Ciment, chaux et papier
Notre offre pour l’industrie du ciment, de la chaux et du papier
Le processus de calcination des carbonates de calcium et leur traitement thermique ultérieur jouent un rôle clé dans de nombreuses industries, notamment dans le bâtiment et la chimie.
Le clinker de ciment et la chaux calcinée sont des composants essentiels des matériaux de construction. La chaux vive est également largement utilisée dans divers procédés industriels tels que la production de pâte à papier, de soude ou de sucre. Aujourd’hui, les processus reposant sur la calcination font face à de fortes pressions liées à l’efficacité et aux exigences de durabilité. Les émissions de dioxyde de carbone issues des matières premières ont un impact significatif sur l’économie du processus, d’où la nécessité d’assurer une efficacité maximale à chaque étape. Des campagnes de production sans défaillance, la réduction des arrêts pour maintenance et l’utilisation de revêtements de fours à haute efficacité thermique peuvent apporter un avantage concurrentiel important. La mission de PCO est de soutenir ses partenaires dans le domaine des technologies réfractaires pour les fours à chaux et à ciment — depuis les études d’ingénierie, en passant par le choix conjoint des matériaux et des méthodes de montage les plus adaptés, jusqu’à la logistique vers n’importe quelle destination dans le monde, le montage et la supervision. Nous sommes convaincus que la qualité fiable de nos produits et de nos services, associée à un accompagnement global, permet de minimiser les interruptions de production et aide nos partenaires à renforcer leur compétitivité tout en atteignant leurs objectifs de développement durable.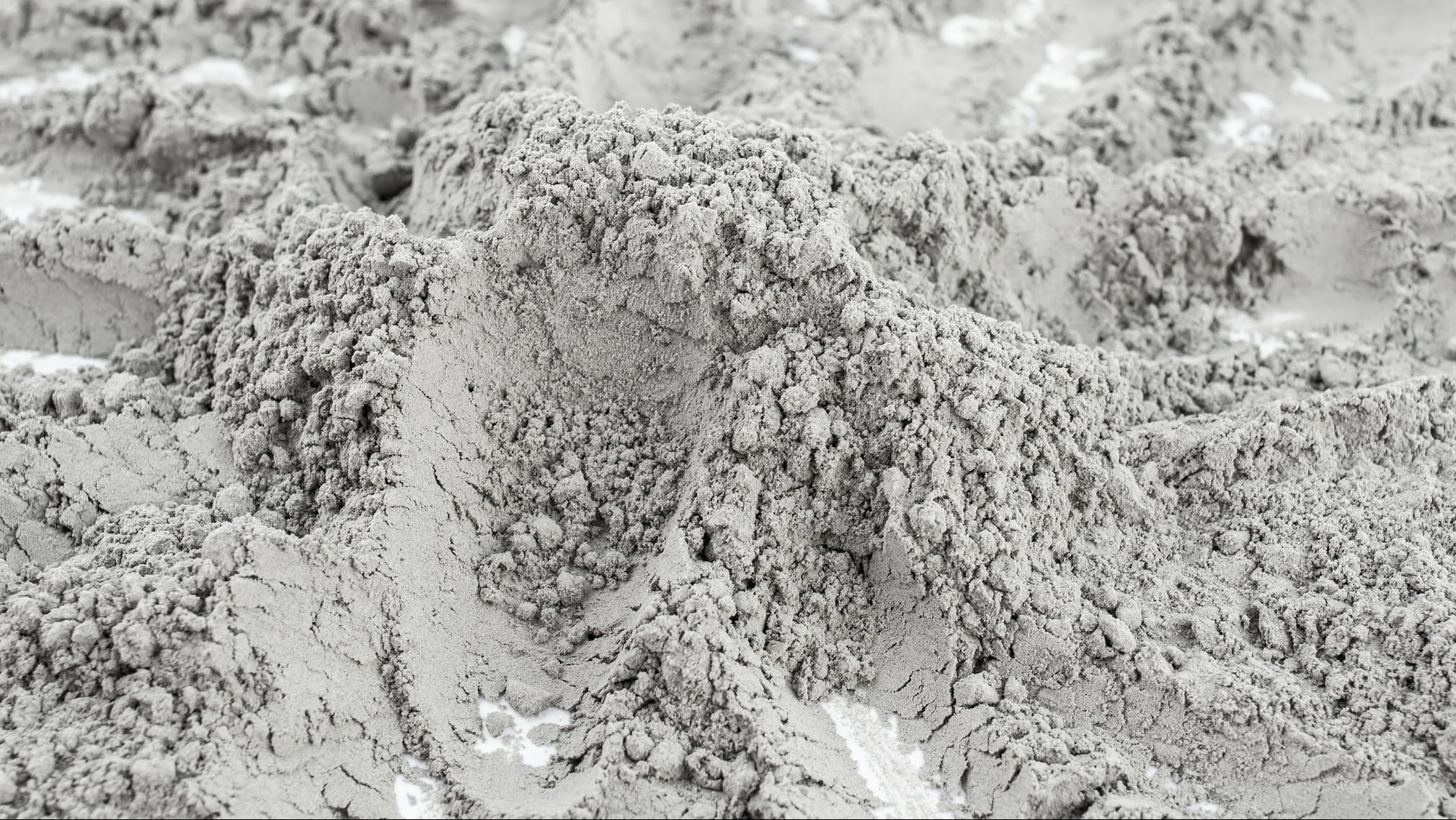
Comment pouvons-nous vous aider?
Nous concevons
- La sélection des qualités de matériaux réfractaires appropriés, adaptés aux conditions spécifiques de votre procédé de production.
- Le choix de la configuration optimale du revêtement réfractaire, prenant en compte la conception des équipements, les zones de processus, les conditions d’exploitation ainsi que les préférences de l’utilisateur.
- Des analyses de flux thermiques pour différents scénarios de revêtement (comparaisons A/B).
- L’optimisation de la conception des revêtements en vue de prolonger leur durée de vie et de réduire les pertes de chaleur.
Nous fabriquons et livrons
- Des produits chamottés et à haute teneur en alumine à résistance accrue à l’abrasion, destinés aux tours d’échange thermique, conduits d’air tertiaire, calcinateurs, gaines et chambres de montée des installations de cimenterie, ainsi qu’aux zones d’entrée et de sortie plus froides des fours à chaux.
- Des bétons réfractaires innovants, à faible teneur ou sans ciment, enrichis en SiC et ZrO₂, pour un large éventail d’applications en cimenterie.
- Des produits isolants pour couches de protection dans les fours verticaux et rotatifs, y compris des qualités à résistance mécanique élevée.
- Des éléments préfabriqués prêts à installer, ne nécessitant pas de traitement thermique sur site.
Nous installons
- Le démontage et le montage de revêtements dans tous les équipements des installations de production de ciment, ainsi que dans les fours verticaux et multichambres.
- L’évacuation des anciens revêtements réfractaires (déchets céramiques).
- Les réparations courantes et les interventions d’urgence lors des campagnes de maintenance.
- Le conseil technique – analyse des causes d’usure, optimisation de la longévité des revêtements, supervision des travaux de pose.
Fours et autres applications à haute température
Cyclones supérieurs
Les cyclones supérieurs jouent un rôle essentiel dans la production de clinker, en assurant le bon mélange, le transfert et la distribution des matières premières. Dans cette zone, la matière est progressivement chauffée, les températures atteignant jusqu’à 600 °C. Le procédé est en continu, ce qui exige des matériaux réfractaires durables et résistants à l’usure. Le revêtement réfractaire d’un cyclone peut être divisé en trois zones principales : la voûte, le cylindre (fût) et le cône. Le principal défi pour le revêtement réfractaire dans cette partie de l’installation est l’abrasion causée par le flux intense de matières solides ; l’effet de la température élevée est relativement secondaire. Les cyclones supérieurs étant soumis à de très longs cycles de maintenance – allant de plusieurs dizaines d’années – il est essentiel d’utiliser des matériaux particulièrement durables. PCO propose des solutions réfractaires adaptées aux conditions spécifiques de fonctionnement de ces équipements. Dans des conditions normales, des briques chamottées de la gamme NORMATON sont utilisées. En cas d’abrasion intensive, des chamottes renforcées comme EXTRATON sont recommandées. Dans certaines configurations, des bétons réfractaires sont également utilisés afin d’augmenter la longévité et la stabilité de fonctionnement.
Portée: Conception du garnissage Fourniture des matériaux réfractaires Services de montage du garnissage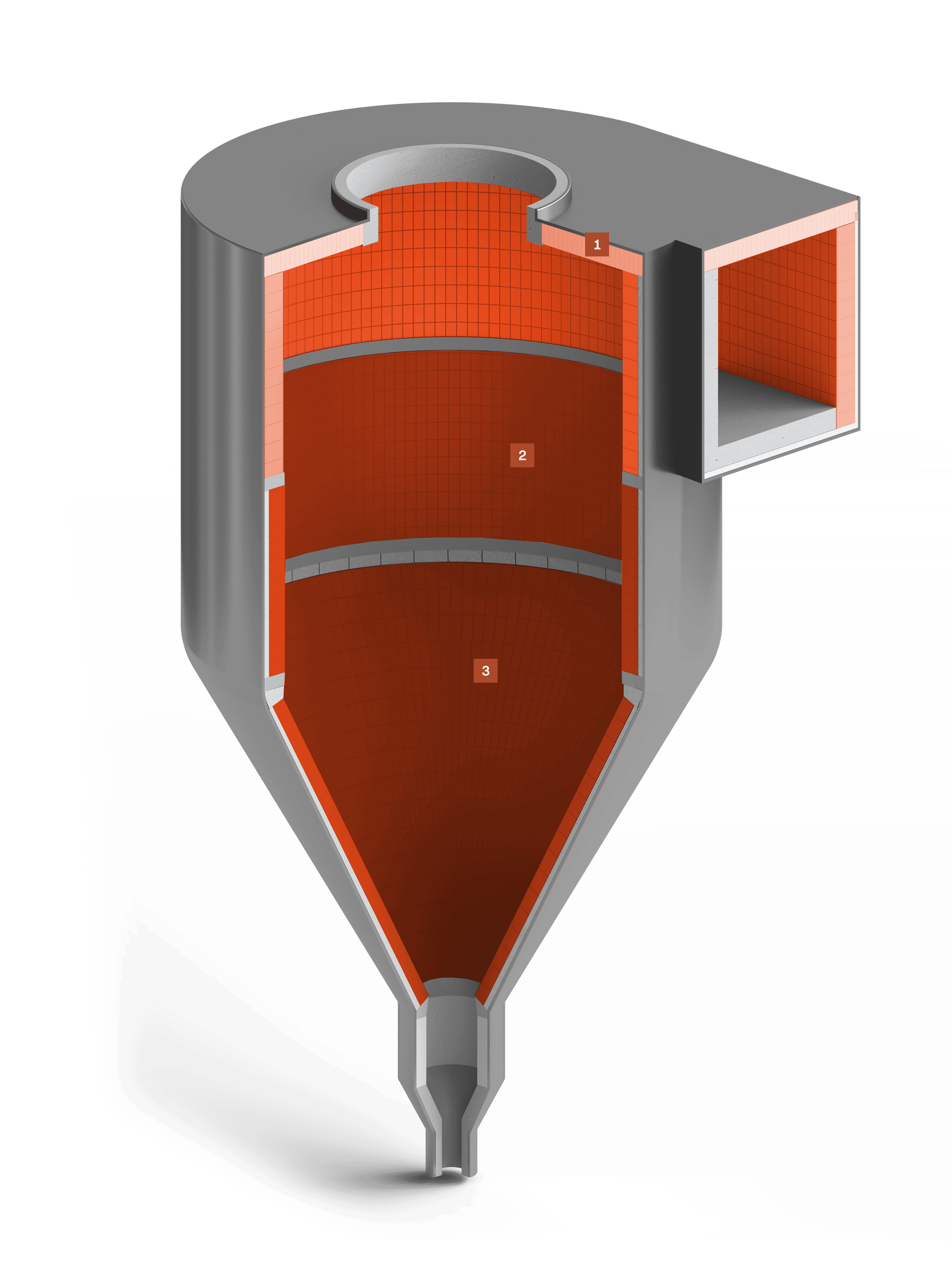
La voûte du cyclone supérieur est principalement exposée à l’abrasion par les gaz chargés en particules. Les effets de la température et des contraintes mécaniques y sont limités, ce qui signifie des conditions d’exploitation relativement douces. La voûte est réalisée en plusieurs couches, dominées par des briques en forme de coin – tant pour les couches de travail que pour les couches isolantes. Cette structure multicouche assure une bonne protection contre les gaz et limite l’usure du revêtement. Dans cette zone, en raison de conditions modérées, les produits à faible teneur en alumine de la série EXTRATON, ainsi que les briques isolantes légères ISOLUX, sont particulièrement adaptés. Ces matériaux offrent une résistance suffisante à l’abrasion gazeuse tout en garantissant une excellente isolation thermique.
Le cylindre du cyclone supérieur est exposé à l’abrasion et aux contraintes mécaniques, mais celles-ci restent modérées. Comme pour la voûte, le revêtement est constitué de plusieurs couches, principalement en briques de type coin, utilisées pour les couches de travail et isolantes. Cette structure permet une répartition uniforme des charges et une protection durable contre l’usure. Les mêmes matériaux que pour la voûte sont utilisés ici : EXTRATON pour les performances mécaniques et ISOLUX pour l’isolation thermique.
Le cône est la zone la plus sollicitée mécaniquement du cyclone, bien que les risques pour le revêtement réfractaire restent faibles dans l’ensemble. En raison de sa géométrie complexe, le revêtement est réalisé en béton réfractaire, ce qui permet une adaptation optimale aux formes irrégulières et facilite la pose. Ce type de conception permet également une répartition homogène du matériau sur les surfaces difficiles.
Comment pouvons-nous vous aider ?
Vous souhaitez recevoir un conseil gratuit ou poser une question sur le choix d’un revêtement réfractaire? Laissez-nous vos coordonnées – nous vous rappellerons!
Contactez-nousComment minimiser l’écaillage des briques réfractaires en cas de cycles thermiques rapides ?
Quel béton de réparation offre la meilleure résistance à l’abrasion par des particules volantes ?
Comment protéger le revêtement céramique contre la corrosion provoquée par les alcalins ou les attaques salines ?
Cyclones inférieurs
Les cyclones inférieurs jouent un rôle clé dans la production de clinker, assurant un mélange, un transfert et une distribution intensifs des matières premières. Dans cette zone, les températures peuvent atteindre jusqu’à 950 °C, soit bien plus que dans les cyclones supérieurs. Une caractéristique importante de leur fonctionnement est la pré-calcination partielle du calcaire, ce qui améliore l’efficacité des étapes suivantes du procédé. Sur le plan du revêtement réfractaire, les cyclones inférieurs comprennent : une voûte, un fût cylindrique et un cône inférieur. Dans cette partie de l’installation, le revêtement est soumis à des conditions bien plus agressives que dans les cyclones supérieurs. Dans des conditions standards, on utilise des briques multi-chamottées enrichies en andalousite et en carbure de silicium, issues des gammes EXTRATON et ABRAL, qui offrent une excellente résistance à l’abrasion et aux attaques alcalines. Pour les revêtements réalisés en béton, les matériaux GELCAST, MULCAST et NxGel sont recommandés pour leur grande résistance aux carburants alternatifs et aux environnements chimiques agressifs.
Portée: Conception du garnissage Fourniture des matériaux réfractaires Services de montage du garnissage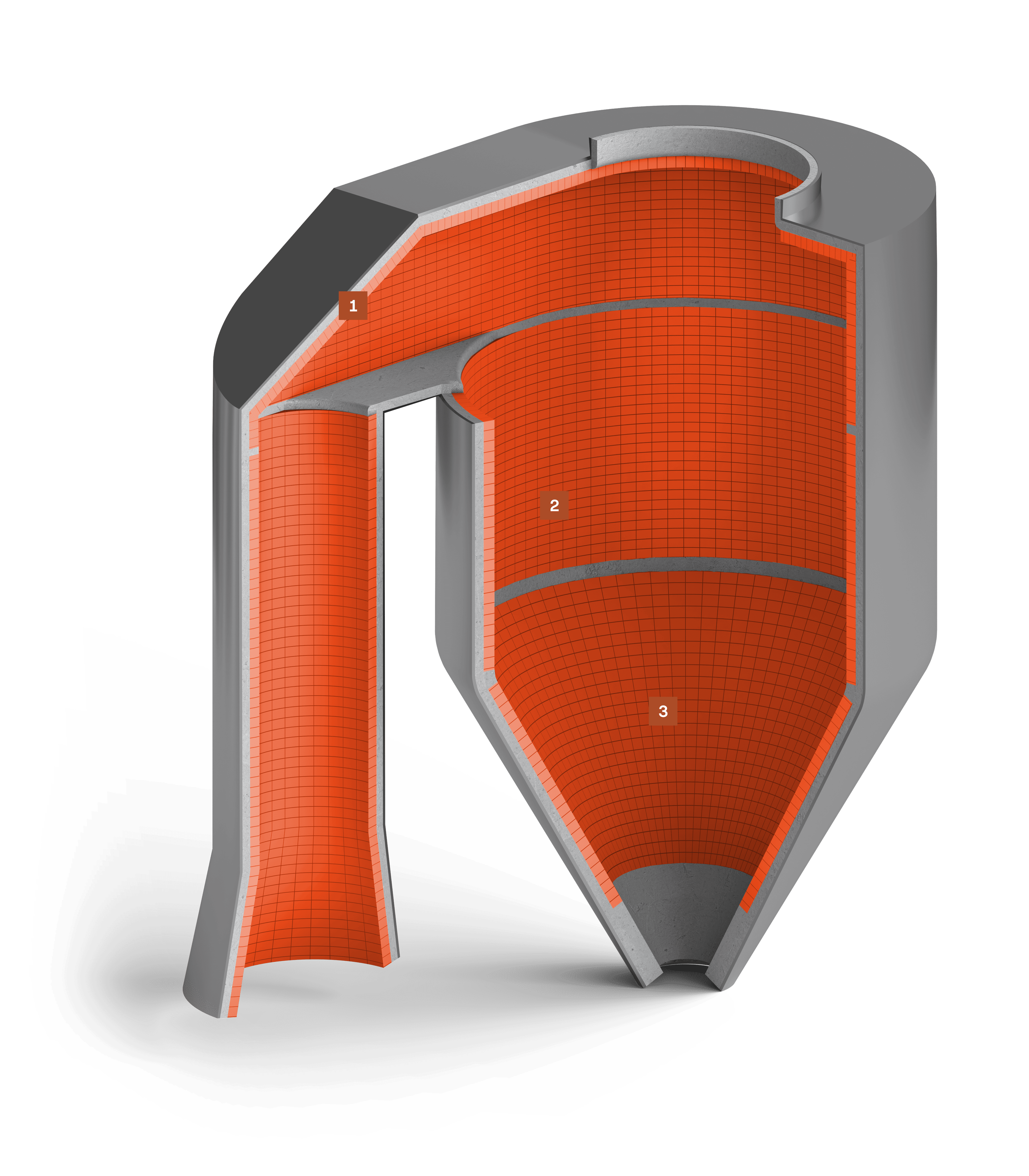
La voûte du cyclone inférieur est principalement exposée à l’abrasion par les gaz chargés en particules volatiles. Bien que les contraintes mécaniques et thermiques soient limitées, les conditions restent plus sévères que dans les cyclones supérieurs. Le revêtement doit également faire face à des attaques chimiques et à la formation de dépôts incrustants, ce qui augmente les risques de dégradation. La construction est multicouche, avec des briques en forme de coin dans les couches de travail et d’isolation. Cette configuration permet une répartition progressive des charges et une meilleure résistance à l’abrasion et aux agressions chimiques.
Le fût du cyclone inférieur subit une combinaison de contraintes : abrasion, agressions mécaniques et attaques chimiques (notamment alcalines). Ce type de sollicitation multiple nécessite un revêtement résistant à l’érosion mécanique ainsi qu’à la dégradation chimique. Comme pour la voûte, le revêtement est formé de plusieurs couches, principalement à base de briques en coin. Cette conception multicouche permet de répartir les efforts de manière homogène et de prolonger la durée de vie du revêtement.
Le cône est la zone la plus fortement sollicitée mécaniquement, chimiquement et par abrasion. En raison de sa forme complexe et des difficultés de mise en œuvre, cette zone est généralement revêtue de béton réfractaire. Cela permet une meilleure adaptation à la géométrie du cône, réduisant ainsi les contraintes localisées et les risques de dommages. Dans cette zone, il est impératif que le matériau soit résistant à l’ensemble des contraintes : mécaniques, chimiques et abrasives.
Comment pouvons-nous vous aider ?
Vous souhaitez recevoir un conseil gratuit ou poser une question sur le choix d’un revêtement réfractaire? Laissez-nous vos coordonnées – nous vous rappellerons!
Contactez-nousQuel béton réfractaire offre le meilleur compromis entre résistance à l’abrasion et tolérance au choc thermique ?
Comment compenser la différence de dilatation entre les couches céramiques et l’enveloppe en acier pour éviter les fissures ?
Comment limiter les incrustations de poussières sur le revêtement réfractaire?
Le calcinateur
Le calcinateur, principalement utilisé pour le préchauffage et la calcination des matières premières calcaires, transfère une partie du processus de combustion et de décarbonatation du four rotatif vers la tour d’échangeurs thermiques. Grâce à l’utilisation de combustibles alternatifs, le calcinateur permet de réduire les émissions de gaz et de diminuer les coûts d’exploitation. Cependant, les conditions de fonctionnement y sont nettement plus exigeantes, ce qui impose l’emploi de matériaux réfractaires avancés. Les températures dans le calcinateur varient de 800 à 1100 °C. Le canal du calcinateur est exposé à de fortes températures ainsi qu’à des agents corrosifs (SOₓ, NOₓ, alcalis, chlore, soufre) qui provoquent une usure abrasive du revêtement. C’est pourquoi l’on utilise des bétons réfractaires à faible teneur ou sans ciment, enrichis en zircone et en carbure de silicium. Pour les réparations, des bétons projetés sont utilisés. Si un revêtement en briques est envisagé, il doit s’agir de produits haute teneur en alumine, résistants aux attaques chimiques, aux températures élevées et aux chocs thermiques. Le revêtement du calcinateur est généralement multicouche : une couche de travail, une couche de protection et une couche isolante, assurant sa durabilité dans des conditions extrêmes. Le cycle de maintenance varie de quelques années selon les conditions de fonctionnement et la part de combustibles alternatifs utilisés.
Portée: Conception du garnissage Fourniture des matériaux réfractaires Services de montage du garnissage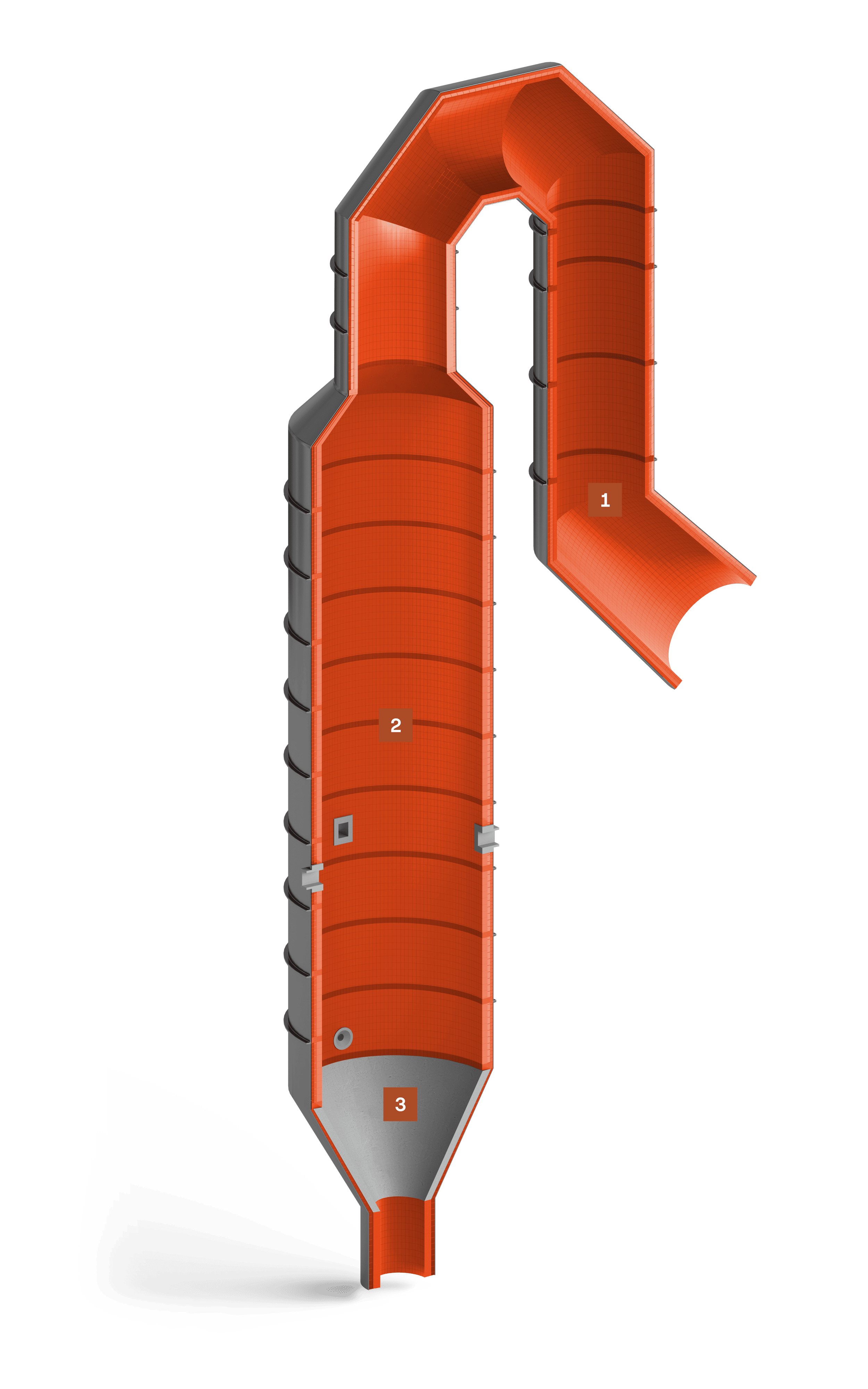
Dans cette zone, les températures varient entre 700 et 900 °C. Le principal risque pour le revêtement est l’abrasion mécanique et l’érosion chimique causées par l’arrivée de la farine crue. Il est également fréquent d’observer des dépôts (soufre et chlore, en cas de combustibles alternatifs). On privilégie ici les bétons réfractaires haute alumine, enrichis en ZrO₂ ou en SiC. En cas d’utilisation de briques, il faut choisir des briques haute alumine, résistantes à l’abrasion et au choc thermique.
Les températures y dépassent les 1000 °C, atteignant localement 1200 °C près des brûleurs. C’est l’une des zones les plus sévères pour les réfractaires dans toute l’installation. Cette zone est soumise à des attaques agressives d’alcalis, notamment dues à l’utilisation exclusive de combustibles alternatifs. Les bétons et briques utilisés ici doivent être haute alumine avec des additifs améliorant la résistance chimique et mécanique.
Les températures y restent élevées, autour de 1000 °C. Le risque principal est la présence d’alcalis, issus de la combustion. On y utilise des bétons haute alumine, à faible ou sans teneur en ciment. En cas de pose en briques, des briques haute alumine avec carbure de silicium sont recommandées. Le revêtement est souvent sujet à l’encrassement par des dépôts chimiques liés aux combustibles alternatifs. Ces dépôts nécessitent un nettoyage à l’air ou à l’eau lors des maintenances. Il faut également prévoir une bonne résistance aux chocs mécaniques, car les dépôts détachés des zones supérieures tombent dans la zone inclinée du bas du calcinateur.
Comment pouvons-nous vous aider ?
Vous souhaitez recevoir un conseil gratuit ou poser une question sur le choix d’un revêtement réfractaire? Laissez-nous vos coordonnées – nous vous rappellerons!
Contactez-nousQuel béton projeté résiste le mieux à l’abrasion par le clinker fritté et à la corrosion par le CO₂ ?
Quel type de matériau réfractaire est le plus adapté aux cycles courts de fonctionnement et aux risques de chocs thermiques ?
Comment concevoir le revêtement en tenant compte de la position du brûleur pour éviter les surchauffes localisées sur l’enveloppe métallique ?
Conduit d’air tertiaire (TAD)
Dans le conduit d’air tertiaire (TAD), où la température varie de 1000 °C dans la zone chaude à environ 600 °C dans la zone froide, les conditions de service sont particulièrement exigeantes. Ce conduit fournit un flux d’air supplémentaire au procédé, ce qui améliore l’efficacité de la combustion et permet un contrôle précis de la température interne du four. Pour garantir une performance optimale du processus, les paramètres clés – débit d’air, température, pression – peuvent être ajustés dynamiquement grâce à des systèmes avancés de surveillance et de contrôle.
Portée: Conception du garnissage Fourniture des matériaux réfractaires Services de montage du garnissage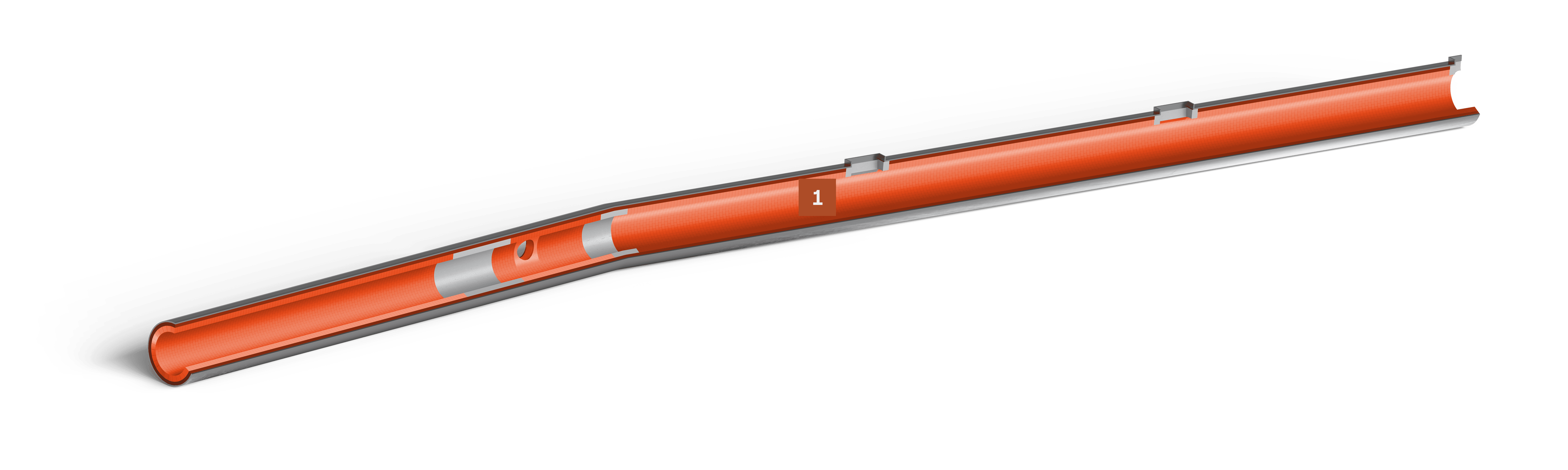
La principale difficulté liée au revêtement réfractaire du canal d’air tertiaire réside dans son faible diamètre, qui amplifie l’impact de l’environnement abrasif – les particules y circulent à grande vitesse et sous haute pression. Pour améliorer la durabilité, PCO recommande l’utilisation de briques moulées EXTRATON ainsi que de bétons chamottés PCOCAST, enrichis en carbure de silicium ou zircone, qui augmentent la résistance à l’abrasion. En cas de conditions encore plus sévères (pression ou température élevées), il est recommandé d'utiliser des briques chamottées au carbure de silicium de la gamme ABRAL.
Comment pouvons-nous vous aider ?
Vous souhaitez recevoir un conseil gratuit ou poser une question sur le choix d’un revêtement réfractaire? Laissez-nous vos coordonnées – nous vous rappellerons!
Contactez-nousComment concevoir une structure multicouche du revêtement pour obtenir une température de surface cible sur la carcasse (par ex. < 200 °C) ?
Quel mortier réfractaire assure la solidité des joints de la couche de travail sous une pression d’air élevée ?
Quel matériau est le plus adapté pour le revêtement des coudes du conduit d’air tertiaire ?
Conduit de montée et chambre d’entrée du four
Le conduit de montée et la chambre d’entrée sont des éléments essentiels de l’installation cimentière, assurant le transfert du matériau préchauffé depuis les cyclones vers le four rotatif, où il subit un chauffage supplémentaire. Les températures y varient d’environ 500 °C dans la partie supérieure du conduit à 1100 °C à l’entrée du four. La chambre d’entrée (également appelée chambre de fumées) récupère les gaz chauds en sortie de four et les redirige vers les cyclones, permettant ainsi la récupération de chaleur. Les principaux risques pour le revêtement réfractaire dans cette zone sont les gaz agressifs (attaques alcalines), les chocs mécaniques ainsi que l’abrasion causée par le mouvement du matériau – particulièrement critique dans les installations équipées de calcinateurs, où la part de combustibles alternatifs est plus importante. Le revêtement réfractaire doit donc posséder une faible porosité et une haute résistance à l’abrasion. PCO Żarów propose des solutions complètes, de la conception au montage, incluant des briques et des bétons réfractaires à teneur en Al₂O₃ de 30 à 60 %, enrichis en additifs améliorant leur résistance chimique et mécanique.
Portée: Conception du garnissage Fourniture des matériaux réfractaires Services de montage du garnissage
Dans la partie supérieure du conduit, où la température ne dépasse pas 700 °C, on utilise des briques chamottées pour la couche de travail. PCO recommande les produits EXTRATON ou ABRAL, à résistance accrue à l’abrasion. Pour des conditions plus sévères, cette zone peut être revêtue de briques bauxitiques haute alumine (BAUXITEX) pour une protection renforcée.
Dans cette zone, les conditions sont beaucoup plus difficiles – température jusqu’à 1100 °C et attaque chimique intense. On y emploie généralement des briques haute alumine, à base d’andalousite ou de bauxite, renforcées par des additifs améliorant la résistance mécanique et chimique. PCO recommande les gammes ABRAL, ANDALUX, ainsi que les bétons ultra-faible teneur en ciment NxGel, spécialement conçus pour les processus de montée rapide en température.
Cette chambre est exposée principalement à une agression chimique des gaz chauds, mais aussi à des chocs mécaniques liés à la chute du matériau depuis le conduit, ainsi qu’au frottement lors de son passage vers le four rotatif. Un problème fréquent est l’encrassement du revêtement par les dépôts de matière première, pouvant aller jusqu’au blocage local du canal. Il est recommandé d’utiliser des matériaux réfractaires enrichis en carbure de silicium ou en zircone, conférant au revêtement une faible porosité et une non-mouillabilité, pour réduire les adhérences et garantir un bon écoulement du matériau.
Comment pouvons-nous vous aider ?
Vous souhaitez recevoir un conseil gratuit ou poser une question sur le choix d’un revêtement réfractaire? Laissez-nous vos coordonnées – nous vous rappellerons!
Contactez-nousQuel matériau améliore la résistance chimique du revêtement face aux sous-produits agressifs du procédé ?
Comment limiter l’érosion du revêtement à la jonction entre le conduit et la chambre ?
Quel matériau réfractaire convient le mieux aux conditions de choc thermique ?
Brûleur principal
Dans cette zone, la température peut dépasser 1500 °C. Le revêtement réfractaire est exposé à des variations thermiques brutales, à un rayonnement thermique intense, ainsi qu’à l’action d’oxydants et de composés soufrés. Cela impose l’utilisation de matériaux offrant une résistance exceptionnelle à la corrosion chimique et au choc thermique. Le revêtement céramique du brûleur ne se limite pas à protéger la carcasse en acier contre la dégradation : il permet aussi une gestion efficace du flux thermique, réduisant les pertes et augmentant l’efficacité de la combustion. Ce revêtement est rénové relativement fréquemment – le cycle de maintenance varie de quelques mois à un maximum d’un an.
Portée: Conception du garnissage Fourniture des matériaux réfractaires Services de montage du garnissage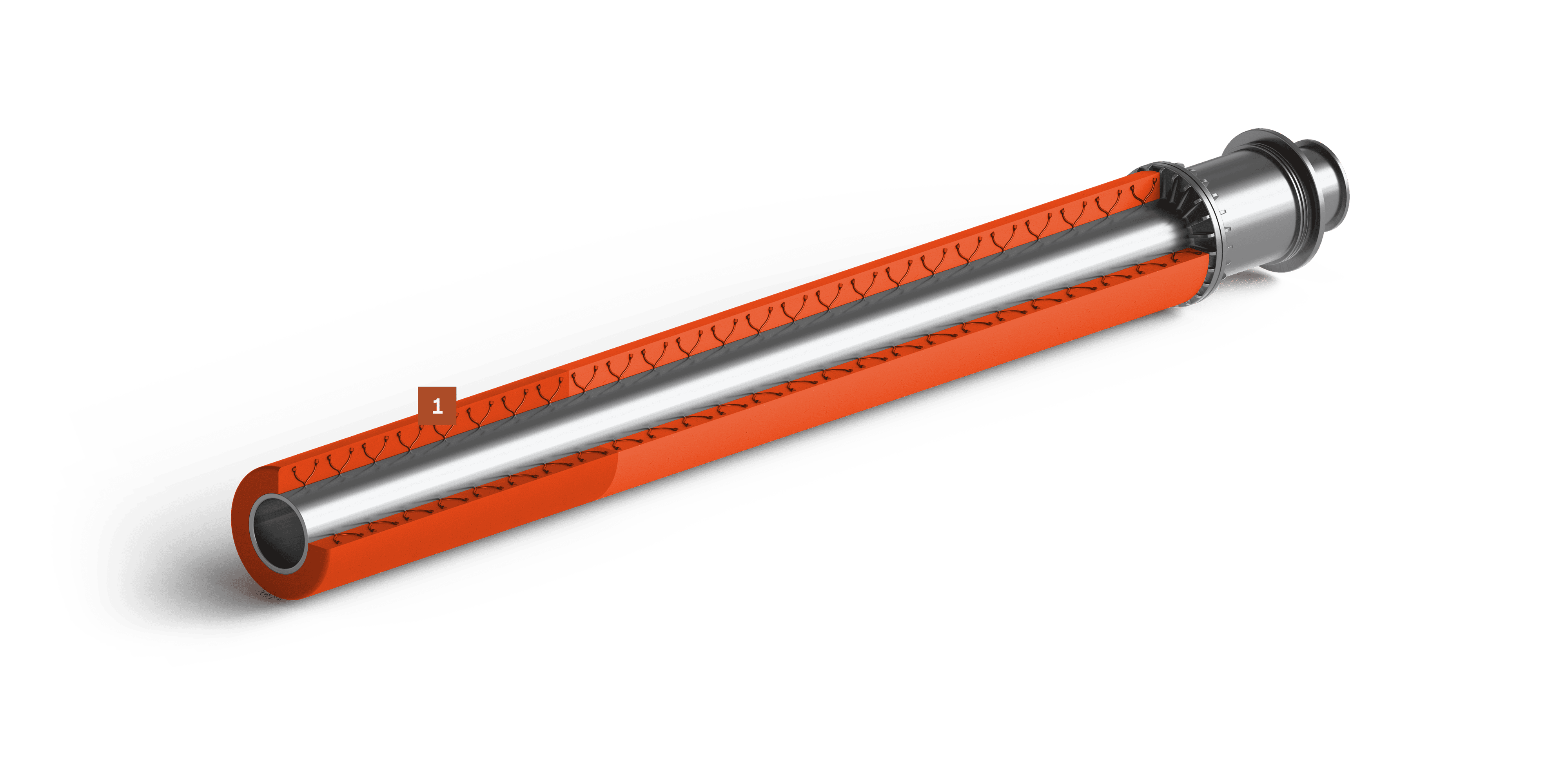
Le revêtement réfractaire de cette zone est exposé à des températures très élevées et à l’action agressive des combustibles alternatifs, nécessitant des réparations fréquentes. L’installation du revêtement dans la zone de flamme est particulièrement complexe, surtout lorsqu’il s’agit de couler le béton directement sur le brûleur. Cela exige non seulement une technologie appropriée, mais aussi un grand savoir-faire de la part des maçons. Il est crucial d’obtenir une consistance homogène du béton, assurant une bonne répartition du matériau et un réchauffement rapide, indispensable au maintien de la continuité de fonctionnement du four. Dans ces conditions extrêmes, les matériaux réfractaires doivent présenter une très haute résistance aux chocs thermiques et à l’agressivité des combustibles.
Comment pouvons-nous vous aider ?
Vous souhaitez recevoir un conseil gratuit ou poser une question sur le choix d’un revêtement réfractaire? Laissez-nous vos coordonnées – nous vous rappellerons!
Contactez-nousComment concevoir les éléments préfabriqués du brûleur pour éviter les brûlures localisées du revêtement ?
Quel matériau céramique choisir pour supporter les fortes contraintes thermiques dans la zone de flamme ?
Comment planifier les inspections du revêtement pour détecter à temps une usure excessive ?
Piec obrotowy
Le rôle principal du four rotatif dans la production de clinker est de chauffer la matière première à des températures très élevées (1350–1450 °C), provoquant sa calcination ainsi que les réactions chimiques nécessaires à la formation des minéraux du clinker. Le revêtement réfractaire de ce type de four est soumis à plusieurs mécanismes d’usure, notamment l’abrasion intense, les charges thermiques générées par le brûleur et la matière en mouvement, les contraintes mécaniques dues à la rotation de la coque en acier, la corrosion chimique causée par les gaz de combustion et les scories provenant des combustibles alternatifs, ainsi que l’attaque d’agents chimiques agressifs. Pour répondre à ces exigences, PCO propose une gamme complète de matériaux et de services adaptés aux fours rotatifs. L’offre comprend des produits réfractaires à haute teneur en alumine enrichis en carbure de silicium, offrant une excellente résistance à la corrosion chimique, à l’abrasion et aux chocs thermiques ; des matériaux à base d’andalousite sur liant chimique, reconnus pour leur durabilité exceptionnelle ; ainsi que des briques chamottées et haute alumine spécialement conçues pour les environnements abrasifs et chimiquement agressifs.
Portée: Conception du garnissage Fourniture des matériaux réfractaires Services de montage du garnissage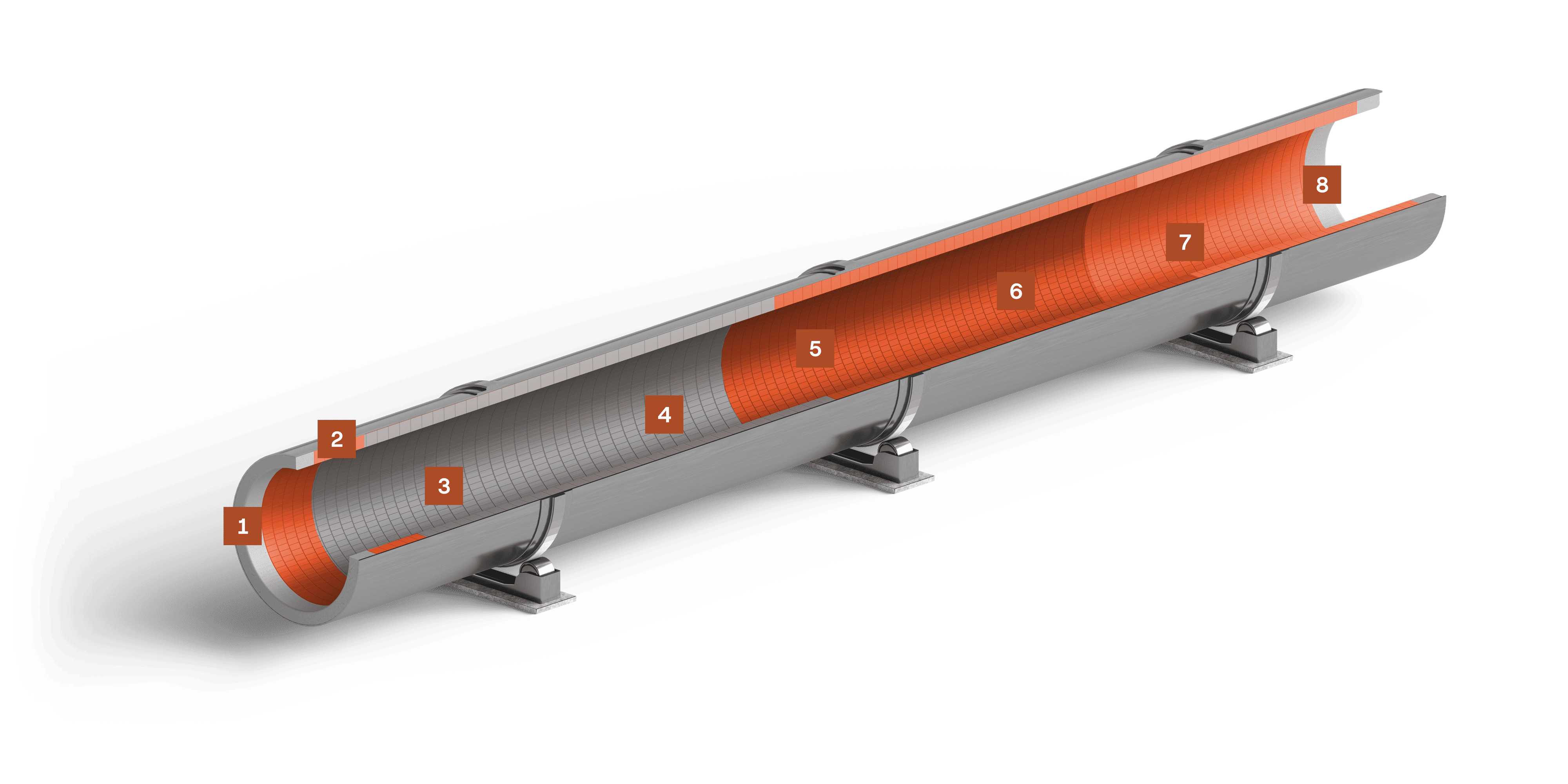
La zone terminale du four – appelée "couronne de nez" – se caractérise par des conditions similaires à celles de la zone de sortie. Les températures y sont variables et la charge traitée exerce une pression mécanique importante, ce qui impose l’utilisation de matériaux ayant une excellente résistance mécanique. La conception du four rotatif prévoit l’emploi de produits monolithiques, coulés directement en place à l’aide de bétons réfractaires lors des campagnes de maintenance. Les propriétés clés de ces matériaux sont la résistance à la compression et à l’abrasion, ce qui garantit l’intégrité structurelle sous des charges intenses. Les produits recommandés sont les bétons haute alumine de la gamme MULCAST et les bétons à faible teneur en ciment de la gamme PCOCAST.
Dans la zone de refroidissement, le principal défi pour les matériaux réfractaires est le choc mécanique provoqué par l'éclatement du clinker, qui change de volume en raison de fluctuations thermiques soudaines. Les températures dans cette zone varient entre 900 et 1100 °C. Le revêtement est constitué d’une seule couche de briques en coin. Les propriétés essentielles requises pour les matériaux réfractaires sont une résistance élevée aux chocs thermiques ainsi qu’une résistance mécanique exceptionnelle aux impacts et à l’abrasion.
Dans cette zone, le clinker fritté lors de l’étape précédente commence à se refroidir progressivement, les températures chutant jusqu’à environ 1200 °C. Malgré la baisse de température, on utilise encore des matériaux réfractaires à haute résistance aux changements thermiques dynamiques. À ce stade, les produits magnésie-spinelle sont privilégiés, car ils garantissent une protection continue du revêtement tout en limitant les contraintes thermiques.
La zone de cuisson est la partie du four où les températures atteignent les niveaux les plus élevés, jusqu’à 1500 °C, où ont lieu les transformations chimiques complètes. La charge de calcaire y est soumise à des réactions intenses qui mènent à la formation des minéraux du clinker. Dans cette zone, on recommande des produits magnésiens, qui, grâce à leurs propriétés, offrent une résistance adaptée aux conditions thermiques et chimiques extrêmes du processus de cuisson.
Dans cette zone, l’exposition thermique est très intense, avec des températures dépassant 1200 °C. La zone est caractérisée par des conditions instables et fluctuantes, et le revêtement, constitué d’une seule couche de briques en coin, doit résister aux changements thermiques rapides. On y utilise principalement des produits magnésie-spinelle, tandis qu’à la frontière avec la zone de sécurité, on installe des matériaux alumino-silicatés de très haute qualité, assurant une protection optimale contre les chocs thermiques.
Les températures y dépassent 1000 °C, ce qui favorise la décomposition du calcaire. Les conditions dans cette zone sont variables et fortement dépendantes du processus, notamment lorsque la part de RDF dans le combustible augmente. Le revêtement, réalisé avec une seule couche de briques en coin, est exposé à des attaques d’alcalis, des eutectiques liquides, des contraintes instables, ainsi qu'à des agressions chimiques et thermiques provenant de la charge et des combustibles alternatifs. Le choix des matériaux réfractaires doit être suffisamment flexible pour répondre aux conditions d’exploitation changeantes. Dans cette zone, on utilise des produits haute alumine avec SiC – tels que ABRAL ou ANDALUX – ainsi que des produits BAUXITEX liés chimiquement.
Dans cette zone, en plus de l’abrasion mécanique intense provoquée par le mouvement de la charge, le revêtement est exposé à l’action d’alcalis provenant des matières premières et des combustibles. Les températures sont maintenues entre 1000 et 1100 °C. Le revêtement est réalisé avec une seule couche de briques en coin. Les matériaux réfractaires utilisés dans cette zone doivent offrir une résistance mécanique élevée ainsi qu'une excellente résistance à la corrosion, afin d'assurer le fonctionnement continu du système dans des conditions de processus variables. Les produits de la gamme ABRAL, réputés pour leur résistance accrue à la corrosion et à l’abrasion, sont bien adaptés à cette application.
Dans cette zone, qui marque le début du revêtement du four, le principal danger est l’abrasion mécanique intense causée par le mouvement de la charge. Pour faire face à ce défi, on utilise des bétons réfractaires résistants à l’abrasion. Il est essentiel d’utiliser un béton haute alumine. Les produits recommandés sont les bétons à teneur moyenne en ciment de la gamme MULCAST ou les bétons sans ciment GELCAST, offrant une résistance mécanique et une durabilité suffisantes.
Comment pouvons-nous vous aider ?
Vous souhaitez recevoir un conseil gratuit ou poser une question sur le choix d’un revêtement réfractaire? Laissez-nous vos coordonnées – nous vous rappellerons!
Contactez-nousComment optimiser le choix des formats et la disposition des briques pour réduire la formation d’anneaux et de dépôts de clinker ?
Quel matériau convient le mieux à un four alimenté avec un combustible à forte teneur en RDF ?
Quel matériau convient le mieux à un four alimenté avec un combustible à forte teneur en RDF ?
Refroidisseur et tête de four
Le refroidisseur et la tête de four ont pour fonction de refroidir le clinker à la sortie du four rotatif. Dans la tête de four, la température peut atteindre 1100 °C, tandis que dans le refroidisseur, elle diminue progressivement – d’environ 800 °C dans la zone chaude jusqu’à 100 °C dans la zone froide. La structure du refroidisseur comprend plusieurs zones distinctes : zone chaude, zone froide, toiture ainsi que le bullnose ring. Des matériaux réfractaires alumino-silicatés sont utilisés dans toutes les parties du refroidisseur. L’usure du revêtement de la tête de refroidisseur est principalement causée par les chocs thermiques dus à l’explosion du clinker ainsi que par l’abrasion mécanique liée à son mouvement. À cela s’ajoutent des variations thermiques cycliques, ainsi que les effets destructeurs chimiques et abrasifs des gaz de procédé. Une zone particulièrement exposée à l’usure est le bullnose, situé au contact direct des gaz à haute température et du clinker. PCO propose une large gamme de matériaux réfractaires pour les refroidisseurs, y compris des bétons réfractaires, des éléments préfabriqués et des briques bauxitiques.
Portée: Conception du garnissage Fourniture des matériaux réfractaires Services de montage du garnissage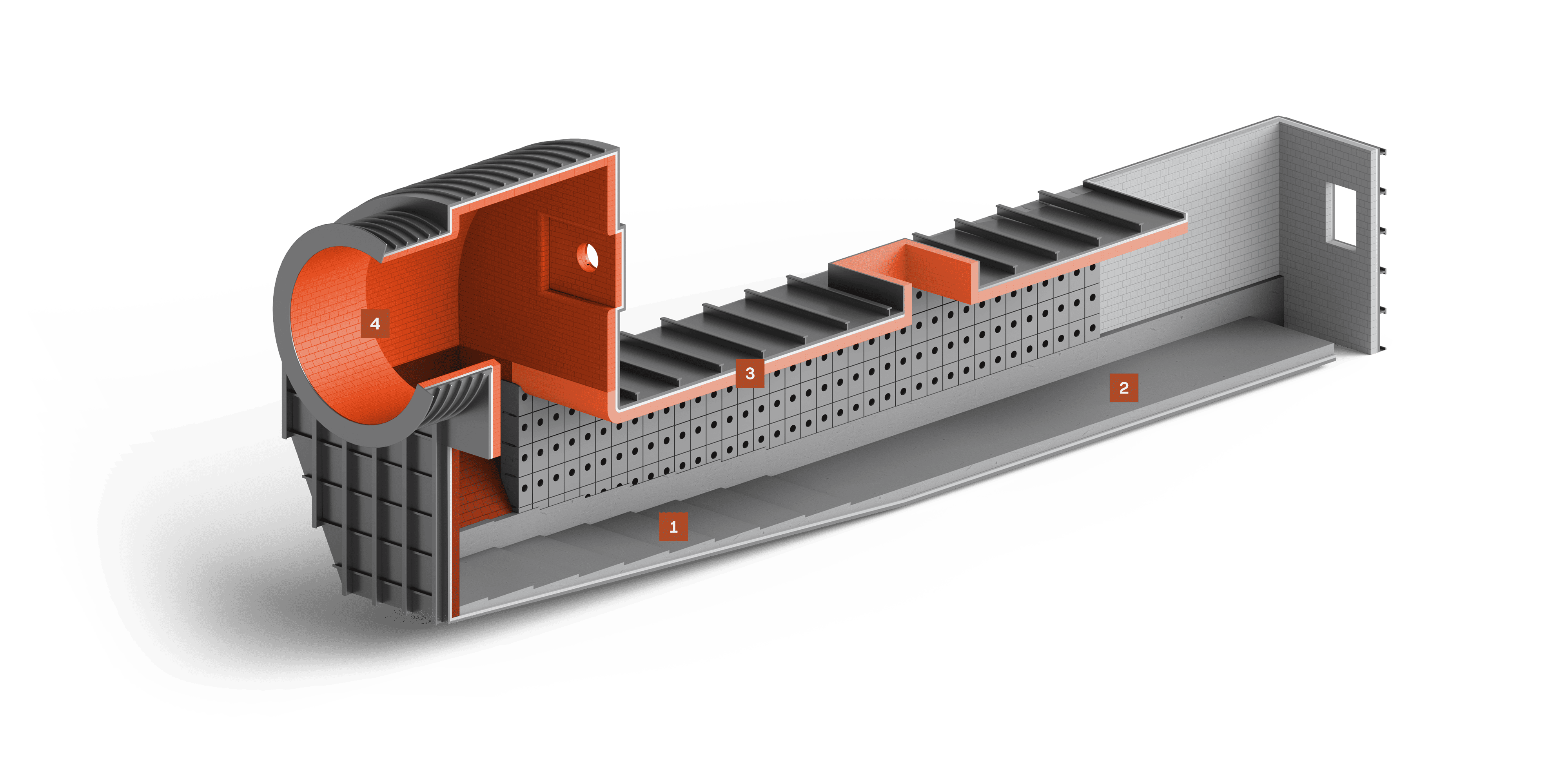
Dans cette zone, la température atteint jusqu’à 1000 °C, avant de chuter brusquement en direction de la grille mobile. Ce profil thermique génère des chocs thermiques violents. Sur le lit de clinker, l’usure du revêtement réfractaire est essentiellement causée par une abrasion mécanique intense, liée au déplacement du matériau ainsi qu’à l’action dynamique des flux d’air et des poussières. Le revêtement est constitué d’éléments préfabriqués en béton, souvent utilisés sous forme de murets de retenue. Ceux-ci assurent une isolation thermique efficace ainsi qu’une bonne stabilité mécanique dans un environnement marqué par d’importantes variations de température. Le bon comportement du revêtement dans cette zone repose sur l’emploi de béton haute teneur en alumine, capable de résister à la fois aux chocs thermiques sévères et à une forte abrasion. Ce type de matériau conserve ses propriétés fonctionnelles même en cas de chute rapide de température et de sollicitations mécaniques importantes.
La zone froide est caractérisée par des conditions thermiques très stables, avec une température qui ne dépasse pas 500 °C. En raison d’une exposition plus modérée à la chaleur et de variations moins dynamiques, cette partie du refroidisseur est faiblement sollicitée d’un point de vue thermique et mécanique. De ce fait, le revêtement y est rarement sujet à des opérations de maintenance. Il est constitué de béton projeté, qui assure une surface uniforme et cohérente. Par ailleurs, le long de la grille, on installe des murets de retenue préfabriqués, confectionnés à partir de réfractaires de qualité inférieure, tels que le MULCAST BN45M S5.
La toiture, utilisée à la fois dans la zone chaude et la zone froide, est soumise à une abrasion provoquée par les poussières volatiles, ainsi qu’à des variations thermiques rapides tout au long du refroidisseur. Les matériaux réfractaires doivent y présenter une résistance élevée à la fois à l’usure mécanique et aux fluctuations thermiques. Pour garantir leur efficacité, les matériaux utilisés dans cette section doivent posséder d’excellentes propriétés mécaniques et thermiques, notamment dans la zone chaude, où l’ajout de carbure de silicium améliore considérablement la résistance du revêtement. Dans les zones froides, la priorité est d’assurer la continuité et la durabilité du revêtement à des températures plus basses, ce qui permet un fonctionnement prolongé sans nécessiter d’interventions fréquentes.
La tête du four a pour principale mission de collecter le clinker et de le transférer vers le refroidisseur, dans des conditions marquées par des sollicitations mécaniques et thermiques intenses. Une attention particulière doit être portée à la zone appelée bullnose ring, une paroi verticale qui constitue l’une des parties les plus vulnérables de l’installation. Dans cette zone, le revêtement est soumis à de fortes contraintes mécaniques dues aux impacts du clinker tombant, ainsi qu’à des variations thermiques soudaines. La combinaison de ces effets impose aux matériaux réfractaires des exigences de très haut niveau. Le revêtement de la tête du four est le plus souvent réalisé à partir de briques moulées, qui garantissent une bonne stabilité thermique et une isolation efficace, réduisant les pertes de chaleur et limitant l’influence des facteurs extérieurs. En revanche, dans le cas du bullnose ring, soumis à des charges mécaniques extrêmes, on utilise des bétons réfractaires de qualité supérieure ou des éléments préfabriqués en béton.
Comment pouvons-nous vous aider ?
Vous souhaitez recevoir un conseil gratuit ou poser une question sur le choix d’un revêtement réfractaire? Laissez-nous vos coordonnées – nous vous rappellerons!
Contactez-nousQuel béton réfractaire assure la plus haute résistance à l’abrasion dans la zone du bullnose ring ?
Comment éviter les dommages dus aux chocs thermiques pendant les variations de flux de gaz plus froids ?
Comment concevoir des murs de retenue préfabriqués pour protéger le revêtement contre les vibrations de la grille ?
Four vertical à chaux
Le four vertical, utilisé dans la technologie de production de chaux, fonctionne à des températures qui dépassent fréquemment les 1100 °C. Le processus de calcination nécessite une répartition de la chaleur homogène et maîtrisée sur toute la hauteur du four. La pierre calcaire introduite dans le four est mélangée à du coke ou à de l’anthracite, et la combustion du combustible génère une température élevée permettant de transformer le calcaire en chaux vive, c’est-à-dire en oxyde de calcium (CaO). Dans l’industrie de la soude, la production de chaux se fait dans des fours opérant à des températures légèrement inférieures à celles de la production classique de chaux, ce qui réduit les exigences en matière de matériaux réfractaires et de systèmes de chauffage. En revanche, dans les sucreries, les fours utilisés pour le traitement de la chaux sont soumis à des conditions de fonctionnement spécifiques. On y observe fréquemment des variations de température ainsi que des arrêts récurrents. Cela nécessite l’emploi de matériaux réfractaires robustes, capables de supporter des cycles thermiques répétés sans usure excessive. Dans ce type de four, le processus de calcination ne s’effectue pas de manière continue, ce qui le distingue des fours utilisés dans d’autres secteurs comme la chaux industrielle ou la production de soude.
Portée: Conception du garnissage Fourniture des matériaux réfractaires Services de montage du garnissage
La zone de préchauffage est l’endroit où la pierre calcaire, mélangée au combustible, est chargée de manière cyclique. Ce processus engendre une usure mécanique importante du revêtement due au déplacement constant de la charge, tout en étant exposé à des températures élevées. Les matériaux utilisés dans cette zone doivent présenter une grande résistance à l’abrasion, ce qui justifie le choix de produits alumino-silicatés de la gamme EXTRATON. Par ailleurs, afin de minimiser les pertes de chaleur, une couche isolante composée de produits ISOLUX associée à de la laine minérale garantit une excellente performance thermique. La clé de la durabilité du revêtement dans cette zone réside dans la combinaison de propriétés mécaniques élevées et de très bonnes capacités d’isolation, permettant de maintenir des paramètres thermiques optimaux dans le four.
La zone de cuisson, également appelée zone de calcination, est l’endroit où s’effectue la transformation intensive de la charge, telle que la pierre calcaire ou dolomitique. La température de cuisson ainsi que la composition de la charge influencent les contraintes chimiques et thermiques spécifiques, y compris le risque d’hydratation. Dans des conditions normales de fonctionnement, les oxydes d’aluminium (Al₂O₃) et de silicium (SiO₂) restent chimiquement stables, ce qui limite leur réaction avec l’eau. Toutefois, il est essentiel d’utiliser des matériaux qui conservent leur stabilité même en présence d’humidité. Dans cette zone, le choix se porte sur des produits dotés d’une résistance élevée à l’hydratation et d’une stabilité chimique à haute température. Les matériaux des gammes MULITEX, ANDALUX et BAUXITEX répondent à ces exigences et garantissent une longue durée de vie du revêtement, même dans un environnement chimique évolutif.
Dans la zone de refroidissement, le revêtement est exposé à une diminution progressive de la température. Cela implique une sollicitation thermique moins intense, mais requiert néanmoins une résistance suffisante à l’abrasion. Dans un four à un seul puits, le processus de refroidissement s’effectue de manière uniforme sur toute la hauteur de cette zone, ce qui permet d’appliquer des solutions isolantes homogènes. Les matériaux chamottés conviennent parfaitement pour cette partie du four, offrant à la fois une bonne résistance à la compression et une excellente tenue à l’abrasion. Plus particulièrement, les produits de la gamme SUPERTON sont recommandés dans cette zone. Pour les fours à puits unique, la couche isolante est constituée sur toute la hauteur de modules ISOLUX, complétés par de la laine minérale. Cette combinaison forme une barrière thermique continue et réduit les pertes de chaleur de manière efficace.
Comment pouvons-nous vous aider ?
Vous souhaitez recevoir un conseil gratuit ou poser une question sur le choix d’un revêtement réfractaire? Laissez-nous vos coordonnées – nous vous rappellerons!
Contactez-nousQuelles briques haute alumine résistent le mieux à la dégradation chimique due à une exposition prolongée au CO₂ dans l’atmosphère du puits ?
Quelles masses projetées ou damées offrent la meilleure résistance à la désagrégation répétée et à l’attaque de vapeur issue d’une charge calcaire humide ?
Comment optimiser la géométrie des briques, la conception des ancrages métalliques et la configuration des joints pour les fours verticaux de grande hauteur, afin de prendre en compte la dilatation thermique axiale et éviter l’effondrement du revêtement ?
Four Maerz – aperçu des solutions
Le four Maerz, utilisé dans les procédés nécessitant un contrôle précis de la température et une distribution homogène de la chaleur, fonctionne dans des conditions où les revêtements réfractaires céramiques sont exposés à des températures très élevées, souvent supérieures à 1200 °C. Ce qui distingue les fours Maerz des autres fours verticaux est le principe de réversion, un élément central de leur fonctionnement. Deux puits sont utilisés : dans l’un se déroule la calcination de la pierre calcaire, tandis que l’autre sert à l’alimentation en air de combustion. Le principe de réversion signifie que les phases de combustion et de calcination s’inversent régulièrement, ce qui permet une meilleure gestion des flux gazeux, une régulation plus efficace de la température et une utilisation plus rationnelle de l’énergie. En raison du rendement plus élevé de ces installations et des conditions de travail plus sévères, les fours Maerz nécessitent l’utilisation de matériaux réfractaires de qualité supérieure par rapport aux fours verticaux classiques. Les matériaux utilisés doivent présenter une excellente résistance aux chocs thermiques et à l’érosion chimique afin de maintenir l’intégrité du revêtement malgré les variations constantes de fonctionnement. L’optimisation de la répartition thermique et la réduction des pertes de chaleur sont des facteurs essentiels pour garantir l’efficacité de cette technologie et la longévité de l’équipement.
Portée: Conception du garnissage Fourniture des matériaux réfractaires Services de montage du garnissage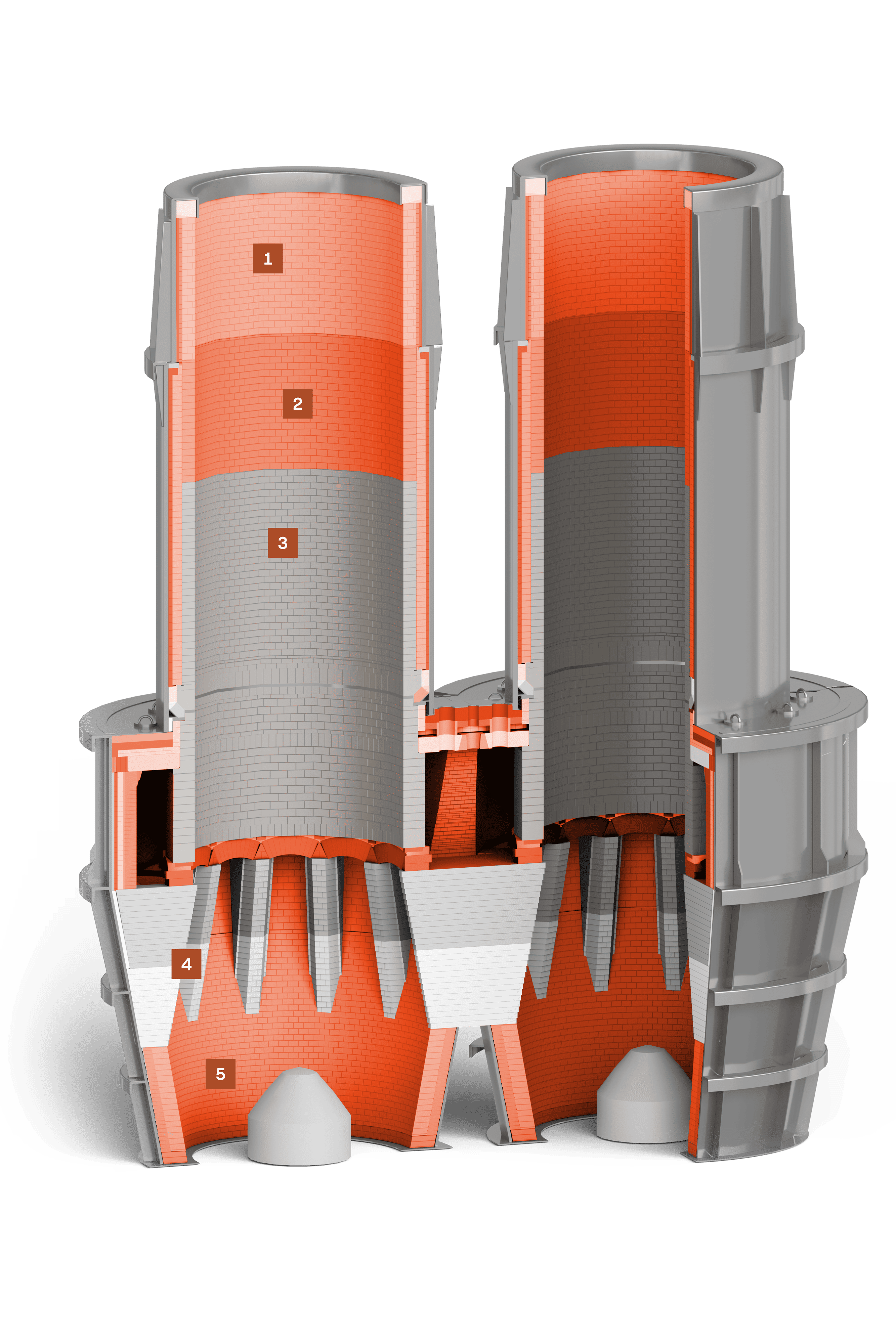
La zone de préchauffage dans le four Maerz s’étend depuis le niveau inférieur des brûleurs jusqu’à la partie supérieure du puits, où la pierre calcaire mélangée au combustible est introduite de manière cyclique. Cette zone est soumise à des contraintes mécaniques et thermiques importantes, résultant du contact direct de la charge avec le revêtement et des conditions thermiques variables. Il est donc essentiel d’assurer une résistance élevée à l’abrasion tout en minimisant les pertes de chaleur, ce qui est fondamental pour l’efficacité du four. La conception du revêtement dans cette zone repose sur l’utilisation de matériaux différenciés selon le profil thermique. Dans la partie inférieure, à proximité des brûleurs, la couche de travail est réalisée avec des matériaux magnésiens-spinel, offrant une très bonne résistance à l’abrasion et aux composés agressifs générés pendant la combustion. Dans la partie supérieure du puits, on utilise des produits alumino-silicatés renforcés contre l’abrasion, en particulier ceux de la gamme EXTRATON.
Afin d’assurer une transition progressive entre la couche magnésienne-spinel et la couche alumino-silicatée, une zone de transition est aménagée à l’aide de matériaux haute alumine à base d’andalousite. De plus, l’espace situé entre la coque en acier et la couche de travail est rempli d’un système d’isolation composé de plaques isolantes de la gamme ISOLUX et de nappes en laine minérale. Dans certaines conceptions, une couche d’isolation supplémentaire, faite de produits SUPERTON ou EXTRATON, est intercalée entre la couche de travail et le système isolant principal. L’ensemble du revêtement du puits est terminé par une couche de béton conventionnel, qui joue le rôle de finition et de renfort de la structure.
La zone de cuisson s’étend du niveau inférieur des voûtes de soutien jusqu’au niveau inférieur des brûleurs (ou lances à gaz). Dans cette section du four, la charge subit une calcination intense qui entraîne des températures très élevées et une exposition à des agents chimiques agressifs, variables selon la nature du matériau traité – calcaire ou dolomie, par exemple. PCO Żarów fournit les matériaux réfractaires servant de couche de protection et d’isolation dans cette zone. L’ensemble du revêtement du puits, à partir de la zone de dilatation vers le haut, repose sur l’utilisation de formes spéciales telles que les modèles AS1, AS2 et similaires, fabriquées à partir des matériaux des gammes MULITEX ou ANDALUX. Cette approche garantit non seulement la stabilité de la structure, mais aussi une bonne résistance aux conditions thermiques et chimiques fluctuantes de la zone de cuisson.
La structure du four Maerz comporte plusieurs éléments porteurs, tels que les piliers, les voûtes inter-piliers, les voûtes plates et le canal de jonction, tous réalisés en bétons à faible teneur en ciment ou sans ciment. La construction des piliers nécessite l’utilisation combinée de briques en forme de nez, de types VK-76x et WL-76, qui assurent une excellente stabilité mécanique. Dans le cas des fours Maerz sans piliers, la base du cylindre suspendu est également réalisée avec des bétons de haute performance. Pour la voûte plate, une couche isolante est appliquée à l’aide de bétons légers de type ISOCAST ou ISOGUN, complétés par une couche de laine minérale.
La zone de refroidissement dans le four Maerz s’étend depuis la première couche du revêtement jusqu’au niveau inférieur des voûtes inter-piliers. Dans cette zone, la température diminue progressivement, ce qui est essentiel à la stabilisation du processus de refroidissement. Malgré la baisse de température, le revêtement est soumis à de fortes sollicitations mécaniques et abrasives, dues à la fois au mouvement de la charge et aux contraintes thermiques générées pendant la phase de refroidissement. La couche de travail est constituée de briques chamottées des gammes SUPERTON ou EXTRATON, parfaitement adaptées à ce type de conditions. Les espaces entre les piliers sont généralement maçonnés avec des briques EXTRATON. La couche d’isolation repose sur des modules ISOLUX, associés à des plaques en silicate de calcium et des nappes en laine minérale, qui forment une barrière thermique continue.
Comment pouvons-nous vous aider ?
Vous souhaitez recevoir un conseil gratuit ou poser une question sur le choix d’un revêtement réfractaire? Laissez-nous vos coordonnées – nous vous rappellerons!
Contactez-nousQuel design de briques pour les piliers permet d’augmenter la résistance mécanique du revêtement ?
Quels matériaux réfractaires conviennent le mieux pour une exposition simultanée à l’abrasion et à l’attaque chimique pendant la calcination du calcaire ?
Comment concevoir les couches de transition et de protection entre les matériaux basiques et alumino-silicatés afin de tenir compte de la dilatation thermique et d’éviter les fissures pendant les phases de chauffage et de refroidissement ?
Four rotatif à chaux pour la production de pulpe
Le four rotatif à chaux utilisé dans le procédé Kraft permet de récupérer la chaux à partir d’un lait de chaux, en vue de sa réutilisation dans la production de pâte à papier. Le revêtement réfractaire de ce type de four est généralement constitué de deux couches, ce qui garantit une durabilité adéquate et une résistance suffisante aux conditions extrêmes d’exploitation. Les principaux facteurs de dégradation du revêtement sont les changements de température rapides, les réactions chimiques entre les briques et le lait de chaux, ainsi que les variations de pression et de contraintes générées par la rotation du four. Selon les zones fonctionnelles du four, différents types de matériaux réfractaires sont employés. Les zones d’entrée et de sortie sont protégées par des bétons réfractaires offrant une haute résistance aux chocs thermiques et à la corrosion chimique, complétés par des briques chamottées et andalousites. Dans la zone de cuisson, on utilise le plus souvent des briques andalousites enrichies en P₂O₅, qui assurent une excellente tenue à des températures extrêmes, à des environnements chimiques agressifs et à des contraintes mécaniques élevées.
Portée: Conception du garnissage Fourniture des matériaux réfractaires Services de montage du garnissage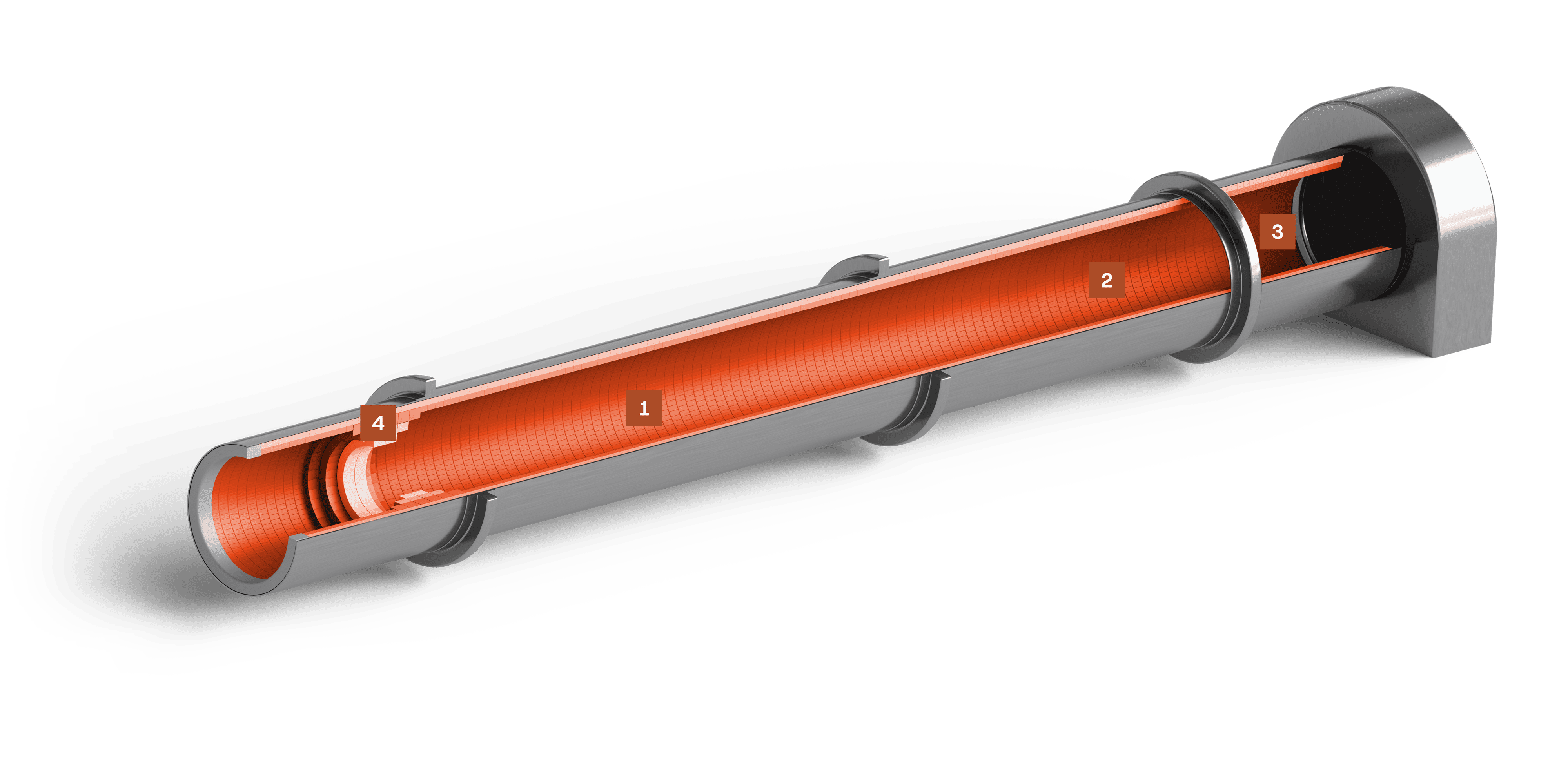
La zone de préchauffage du four rotatif à chaux couvre la montée en température de 200 °C à environ 1100 °C. C’est dans cette section que le lait de chaux est séché puis partiellement calciné. Le revêtement réfractaire y est exposé à une forte abrasion ainsi qu’à une érosion chimique importante. Le lait contient en effet divers composés chimiques comme des sels alcalins, du soufre et des chlorures, ce qui accroît les risques d’infiltration corrosive dans la structure du revêtement. Un autre facteur de risque est l’humidité de la charge, pouvant atteindre 20 %. Il est donc indispensable que le revêtement présente une faible porosité et une résistance à l’absorption d’eau. Dans la zone de travail, on recommande des briques chamottées de qualité supérieure, issues de la gamme EXTRATON, qui présentent une très bonne tenue aux attaques alcalines et une faible porosité. Plus près de la zone de cuisson, où les températures sont plus élevées, il convient de passer à des produits haute alumine ou liés chimiquement, comme ceux de la gamme ANDALUX.
Dans cette zone, les températures se situent entre 1100 °C et 1300 °C sur toute la longueur. Les conditions d’exploitation sont instables, soumises à des contraintes thermiques élevées, dues principalement au rayonnement intense de la flamme, mais aussi à l’agressivité chimique des gaz de combustion. Le lait de chaux y est soumis à un processus de frittage, transformant la boue carbonatée en chaux vive (CaO). Le revêtement réfractaire doit donc être résistant au choc thermique, aux températures élevées et à la fois à la corrosion chimique et à l’usure mécanique. Le revêtement est conçu comme une structure à deux couches. Pour la zone de travail, on recommande l’utilisation de briques andalousites liées chimiquement, issues de la gamme ANDALUX, qui combinent stabilité mécanique, résistance chimique et durabilité à haute température.
Il s’agit de la section la plus courte du four rotatif, généralement limitée à quelques mètres avant l’entrée dans le refroidisseur. La température y chute rapidement, passant d’environ 1000 °C à près de 200 °C. Ce refroidissement brutal engendre de forts chocs thermiques. Le clinker déjà calciné agit comme un agent abrasif en se déplaçant contre le revêtement. La rotation du four et le rétrécissement du diamètre de l’enveloppe métallique à cet endroit créent des contraintes mécaniques supplémentaires qui peuvent fragiliser le revêtement. Le revêtement est construit sur deux couches. Dans les sections rétrécies, on applique dans la zone de travail un béton haute alumine, tandis que la couche isolante est composée de plaques moulées ISOLUX à haute résistance à la compression.
Le seuil de charge, fabriqué en céramique réfractaire, a pour fonction de régulariser la distribution de la charge à la sortie du four rotatif. Dans cette zone, le revêtement est soumis à une forte abrasion et à des contraintes mécaniques continues. La configuration recommandée repose sur l’utilisation de briques andalousites de très haute performance, qui permettent de contrôler le mouvement du matériau et de garantir un fonctionnement stable dans cette zone critique.
Comment pouvons-nous vous aider ?
Vous souhaitez recevoir un conseil gratuit ou poser une question sur le choix d’un revêtement réfractaire? Laissez-nous vos coordonnées – nous vous rappellerons!
Contactez-nousQuel matériau convient comme revêtement de travail lorsqu’il est en contact avec du goudron ou des acides organiques ?
Comment éviter les fissures du revêtement causées par la différence de dilatation entre la coque métallique, la couche isolante et la couche de travail ?
Comment détecter l’usure excessive du revêtement réfractaire dans les zones où les dépôts s’accumulent ou à proximité du brûleur ?
Pourquoi PCO
Installation incluse avec la fourniture des réfractaires – gestion de projet simplifiée et garantie unique de qualité.
Gamme complète de produits réfractaires alumino-silicatés pour l’industrie du ciment et de la chaux
Notre propre équipe de concepteurs et d’ingénieurs prête à relever tous les défis
Produits et services sélectionnés
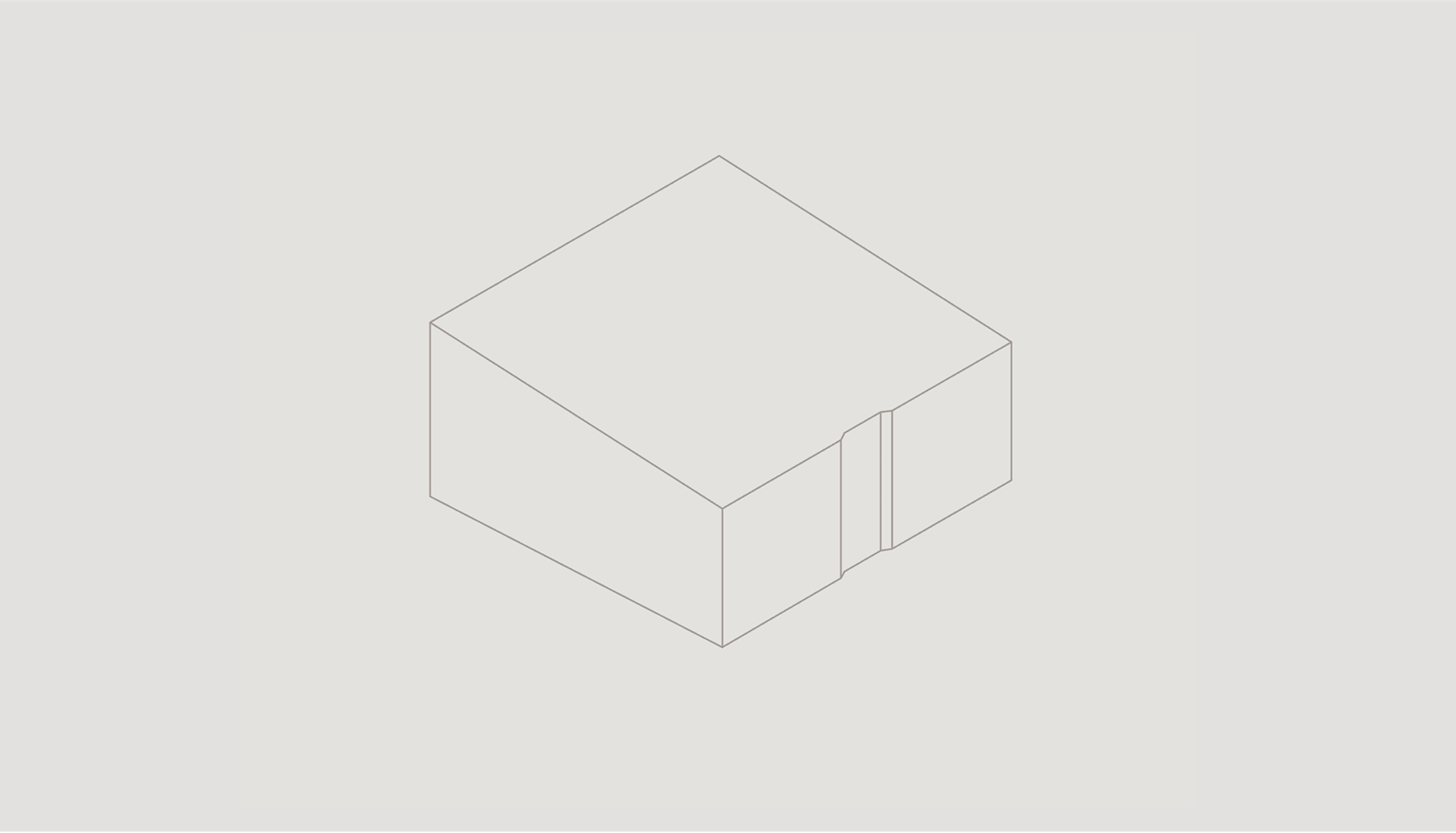
Gamme de produits ABRAL
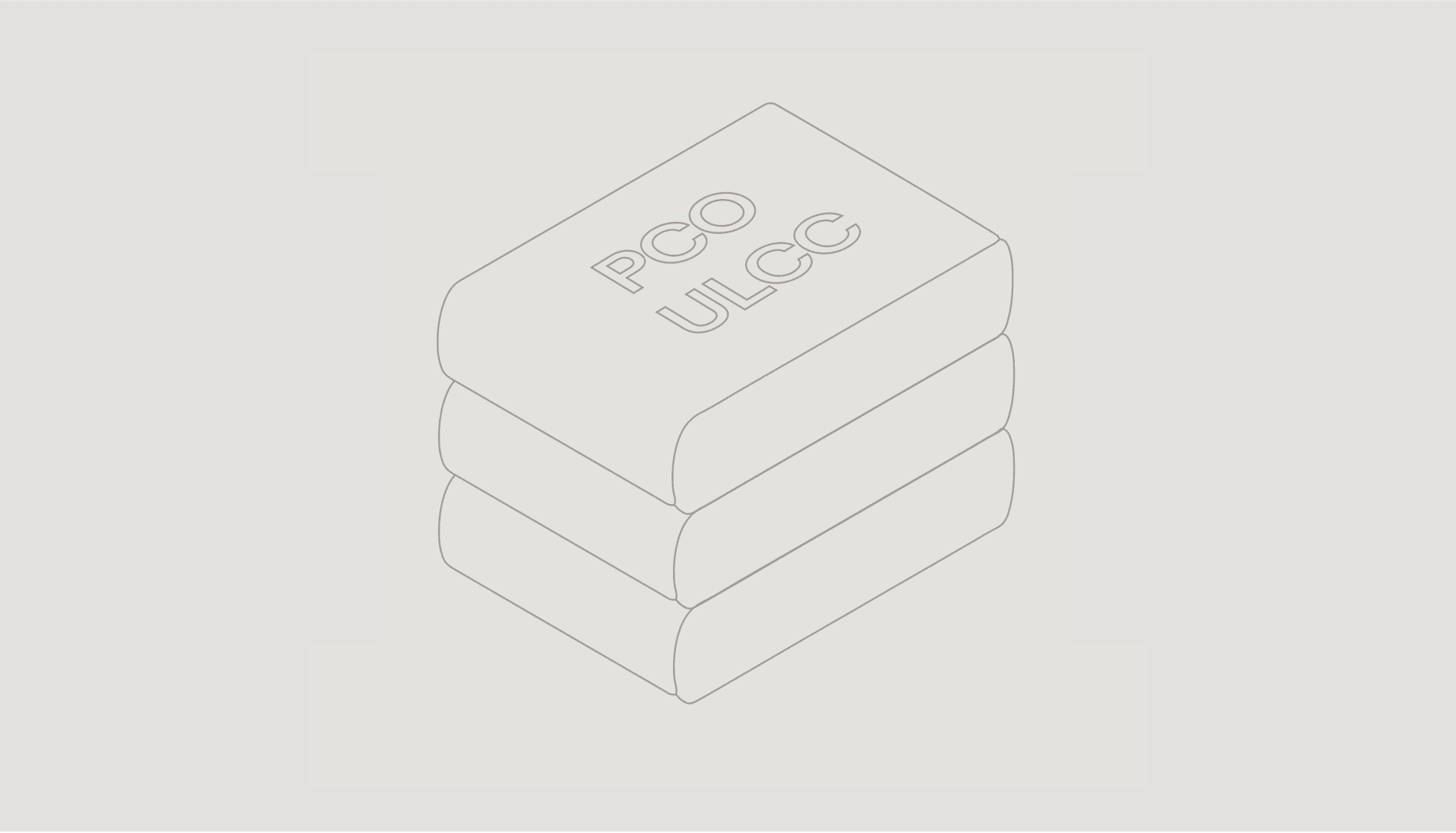
Bétons réfractaires ultra-bas en ciment (ULCC)

Supervision des projets de revêtement pour fours verticaux et fours Maerz
Contactez-nous
Veuillez sélectionner l'option qui décrit le mieux le sujet que vous souhaitez discuter avec nous. Cela nous aidera à orienter votre demande vers la bonne personne chez PCO.