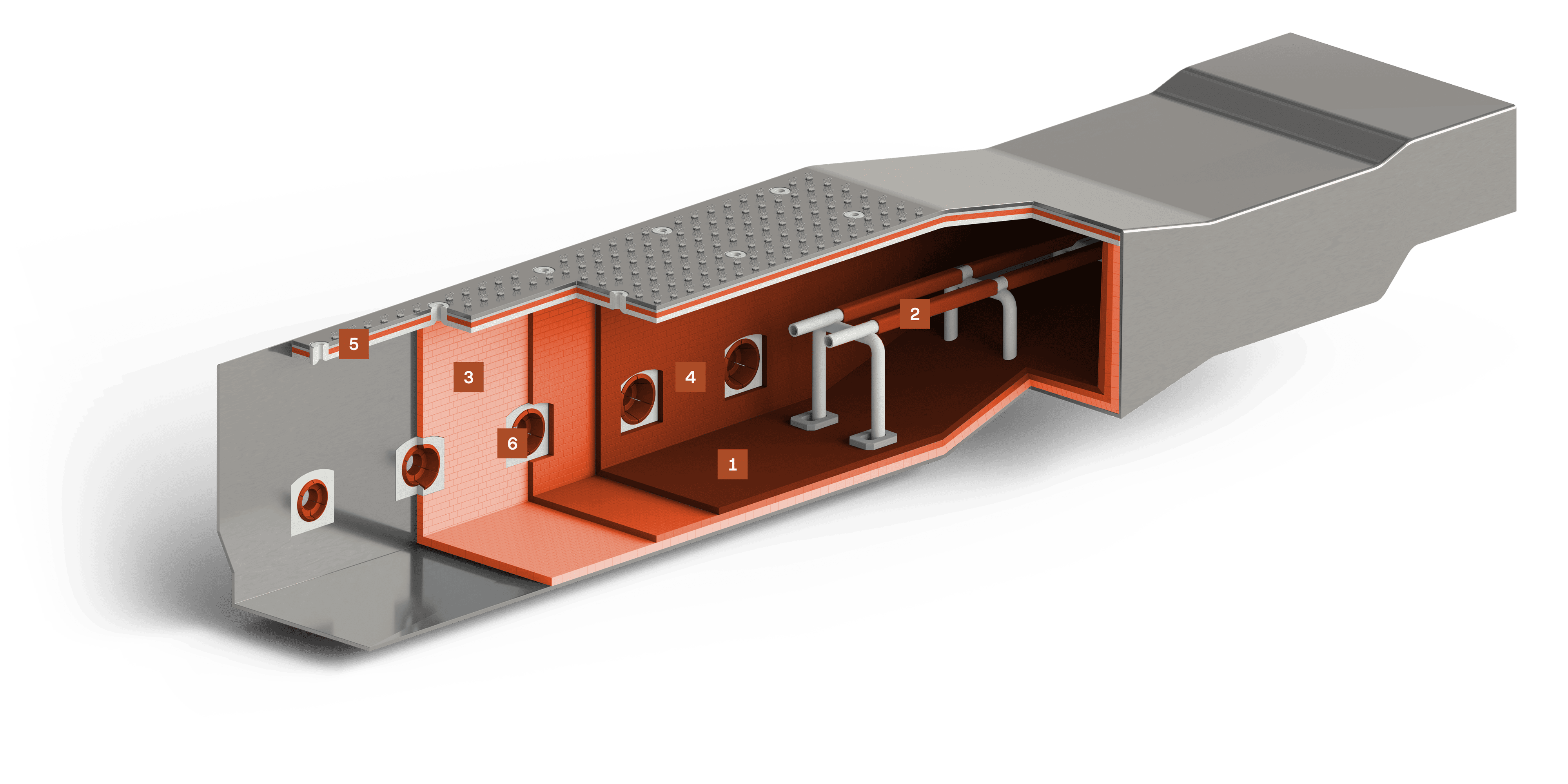
La sole du four est fortement sollicitée en raison du contact direct avec le métal chauffé, des gaz agressifs et des températures extrêmes. PCO Żarów recommande l’utilisation de bétons à haute teneur en alumine (beton wysokoglinowy) à écoulement amélioré, adaptés au revêtement de grandes surfaces. Pour les interventions d’urgence et une remise en service rapide, des bétons de type fast dry (betony szybkowiążące) sont proposés : ils peuvent être séchés en un temps très court, ce qui réduit considérablement les arrêts de production.
Les conduits de ce type de four jouent un rôle crucial dans le transfert de chaleur et l’acheminement des gaz de combustion (spaliny). PCO Żarów fournit des éléments préfabriqués prêts à être montés – aussi bien pour les conduits verticaux que horizontaux. Ces composants facilitent la maintenance et la modernisation. Dans les zones complexes comme les raccords en T (trójniki), des masses à damer PCO WetRAM (masy do ubijania) assurent l’étanchéité et la stabilité structurelle.
Les couches de protection des parois assurent une isolation thermique efficace et protègent la structure du four. Le bon choix de matériaux alumino-silicatés (materiały glinokrzemianowe) permet de maintenir des conditions de fonctionnement stables, de réduire les pertes de chaleur et d’optimiser le chauffage du métal.
Cette couche est soumise à une forte abrasion, à l’oxydation et à des chocs thermiques, surtout dans les zones où les différences de température sont marquées. Les briques andalousites à haute teneur en alumine ANDALUX (cegły andaluzytowe) assurent une excellente stabilité du revêtement. Pour les grandes surfaces, l’utilisation d’éléments préfabriqués en béton est idéale : leur structure homogène et leur facilité de pose garantissent un revêtement cohérent.
La voûte du four est exposée aux gaz chauds et à de grandes variations de température durant les cycles de fonctionnement. Elle peut être réalisée en briques alumino-silicatées (60–80 % d’Al₂O₃) ou en bétons bauxitiques ou corindoniques (betony boksytowe i korundowe). Ces bétons sont particulièrement adaptés aux surfaces difficiles d’accès ou aux couches épaisses.
Les brûleurs du four à pas marcheurs subissent des conditions thermiques et chimiques extrêmes. PCO Żarów recommande des bétons à base de corindon à haute teneur en alumine (beton korundowy), utilisables par coulage ou sous forme de pièces préfabriquées (kształtki palnikowe). Leur structure dense et leur résistance aux chocs thermiques garantissent la stabilité et l’efficacité à long terme des brûleurs.
Comment pouvons-nous vous aider ?
Vous souhaitez recevoir un conseil gratuit ou poser une question sur le choix d’un revêtement réfractaire? Laissez-nous vos coordonnées – nous vous rappellerons!
Contactez-nousQuel matériau céramique protégera le mieux les poutres mobiles (belki chodzące) contre la calamine tombant des demi-produits chauffés ?
Quelle configuration multicouche du revêtement garantira une résistance aux contraintes thermiques liées à l’introduction de métal froid ?
Quel matériau choisir pour limiter l’effritement du revêtement aux bords des poutres et autour des ancrages (kotwy)?
Le four à sole extractible
Les fours à sole extractible, principalement utilisés dans les ateliers de forge et de traitement thermique, servent à la chauffe, au détensionnement et au recuit des pièces moulées, demi-produits ou produits finis. Selon le type de charge et l’objectif du traitement, les températures varient entre 600 et 1350 °C. Le revêtement réfractaire est entièrement constitué de matériaux alumino-silicatés (materiały glinokrzemianowe) et de modules en fibres céramiques (moduły z włóknin ceramicznych), assurant stabilité thermique et résistance aux conditions extrêmes d’exploitation. PCO Żarów propose des solutions complètes pour les parois et la voûte du four, ainsi que plusieurs variantes de revêtement de la sole extractible – allant des modules préfabriqués, en passant par le coulage sur site, jusqu’à la maçonnerie traditionnelle.
Portée: Conception du garnissage Fourniture des matériaux réfractaires Services de montage du garnissage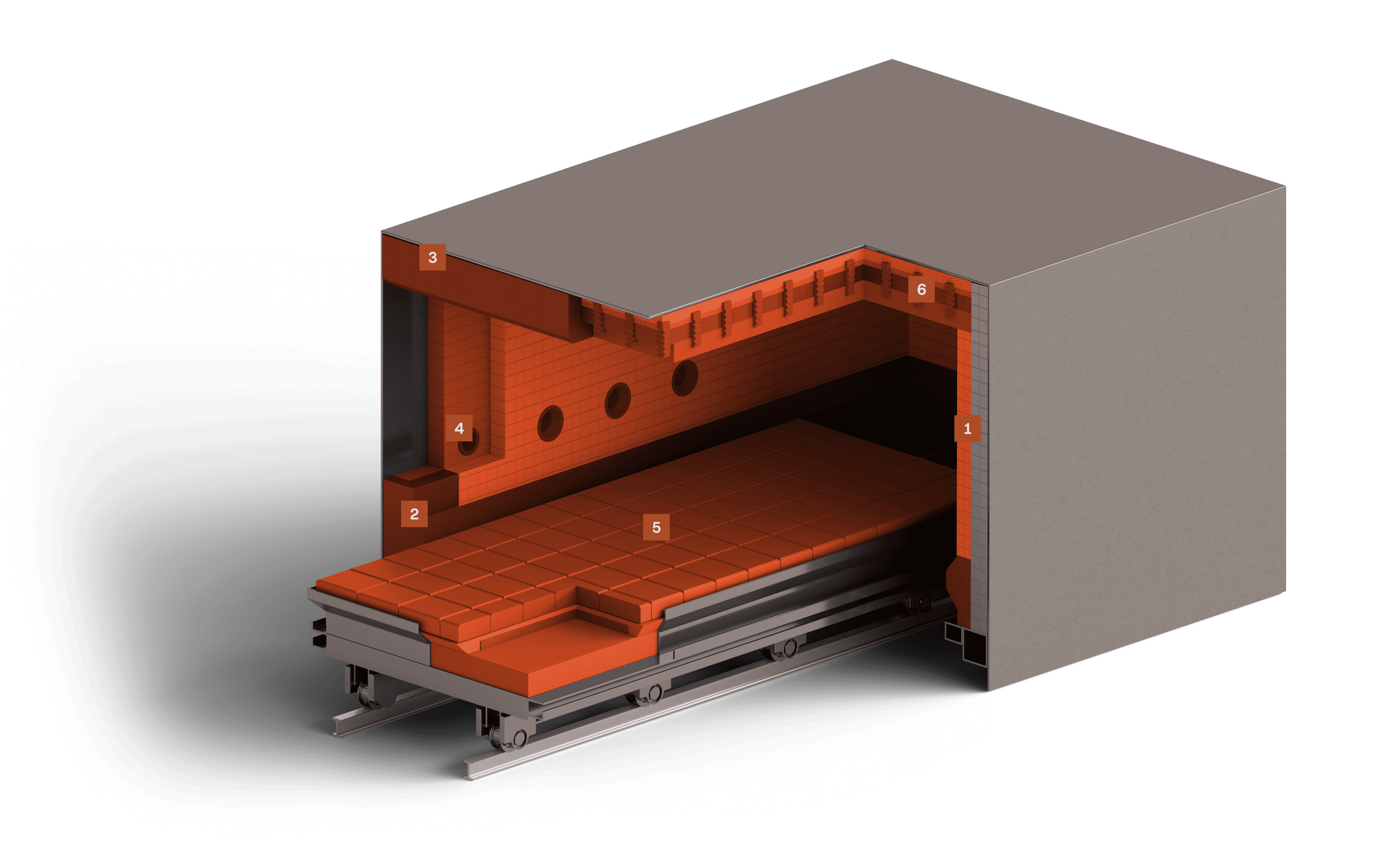
Les parois sont principalement soumises à des chocs thermiques (szoki termiczne) provoqués par les variations de température lors de l’ouverture du four à chaque retrait de la sole. Le revêtement est conçu selon un système multicouche (system wielowarstwowy), dont la couche de travail utilise des briques isolantes (cegły izolacyjne). Compte tenu des températures modérées (450–1250 °C), leur fonction est avant tout isolante, les contraintes mécaniques étant limitées.
Le socle est la base portante des parois, situé à hauteur de la sole. En plus des chocs thermiques, il subit des contraintes mécaniques liées au déplacement de la sole extractible (ruch trzonu). On y utilise généralement des bétons denses ou des briques réfractaires massives (cegły zwarte). Le système est également multicouche, incluant des modules en fibres isolantes (moduły izolacyjne) derrière la couche de travail, renforçant ainsi l’isolation et la stabilité du four.
La porte utilise des matériaux analogues à ceux du socle. Elle est généralement construite avec un béton réfractaire dense (ciężki beton ogniotrwały), en une seule couche, sans isolation supplémentaire.
Les brûleurs représentent les éléments les plus exposés aux chocs thermiques du four, avec des températures atteignant fréquemment 1300 °C. Pour répondre à ces exigences, on utilise des pièces préfabriquées en béton réfractaire dense à haute teneur en alumine (kształtki prefabrykowane z betonu wysokoglinowego), assurant la stabilité et la longévité de l’installation.
Le trzon est l’élément le plus sollicité thermiquement – il est régulièrement refroidi à chaque cycle d’entrée et de sortie du four. Dans certaines installations, la sole effectue plusieurs cycles par heure, générant d’importantes contraintes thermiques. Compte tenu des grandes dimensions des pièces chauffées, les matériaux doivent présenter une haute résistance mécanique (wytrzymałość mechaniczna) et aux chocs. Le revêtement est constitué de plusieurs couches, la couche de travail étant réalisée en béton dense ou en briques massives. Une attention particulière est portée aux joints de dilatation (dylatacje), vulnérables à l’encrassement par la calamine (zendra).
Le strop est exposé à des chocs thermiques ainsi qu’à un fonctionnement prolongé à haute température. Selon la conception, il peut être revêtu de modules en fibres céramiques (moduły z mat ceramicznych), adaptés aux conditions modérées, ou d’éléments préfabriqués lourds (kształtki prefabrykowane). Ces éléments sont constitués d’un béton dense combiné à un béton isolant, et sont fixés par des ancrages céramiques (kotwy ceramiczne), assurant leur stabilité.
Comment pouvons-nous vous aider ?
Vous souhaitez recevoir un conseil gratuit ou poser une question sur le choix d’un revêtement réfractaire? Laissez-nous vos coordonnées – nous vous rappellerons!
Contactez-nousQuel matériau choisir pour la porte (brama) et le socle (podbitka), afin qu’il résiste aux contraintes mécaniques liées aux mouvements de la sole ?
Comment concevoir la structure multicouche du trzon et les joints de dilatation pour garantir leur intégrité dans le temps ?
Quel matériau appliquer sur les parois (ściany) et le strop pour allier résistance mécanique et résistance aux chocs thermiques lors d’un fonctionnement cyclique ?
Pourquoi PCO
Installation avec fourniture de céramique – gestion de projet simplifiée et un seul garant de qualité
Précision dimensionnelle constante, quelle que soit la taille de série
Support des concepteurs et spécialistes matériaux – nous vous aidons à bien choisir le matériau et assurons la supervision du montage
Produits et services sélectionnés
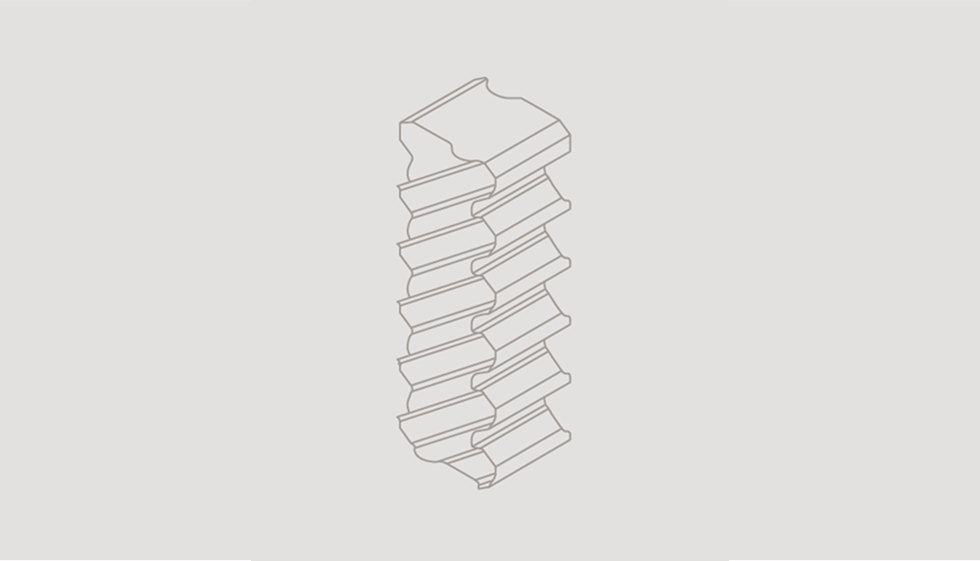
Ancres céramiques
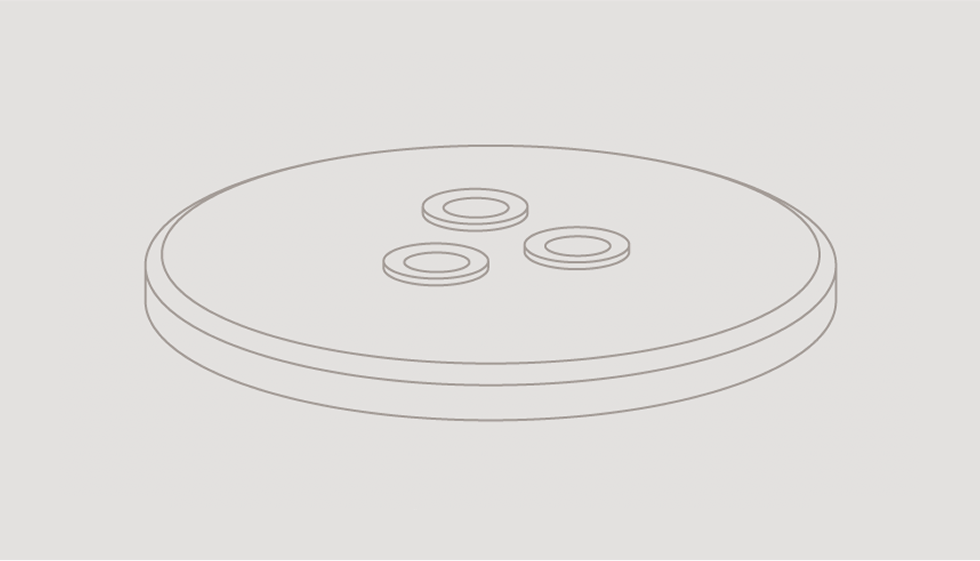
Voûte préfabriquée pour four à arc électrique (EAF)
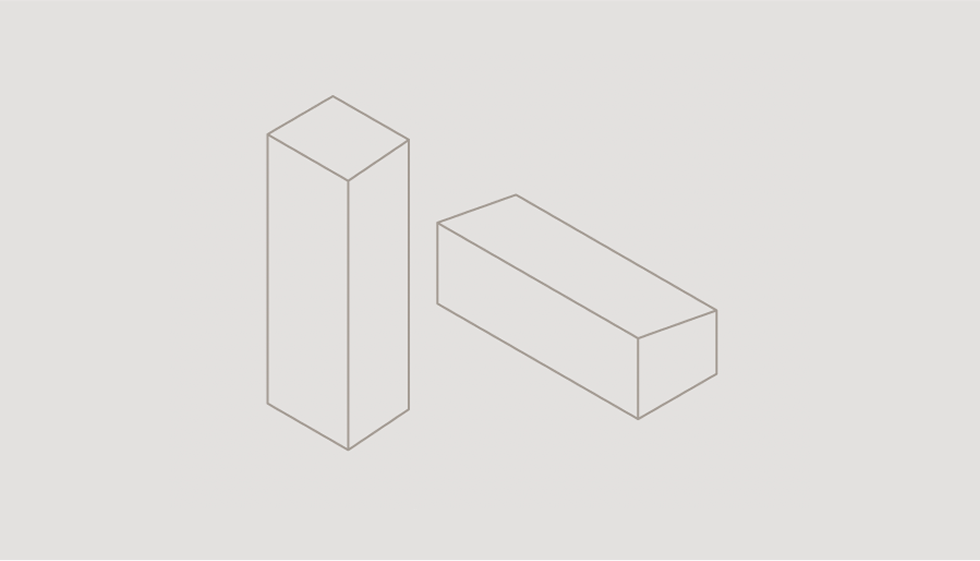
ANDALUX A60Hc-Un
Contactez-nous
Veuillez sélectionner l'option qui décrit le mieux le sujet que vous souhaitez discuter avec nous. Cela nous aidera à orienter votre demande vers la bonne personne chez PCO.