Cokerie
Notre offre pour l’industrie de la coksification
L’industrie de la cokéfaction est confrontée à des défis majeurs tels que la réduction des émissions de CO₂, de SOₓ et de NOₓ, la fluctuation des prix des matières premières ainsi que l’adaptation à l’évolution de la demande mondiale en acier.
Ces défis imposent une amélioration de l’efficacité des installations et la construction de nouveaux équipements onéreux afin de limiter l’impact environnemental. Nous soutenons ce secteur en proposant des solutions éprouvées de revêtements réfractaires ainsi que la fabrication de produits réfractaires alumino-silicatés. Nos briques et pièces façonnées sont produites conformément aux spécifications du client ou aux normes telles que la DIN 1089-2. Nous adaptons pleinement notre offre au volume de la demande.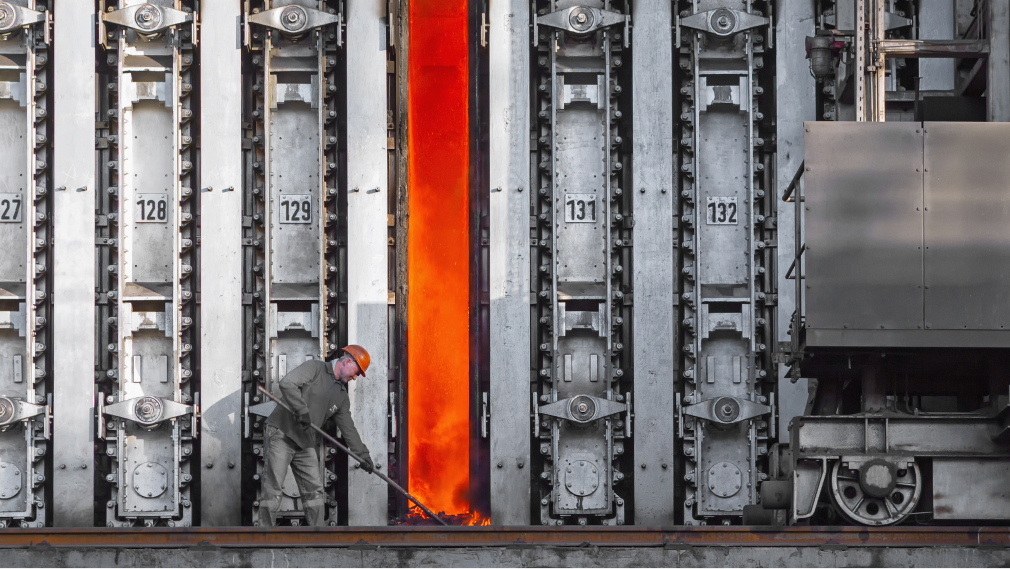
Comment pouvons-nous vous aider?
Conception
- Calculs thermiques avec Simu-Therm pour certains composants de batteries.
- Paquet complet de conception et d’ingénierie de revêtements réfractaires pour réacteurs, incluant : plans d’ensemble et de détail, plans d’armatures, plans d’atelier pour l’acier, plans de composants, fiches techniques, nomenclature des matériaux, instructions de montage, courbes de séchage, directives de mise en service et de maintenance.
- Inspection des revêtements réfractaires des réacteurs, zones régénératives, portes de chambres, toitures de fours.
- Documentation de fin de travaux pour les réparations.
Production et livraison
- Chamotte, chamotte-quartz, matériaux à haute teneur en alumine et isolants pour échangeurs de chaleur régénératifs, foyers, portes de chambre et toits de batteries à coke.
- Revêtements céramiques pour réacteurs de décomposition catalytique de NH₃ et unités de récupération de soufre (SRU).
- Revêtements céramiques pour rampes de déchargement de coke et décanteurs.
- Revêtements pour installations de trempe sèche du coke (CDQ).
- Revêtements céramiques pour toitures, régénérateurs, conduits de gaz de combustion et cheminées.
- Bétons et masses réfractaires, notamment pour les portes de batteries à coke.
Travaux de montage
- Montage sur site de nouveaux fours de cuisson, installations CDQ, réacteurs, revêtements céramiques de rampes à coke, conduits céramiques de gaz et revêtements de cheminées.
- Réparations et reconstructions (démontage et évacuation des déchets céramiques, réparations continues des chambres, régénérateurs, batteries et revêtements de réacteurs).
- Fourniture de tous les matériaux auxiliaires nécessaires.
- Planification et gestion de projet.
Fours et autres applications à haute température
Batterie de fours à coke
La batterie de fours à coke est un système complexe où le charbon est soumis à une pyrolyse à des températures dépassant 1200 °C. Les matériaux réfractaires y jouent à la fois un rôle structurel et technologique, tout en étant exposés à des conditions extrêmes de température, d’érosion et de corrosion. Nous proposons une solution complète en matériaux pour la structure de la batterie.
Portée: Conception du garnissage Fourniture des matériaux réfractaires Services de montage du garnissage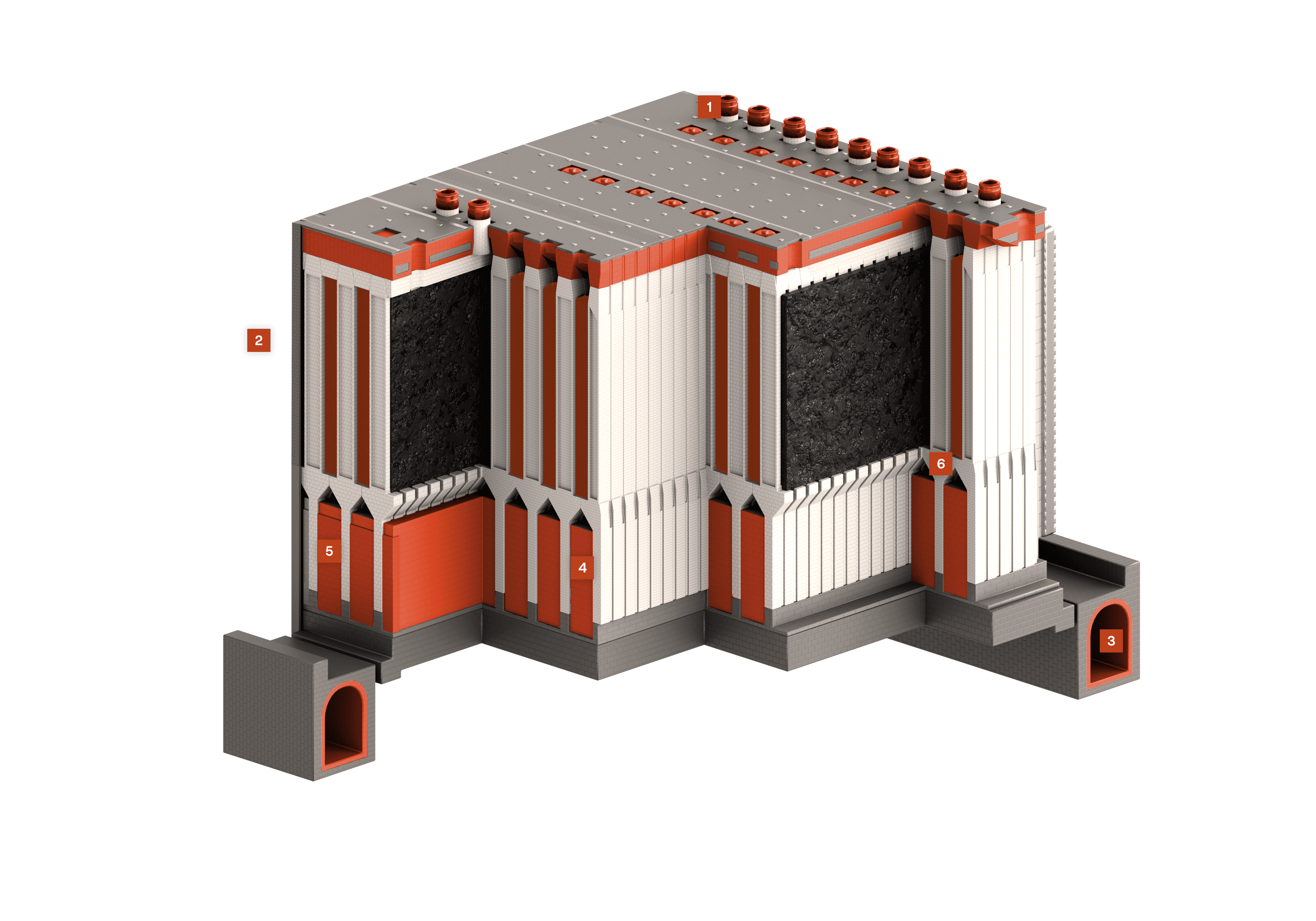
Les matériaux pour la toiture doivent présenter de bonnes propriétés isolantes ainsi qu’une densité appropriée. Nous avons développé les matériaux isolants ISOLUX et des produits à densité accrue qui stabilisent les chambres de la batterie. La couche supérieure, résistante aux variations de conditions et à l’usure, est réalisée en RESIMAX, un matériau offrant une haute résistance mécanique et une faible absorption d’eau.
Soumises à des cycles thermiques intenses, les portes doivent être fabriquées à partir de matériaux résistants aux chocs thermiques. Nous avons conçu les matériaux KORMAX et PCOCAST, à base de silice amorphe et de cordiérite, qui prolongent la durabilité des portes. Ils sont proposés sous forme de pièces façonnées, de préfabrications en béton ou de masses à couler sur site.
Dans cette zone, nous utilisons le matériau SITONEX (chamotte-quartz), qui offre une faible rétraction secondaire, améliorant l’étanchéité de la maçonnerie des régénérateurs. Les briques à croisillons (checker bricks) sont produites avec une géométrie précise et des tolérances strictes, ce qui facilite leur mise en place.
W strefie pod komorami koksowniczymi używamy materiału kwarcowo-szamotowego SITONEX, który zapewnia minimalną skurczliwość wtórną, co poprawia szczelność obmurza regeneratorów. Kształtki kratownicowe (checker bricks) są produkowane z precyzyjnie określoną geometrią i tolerancjami, co ułatwia ich zabudowę.
Pour limiter les pertes thermiques, nous utilisons des produits isolants légers ISOLUX dotés d’un système d’emboîtement, qui renforce l’étanchéité et réduit le transfert de chaleur vers l’extérieur.
Dans la zone du tronc, exposée aux variations thermiques soudaines, nous recommandons des produits spéciaux à haute résistance au choc thermique (briques TSR). Notre matériau, riche en phase mullitique, garantit une résistance thermique et mécanique exceptionnelle.
Comment pouvons-nous vous aider ?
Vous souhaitez recevoir un conseil gratuit ou poser une question sur le choix d’un revêtement réfractaire? Laissez-nous vos coordonnées – nous vous rappellerons!
Contactez-nousLes déformations et écarts dimensionnels des pièces façonnées empêchent une construction rapide et étanche de la structure.
Disponibilité limitée des matériaux réfractaires en raison de la grande taille et de la complexité des moules.
Nécessité d’utiliser des matériaux à faible retrait secondaire, afin de garantir l’étanchéité de la maçonnerie.
Quai de déchargement du coke
Le quai de déchargement du coke ainsi que le décanteur sont des éléments essentiels d’une installation classique de cokéfaction utilisant la méthode de trempe humide. Leur rôle est due: refroidir le coke chaud avant son transport, réguler le flux de coke tombant sur le convoyeur.
Portée: Conception du garnissage Fourniture des matériaux réfractaires Services de montage du garnissage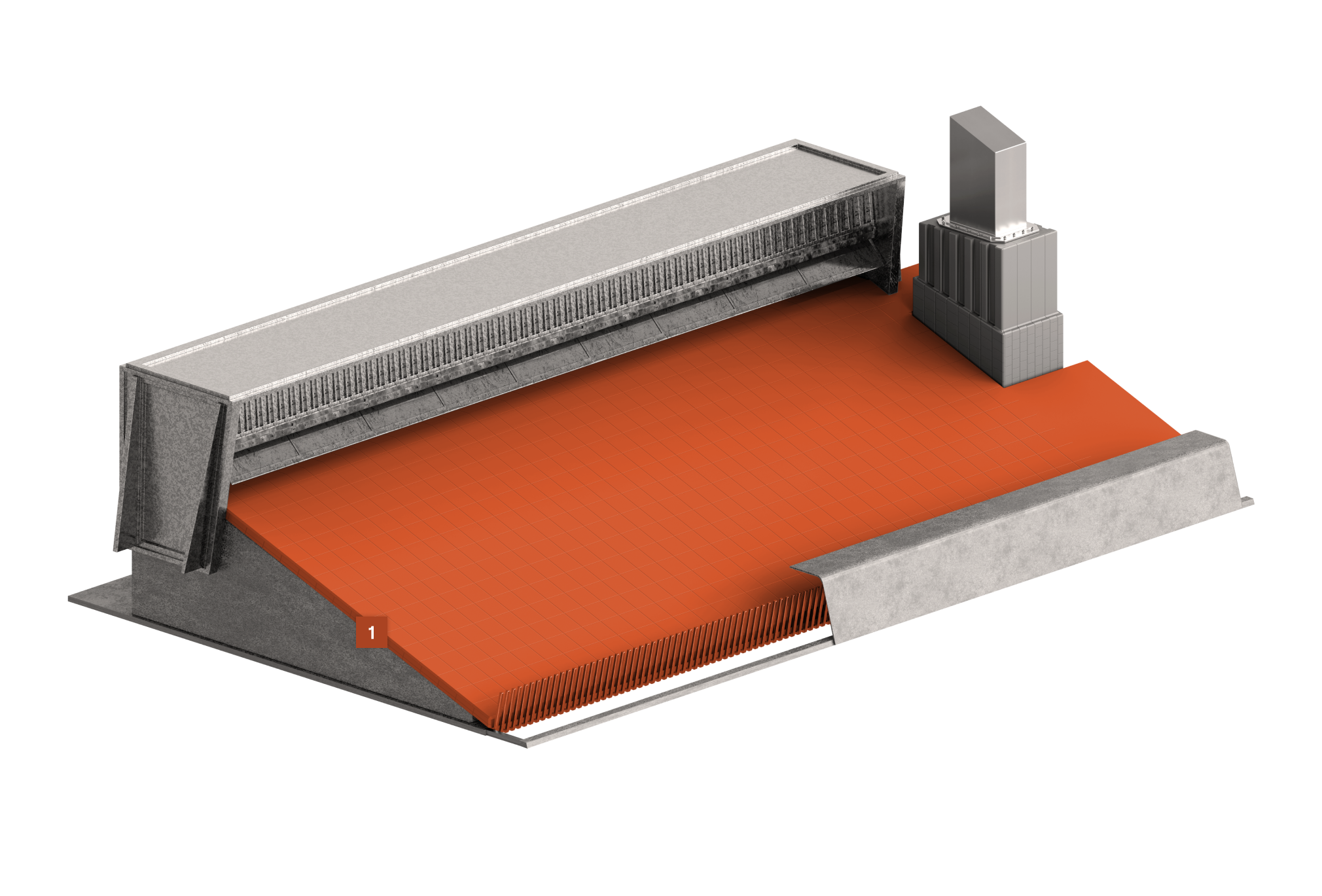
Le revêtement de la rame est soumis à des températures élevées, à des chocs thermiques, à des impacts mécaniques violents ainsi qu’à une érosion intense due à la chute continue du coke. Pour répondre à ces exigences, nous avons développé le matériau ABRAL ŻRMK, à base de corindon et de zirconium, conçu spécifiquement pour ce type d’application.
Comment pouvons-nous vous aider ?
Vous souhaitez recevoir un conseil gratuit ou poser une question sur le choix d’un revêtement réfractaire? Laissez-nous vos coordonnées – nous vous rappellerons!
Contactez-nousBlocage du coke pendant le déchargement à cause de l’usure du revêtement.
Blocage du coke dû à la surface rugueuse de la rampe.
Fonctionnement toute l’année en conditions extérieures → nécessité d’un revêtement résistant au gel.
Installation de trempe sèche du coke (CDQ)
Le coke expulsé des chambres des batteries doit être refroidi avant de pouvoir être transporté et transformé en toute sécurité. Ce refroidissement peut être effectué à l’aide d’une installation de trempe sèche du coke, dans laquelle le coke est refroidi par contact avec un gaz inerte en circulation, généralement de l’azote, au lieu d’être arrosé d’eau comme dans la méthode traditionnelle. Ce procédé protège l’environnement en réduisant les émissions de poussières et permet également de récupérer l’énergie thermique contenue dans le coke chaud. Les matériaux réfractaires utilisés dans cette installation doivent présenter une excellente résistance mécanique (abrasion, chocs) ainsi qu’une grande résistance aux chocs thermiques.
Portée: Conception du garnissage Fourniture des matériaux réfractaires Services de montage du garnissage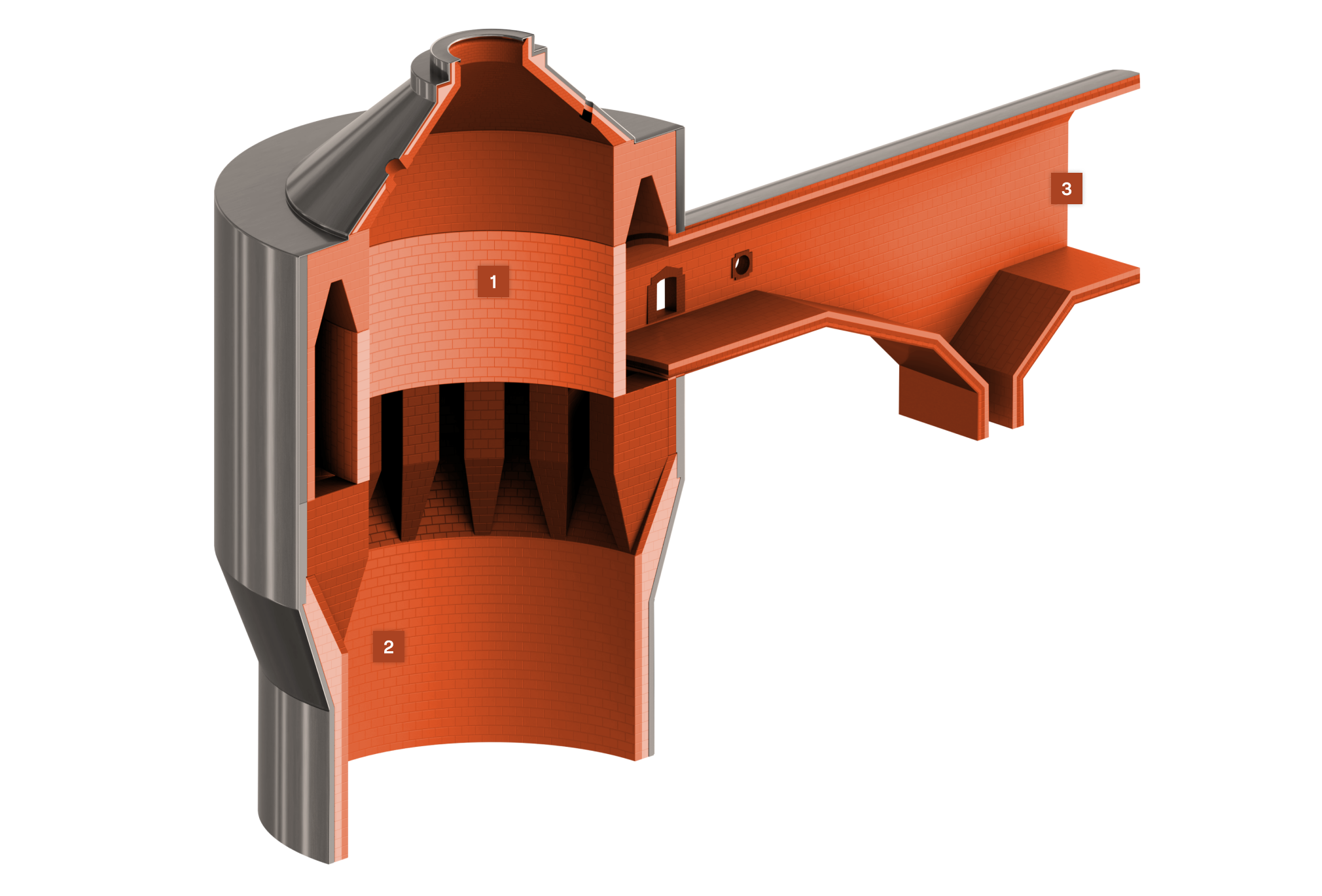
Cette zone de l’installation est soumise à certaines des conditions les plus extrêmes du processus. Elle est exposée à des températures très élevées (environ 900–1000 °C) provoquées par l’introduction du coke chaud, à des chocs thermiques sévères dus au chargement cyclique du matériau, ainsi qu’à des contraintes mécaniques intenses causées par les impacts du coke. Pour répondre à ces exigences, nous recommandons l’utilisation des matériaux des gammes ANDALUX et SUPERTON, qui se distinguent par leur forte teneur en phase mullitique, assurant une excellente résistance thermique et mécanique. Pour les couches isolantes, nous préconisons une combinaison d’isolants légers et denses de la gamme ISOLUX, qui minimisent efficacement les pertes thermiques tout en supportant les conditions de fonctionnement difficiles.
Bien que les conditions dans cette partie de l’installation soient légèrement moins sévères que dans la chambre de trempe, elles restent particulièrement exigeantes pour les matériaux réfractaires. La température y varie de 600 à 800 °C et diminue progressivement à mesure que le coke se refroidit. Le flux constant de gaz inertes peut entraîner l’érosion des matériaux, tandis que le déplacement du coke génère d’importantes sollicitations mécaniques abrasives. Les briques et cales des familles ANDALUX et SUPERTON sont parfaitement adaptées à ces conditions grâce à leur résistance optimale à l’abrasion et à l’érosion. Pour les couches isolantes, les matériaux de la gamme ISOLUX offrent une excellente isolation thermique tout en assurant une durabilité à long terme dans des environnements exigeants.
Le dépoussiéreur permet d’éliminer et de contrôler les poussières générées pendant le refroidissement du coke. Ces poussières peuvent constituer un risque environnemental et altérer la performance ainsi que la longévité de l’installation. Les revêtements réfractaires dans cette section sont exposés à un flux de gaz contenant une forte charge de particules de poussière et de coke, à une répartition thermique inégale pouvant provoquer des points chauds localisés, ainsi qu’à des phénomènes de corrosion chimique résultant du contact avec les composants présents dans les gaz et les poussières. Les matériaux des gammes ANDALUX, SUPERTON et NORMATON, recommandés par PCO, garantissent une exploitation fiable et durable grâce à leur grande résistance à l’abrasion, leur faible porosité, leur excellente résistance aux chocs thermiques, ainsi que leur haute stabilité chimique, qui limite les risques de dégradation dans un environnement agressif.
Comment pouvons-nous vous aider ?
Vous souhaitez recevoir un conseil gratuit ou poser une question sur le choix d’un revêtement réfractaire? Laissez-nous vos coordonnées – nous vous rappellerons!
Contactez-nousLe flux continu de gaz chauds et de poussières provoque l’érosion progressive de la surface du revêtement réfractaire.
Les variations cycliques de température entraînent la formation de microfissures et la dégradation du matériau.
Les produits issus de la combustion du coke peuvent contenir des substances chimiques réactives qui accélèrent l’usure des matériaux réfractaires.
Réacteur de décomposition catalytique de l’ammoniac et de production de soufre selon le procédé Claus
Le réacteur de décomposition catalytique de l’ammoniac, utilisé dans le procédé Claus, est un élément clé du système de récupération du soufre à partir des gaz résiduels. Il joue un rôle essentiel dans la réduction des émissions de composés nocifs vers l’atmosphère. En raison des conditions de fonctionnement complexes, les revêtements réfractaires de ce type d’installation sont soumis à des contraintes particulièrement sévères.
Portée: Conception du garnissage Fourniture des matériaux réfractaires Services de montage du garnissage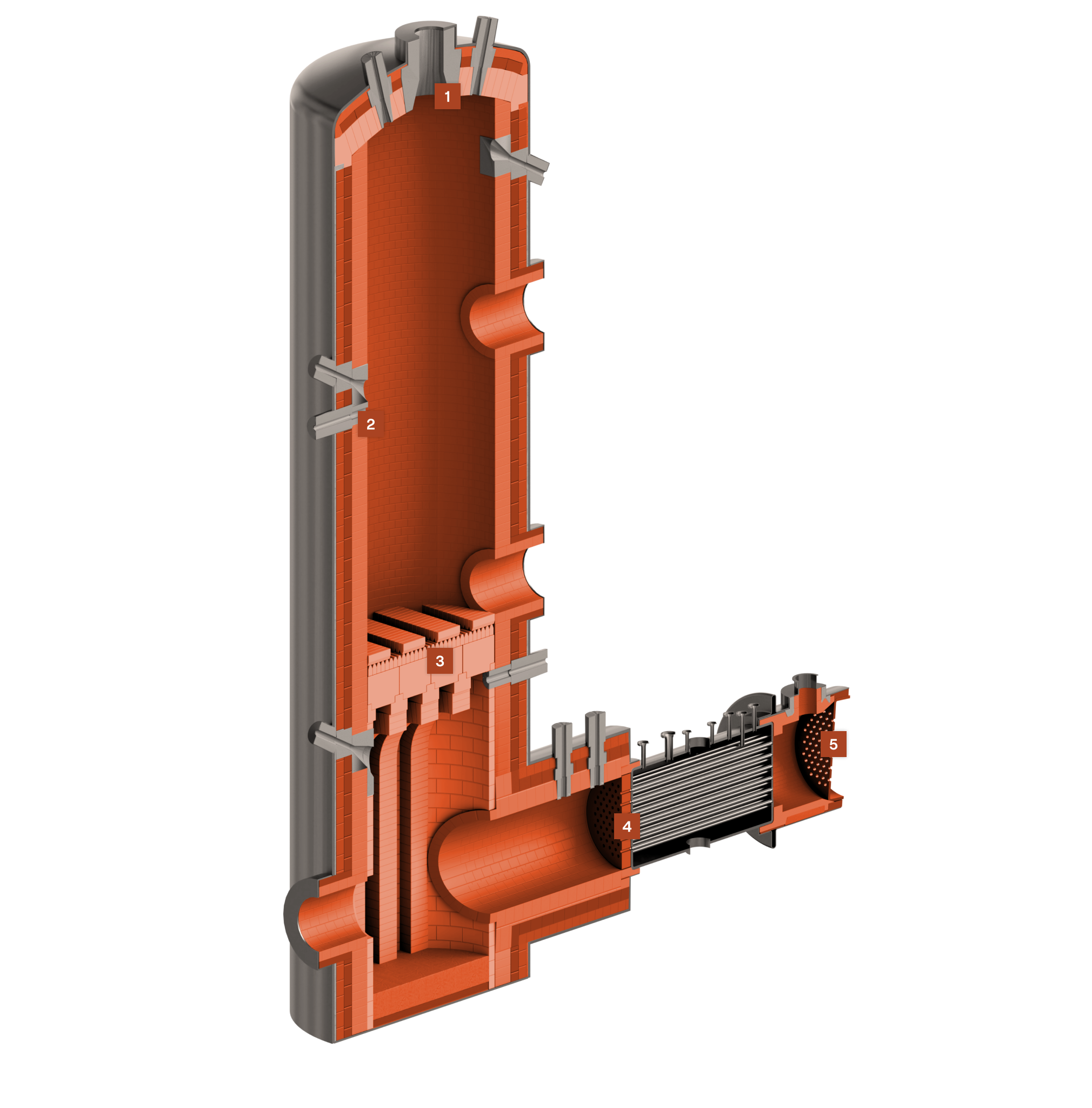
Le brûleur est exposé à une production de chaleur intense, en particulier lors des phases de mise en service, ce qui provoque des contraintes thermiques considérables sur les éléments céramiques. Le matériau utilisé doit donc offrir une résistance maximale aux chocs thermiques ainsi qu’à des températures localement très élevées.
Cette section est également soumise à des températures élevées, bien qu’en général inférieures à celles du brûleur. Le principal défi ici est l’exposition prolongée à des gaz réactifs. La présence de SO₂ et d’autres composés soufrés peut provoquer une corrosion chimique progressive du matériau réfractaire, entraînant à terme une perte d’efficacité de l’isolation thermique et des perturbations dans le fonctionnement du réacteur, voire une dégradation du revêtement métallique.
La grille céramique, qui soutient le lit catalytique, fonctionne à haute température et est directement exposée au flux de gaz chauds et au poids du catalyseur. Le revêtement réfractaire dans cette zone doit donc posséder une stabilité thermique élevée ainsi qu’une bonne résistance chimique aux gaz de procédé.
Le plancher doit assurer à la fois une bonne étanchéité et une isolation thermique efficace tout en permettant l’installation correcte des tubes en corindon provenant de la chaudière haute pression.
Dans cette zone, le revêtement réfractaire est principalement exposé à une température très élevée ainsi qu’à des phénomènes de corrosion chimique liés aux résidus réactifs présents dans les gaz.
Comment pouvons-nous vous aider ?
Vous souhaitez recevoir un conseil gratuit ou poser une question sur le choix d’un revêtement réfractaire? Laissez-nous vos coordonnées – nous vous rappellerons!
Contactez-nousDans certaines conditions de fonctionnement, une condensation d’acide sulfurique peut survenir, entraînant une corrosion chimique du revêtement réfractaire.
Une isolation inadaptée ou insuffisante de la paroi en acier du réacteur peut provoquer une surchauffe de l’enveloppe métallique.
Difficulté à trouver une entreprise de montage disposant de l’expertise spécialisée nécessaire à l’installation de ce type de revêtement.
Pourquoi PCO
Nous fabriquons toutes les formes
Précision dimensionnelle garantie
Une équipe de maçons expérimentés
Produits et services sélectionnés
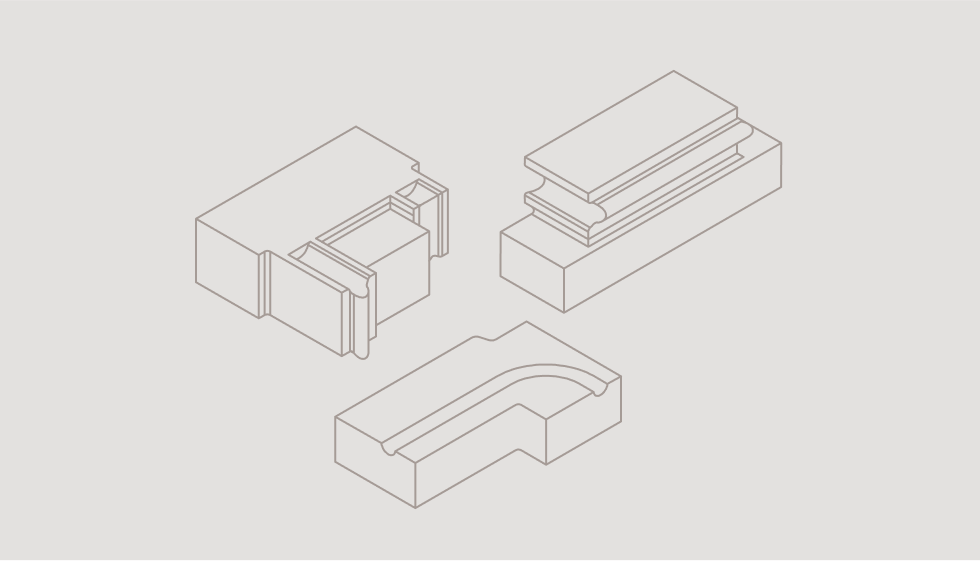
SITONEX
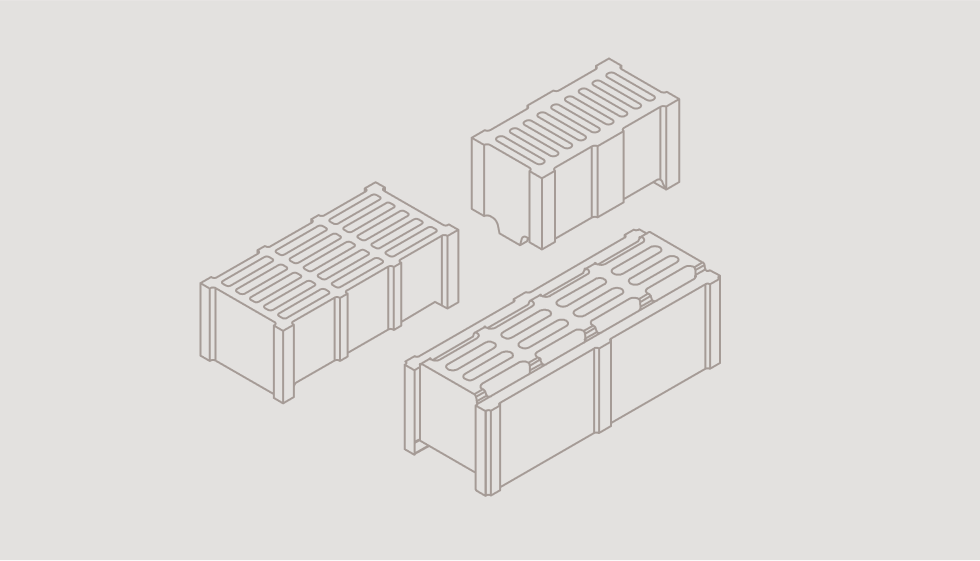
Briques à croisillons
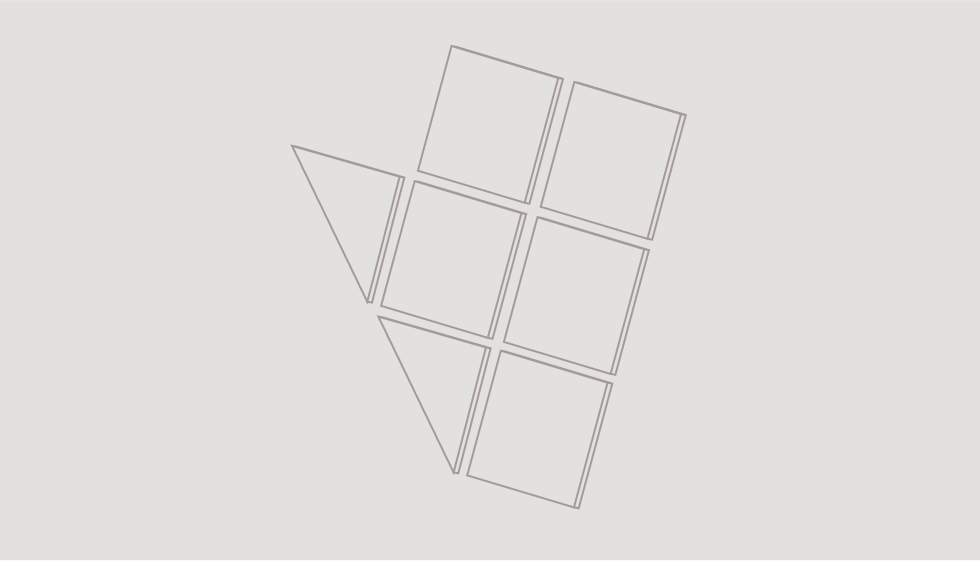
ABRAL ŻRMK
Contactez-nous
Veuillez sélectionner l'option qui décrit le mieux le sujet que vous souhaitez discuter avec nous. Cela nous aidera à orienter votre demande vers la bonne personne chez PCO.